Ensuring a Safer Tomorrow: The R15.08 Standard Paves the Way for Human-Robot Coexistence
The dawn of autonomous mobile robots (AMRs) in industrial settings has ushered in a new era of productivity and efficiency. However, with great innovation comes the need for stringent safety measures to protect human workers and ensure seamless integration into existing workflows. Enter the R15.08 safety standard, a comprehensive set of guidelines developed by the Robotic Industries Association (RIA) to address the unique challenges posed by these advanced machines.
The R15.08 standard lays the foundation for the safe design and manufacturing of Industrial Mobile Robots (IMRs) and their attachments. It provides a detailed framework for risk assessment and the necessary safety requirements that manufacturers must meet to ensure the well-being of human operators in proximity to these robots. As we stand on the brink of a robotic revolution, the R15.08 safety standard is not just a regulatory requirement; it’s a pivotal step towards harmonizing human-robot collaboration in the factories of the future.
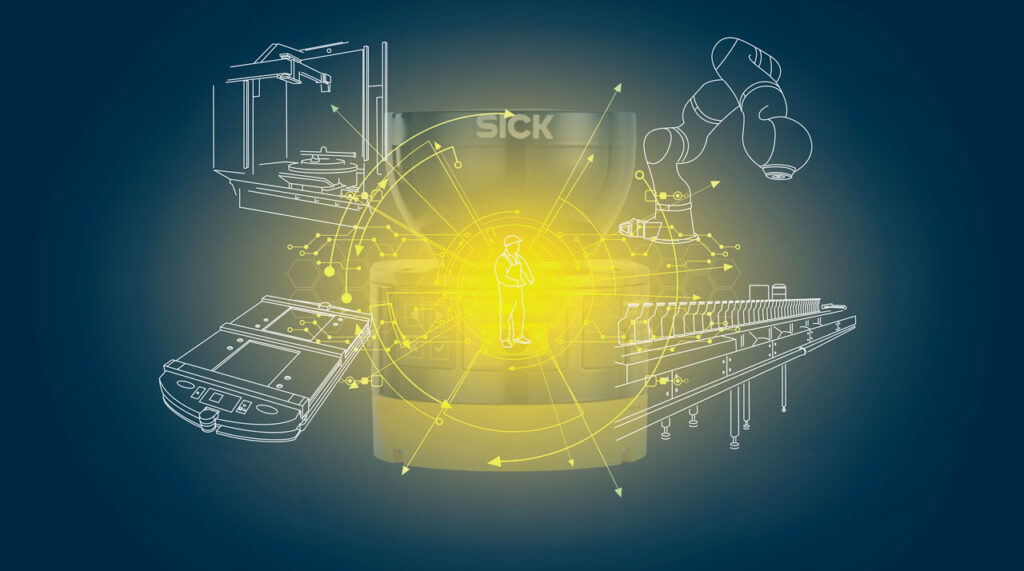
We did a recent webinar covering all you need to know about this standard, but we’ve also got answers to some frequently asked questions from leading safety expert, Chris Soranno, Manager of International Safety Standards at SICK North America.
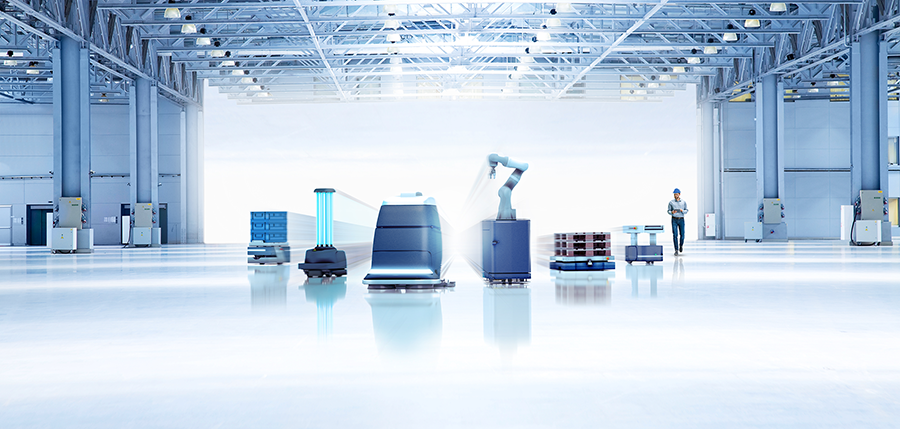
Q: What is the difference between AGV and IMRs?
Within the scope of R15.08, there is a distinction made between AGV (automated guided vehicles) and AMR (autonomous mobile robot). The introduction of ANSI/RIA R15.08-1-2020 states:
The fundamental difference between AGVs and AMRs is characterized by how they traverse the specified operating environment. An AGV traverses the specified operating environment automatically along predefined guide paths (virtual or physical) using collision avoidance and can adjust from their guidepath. AMRs traverse the specified operating environment autonomously which requires the ability to navigate using obstacle avoidance and collision avoidance by detecting obstacles using sensors and adjusting paths by computing an obstacle-free path through free space rather than using a predefined path.
Building on those concepts, an IMR (industrial mobile robot) can be categorized as one of 3 types, as described in the Scope (Clause 1) of ANSI/A3 R15.08-2-2023:
- IMR Type A: AMR without any attachments. Such platforms consist of the mobile platform, alone, and are typically intended to be used as the basis for an IMR Type B or C.
- IMR Type B: AMR with either passive or active attachments, excluding manipulators. Such active attachments can include roller tables, conveyors, and linear lift devices (e.g., picking attachments).
- IMR Type C: IMR constructed from an AMR or an AGV as a mobile platform with a manipulator as the attachment.
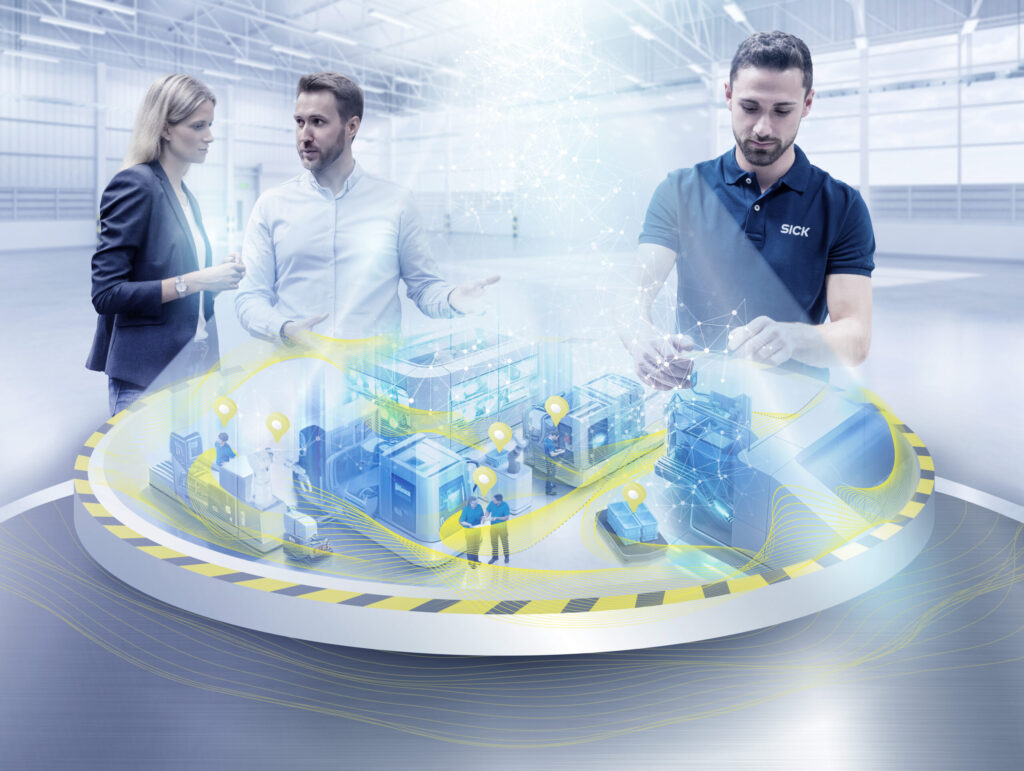
Does the R15.08 standard cover applications for classified environments per NFPA 70?
Currently there are no European (EN) or international (ISO / IEC) standards with an identical scope as R15.08. However, efforts are currently underway to identify gaps between existing standards (such as EN ISO 10218 and EN ISO 3691-4) specific to the application of manipulators in use while on a mobile platform. This ongoing work is just beginning and may take some years before the output(s) of this effort are published and available for reference.
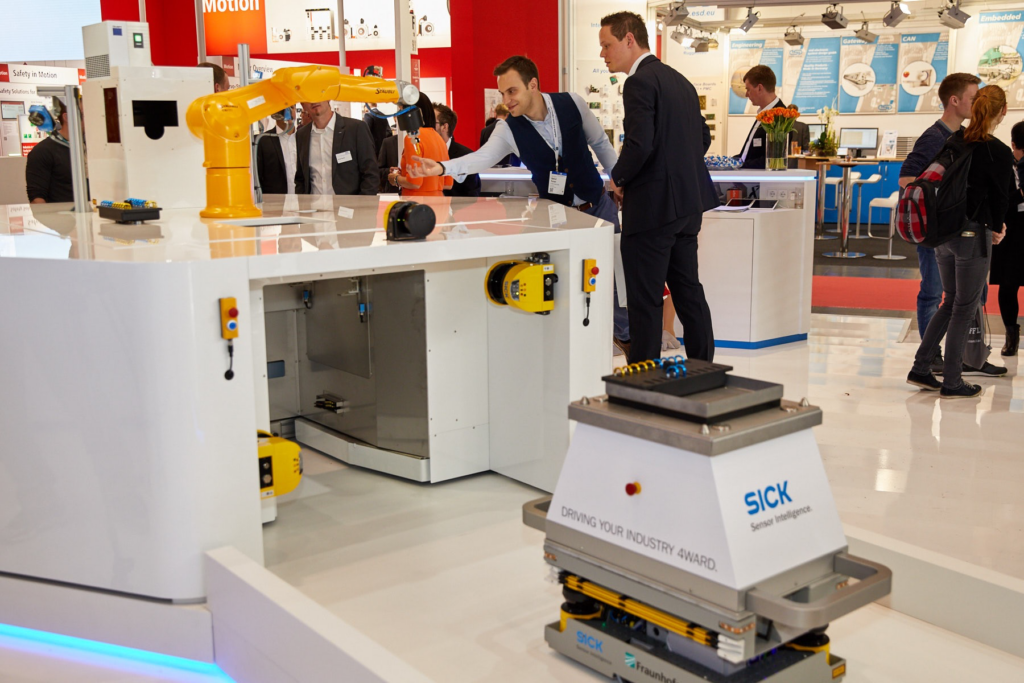
R15.08 does point to R15.06 for manipulators on IMR Type C's. R15.06 requires PLd/SIL2 like the ISO standard. Does this mean IMR Type C's with manipulators require PLd/SIL2 at least for the manipulator?
The R15.08 series of standards does indeed require that manipulators used on Type C IMRs comply with the requirements of R15.06 (the U.S. National adoption of ISO 10218). Furthermore, R15.06 establishes performance requirements for the safety-related parts of the control system (SRP/CS) to meet PL=d with structure category 3 (according to ISO 13849-1) or SIL 2 with a hardware fault tolerance of 1 with a proof test interval of not less than 20 years (according to IEC 62061).
However, upon closer review, R15.06 allows other control system performance of the SRP/CS as a result of a comprehensive risk assessment (see ANSI/RIA R15.06-2012; Clause 5.4.3 of Part 1 and Clause 5.2.3 of Part 2).
Furthermore, the ISO 10218 series has recently been revised and is anticipated to be published soon. The intent is that the revised standards will again be adopted nationally in the U.S. as a new revision to R15.06. The upcoming revision of ISO 10218-2 includes a new normative Annex C which provides information for determining safety function performance levels – and this annex is very similar to the content of Annex C of both R15.08-1 and -2.
Therefore, the scalable approach in R15.08 is both compatible and aligned with the requirements of the existing and future revisions of R15.06.
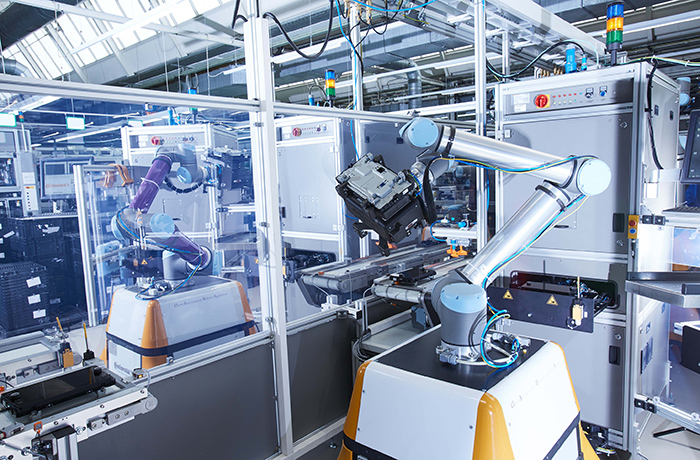
When we get to the calculation of number of people exposed, how do we factor in the combination of direct exposure and incidental? The equation doesn't seem to allow for this combination.
Annex C of R15.08-2 provides guidance on this topic, and in particular Table C.1. When estimating Exposure and determining the effect of persons exposed to the IMR working space, the threshold guidance for any number of persons exposed incidentally (not related to any specific risk) is:
Nr = N x 0.1
where:
Nr = factor for consideration of the number of affected persons
N = number of affected persons exposed
For direct exposure (also referred to as task-based interactions associated with intended use), Nr = N.
Furthermore, each ‘risk’ to be assessed is a 1:1 combination of a task + a hazard. In a typical scenario, the ‘hazard’ may be the same (presumably an IMR), but the ‘task’ is different for those persons directly exposed vs. the persons who are incidentally exposed. This would result in at least 2 separate line items in the risk assessment (maybe more if multiple hazards exists (other hazard sources). The table below identifies 4 possible ‘risks’ to be assessed individually based on 2 tasks x 2 hazard sources:
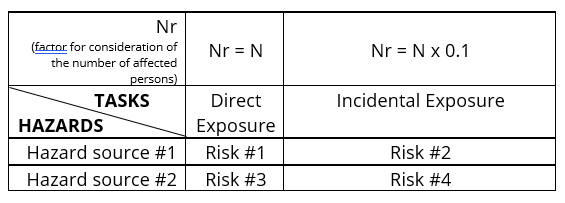
The benefit of this level of detail in the risk assessment process is that it allows for differentiation between direct and incidental exposure, and in turn, opens the possibilities for different risk reduction measures. If someone were to choose NOT to be more detailed in the risk assessment, then a simplified approach must account for the worse-case scenario: all persons have direct exposure. In an example where 2 persons have direct exposure and 1 person has incidental exposure, this would result in a single task/hazard pair where Nr = 3.
Are we allowed to have both a robot arm and a base moving/operating at the same time?
The short answer is: Absolutely!
This was the origin of the R15.08 project. The standard for fixed industrial robot systems (R15.06 in the U.S., or ISO 10218 internationally), states that it does not cover all hazards related to manipulators integrated with mobile platforms. However, the past 10-15 years have seen many innovative designs on the market where a manipulator and the associated mobile platform are both in operation simultaneously. Therefore, R15.08 specifically addresses the hazards derived from these unique applications.
When will Part 3 of R15.08 be published?
The goal is for R15.08-3 to be available sometime in 2025. This standard will describe user requirements for safe operation of IMRs and IMR systems.