Compressed air monitoring delivers energy savings and cuts costs for bottling plant.
Electricity is one of the most expensive resources used in the production process for beverage companies. Generating compressed air consumes large quantities of electricity. With the sharp rise in energy costs, beverage companies are feeling the impact, including one of our customers.
After installing SICK’s compressed air monitoring solution the FTMg flow sensor combined with the TDC Gateway, and an added a cloud solution in our Field Analytics portfolio our client has experienced reduced consumption and increased savings. Now they can identify and eliminate leaks, inefficiencies, and use data to better understand their processes. They are also able to base energy-use decisions on accurate data analysis and even make production more sustainable.
In the past, this customer had manual checks to identify and reduce compressed air leaks. These checks involved inspecting the equipment at every stage of production, from the manufacturing of bottles, filling of beverages, and even packaging and palletizing. Altogether it was a time-consuming (and costly) affair, often performed on weekends. They wanted an efficient digital monitoring system that also met DIN EN ISO50001 requirements.
From manual to automated monitoring through collaboration
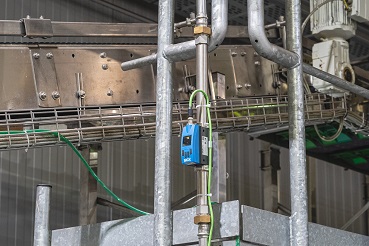
SICK took a holistic approach to optimizing the compressed air energy management in the bottling plant. We proposed a three-component continuous monitoring solution comprised of the FTMg flow sensor, the TDC Gateway, and the cloud solution in the Field Analytics portfolio.
In this collaborative project, forty-nine SICK FTMg flow sensors were installed in five production lines. These sensors were added to record DIN-compliant compressed air consumption measurements and provide real-time data on parameters such as device status, pressure levels, and energy consumption. The SSG-E210GC gateway then transmits the sensor and machine data to the SICK cloud.
After the data is transferred to the cloud, the Digital Services team uses the data for cloud-based advanced analytics on all compressed air equipment across the entire production floor. Once the data is collected, intelligent algorithms evaluate the minimum compressed air consumption during both operation and downtimes.
This data allows us to have perform analysis on the entire production process where we can easily find potential leakages and inefficiencies. Once those are found, the company can make data-based cost calculations to see where they can save money while maximizing production.
Holistic digital solution saves time and resources, with potential for scalability
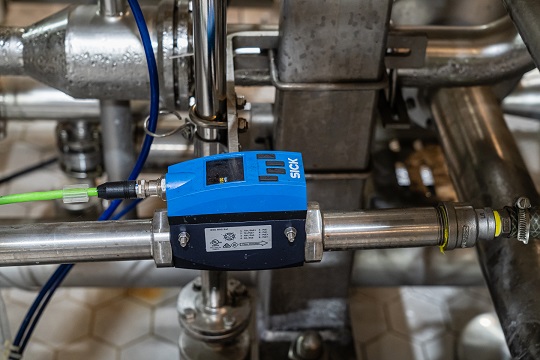
Shifting from time-consuming and labor-intensive manual inspections to a digital continuous monitoring solution was a game changer. They now have 24/7 data visualization. Complete with specific alarms to indicate potential leakages and inefficiencies!
By comparing consumption data from each measuring point on the machines and production lines, they can find cost drivers or over-consumption problems. For example, they can compare the same machine type with the same function in two different lines.
Additionally, if other production sites are added in the future, comparisons across plants are also possible. Continuous monitoring of individual equipment items and the plant gives a clear overview of what is happening on the production lines that draws on statistics, trends and KPIs.
This plant is now equipped with the right tools for effective maintenance planning which leads to advanced cost evaluation powered by analytics. Now, they’ll be able to provide and find measurable cost saving actions.
Data visualization designed for specific usage
The collaboration between SICK and the beverage company was crucial to the success of this project. The team of the beverage company was able to provide process knowledge and offered constructive feedback throughout the project.
By having the customer actively involved in the development of the solution, we could find the most optimal solution for their needs.
Compressed air savings results
According to an initial analysis, the project delivered annual savings of close to €60,000 on 1 million m³ of compressed air. A second automatic analysis yielded an additional savings potential of 0.5 million m³ – and that’s only for downtimes. But there’s even more savings potential if dynamic leaks are considered.
Going forward, the SICK continuous monitoring system will be used to monitor their systems around the clock and deliver hard data. Ultimately leading in helping to cut downtimes and service costs and will improve the carbon footprint with more efficient production.