How Optimation in Sweden used 3D vision in grimy environments
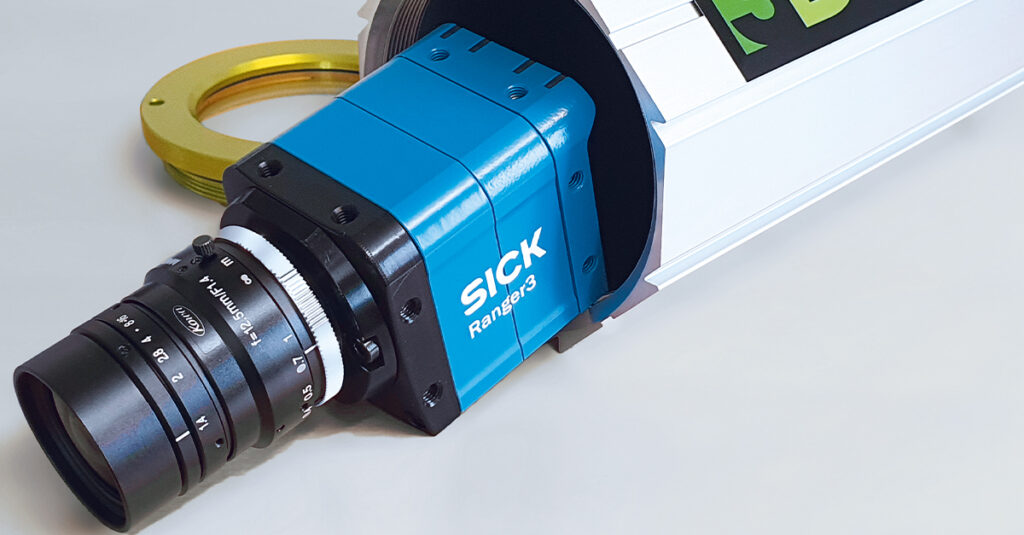
The dusty, grimy environments of mining and metallurgy can be a challenge for sensors and vision cameras. Products such as the Ranger3 have been highly successful in helping to increase productivity–even in such unpredictable industrial settings. Two Swedish industrial companies have put that experience to the test with upgraded 3D machine vision technology.
When ore is loaded onto a conveyor belt to go to a crusher, its form and size can vary widely, from large rocks down to very fine material. Having accurate information about the particle size distribution on that conveyor belt is important for process optimization. This is where the Swedish sister companies Optimation AB and Optimation Advanced Measurements AB come into play.
Optimation is Sweden’s leading expert in production optimization in the process industry. The company is a cutting-edge engineering consultancy that provides advanced services and solutions in automatic control for a broad range of industries. When it comes to crushing, grinding, milling, and pulverizing, they are masters of production optimization.
3D scanning technology, based in Sweden
One of the company’s main products is their three-dimensional particle measurement system (3DPM). This high-performance measurement system carries out 3D scanning of bulk material. The associated state-of-the-art software, developed by the company, analyzes the individual particles passing on a conveyor belt. Developed after years of research and in cooperation with Luleå University in Sweden and Innovative Machine Vision in Australia, 3DPM has now been on the market since 2008.
The system has proved itself to be highly reliable, even in very difficult, real-life conditions. That efficacy and reliability are the reasons why it can now be found in production sites all over the world, from customers sites in Sweden to the largest steel manufacturer in Japan to the mining industry in Australia, alongside other challenging environments.
Designed for rough industrial environments, the 3DPM uses the SICK Ranger3 3D vision camera to measure particle size distribution on wide, high-speed conveyor belts. Not only does the system have an IP65 classification, but it also has very low maintenance requirements, even when running 24/7.
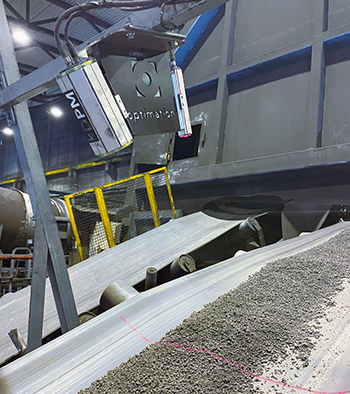
Precision that withstands harsh conditions
Detecting and classifying dark particles on black conveyor belts demands that the camera meets high sensitivity standards. It is also important that the system can identify very small particles, known in this context simply as “fines.” These fines make the grinding mill less efficient, increasing the energy and thereby the costs for every ton that is processed. To be able to identify them reliably requires a high sampling rate. SICK’s Ranger3 is a very robust 3D vision camera with a unique CMOS sensor that fulfills both demands. In fact, “so far, no camera has stopped working for us despite the fact that most of our measuring systems are located in harsh environments,” explained Optimation Machine Vision Specialist Jan Nyström.
The Optimation 3DPM system also reveals other parameters such as particle shape and bulk volume flow. Boulders or rock bolts are detected, even when these partially overlap. That level of precision is very valuable in protecting the production system and preventing interruptions. It also means that the system can be easily adapted to measuring a large variety of materials such as coke, limestone, metal ore and agglomerated materials.
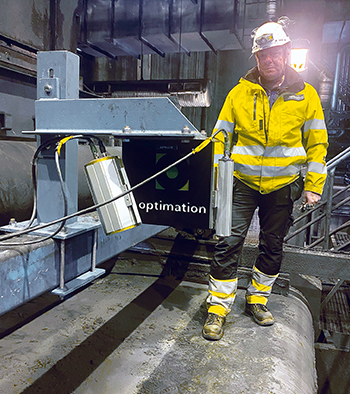
Reliability in partnership and industrial technology
“The Ranger and Ruler from SICK have always been dominating in terms of technology, and at the same time the SICK team is incredible when it comes to long-term support and product maintenance,” Nyström says. SICK sensors and 3D machine vision solutions are also part of the reason why Optimation can promise their customers warranties and support that extends over a long period of time.
Each industrial environment poses its own unique challenges. SICK engineers work closely with customers to find the optimal solution for as many of these challenges as possible. For Optimation, this solution was found in robust, high precision sensors and fruitful collaboration.