From 2D to 3D and beyond!
Efficiency is key in industrial automation—no shocker there. But what types of applications have evolved from this need for efficiency? From automotive manufacturing to logistics, the ability to swiftly and accurately pick parts from bins has long been a coveted goal. This process, known as bin picking, has transformed significantly over time, driven by advancements in technology and the quest for enhanced precision and speed.
What is bin picking?
Bin picking entails the retrieval of parts from a container or bin, a task historically deemed the “holy grail” of robotic automation. The objective is to identify and extract components based on visual cues, optimizing the process for subsequent manufacturing stages. Whether it's automotive components or assorted products on a warehouse pallet, each item's unique geometry and position within the bin pose challenges that different solutions aim to overcome.
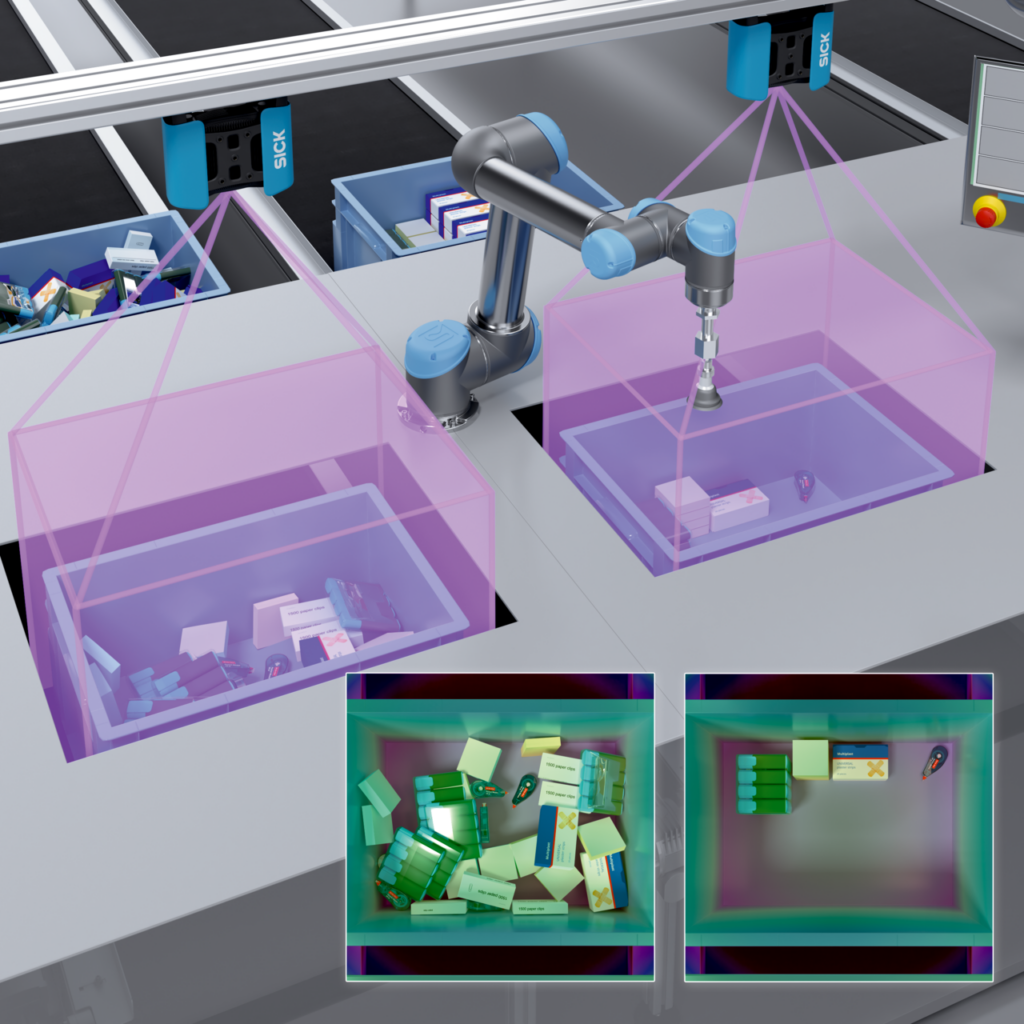
Are there different types of bin picking?
The quick answer: Yes! There are different approaches to bin picking. They are primarily characterized as random bin picking or structured bin picking.
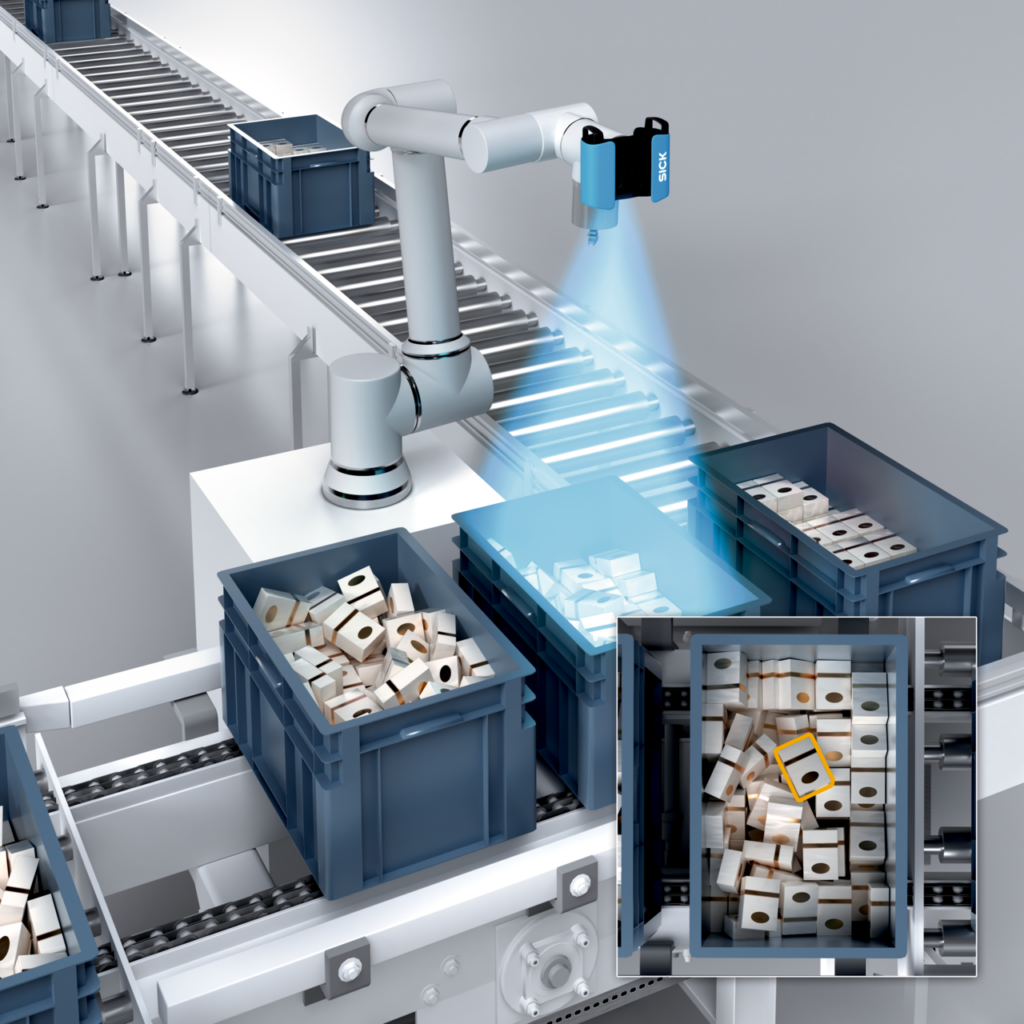
Random vs. structured bin picking
In structured bin picking, the parts are neatly organized within the bin. They’re placed in predictable patterns or layers. This means the robot can easily pick these parts because they’re aligned the same way, oriented identically, and have a uniform appearance.
Imagine a tray of cookies, like Oreos® or CHIPS AHOY®. If a robot had to pick the cookies out of the tray and place them on a conveyor belt, it would follow the same process for picking each cookie. This is because each cookie has the same orientation; they are all upright in the same position within their part of the tray. The robot just has to know to move a longer distance with each pick to grab each cookie. This would be a structured bin picking scenario.
Now: imagine the cookies are no longer in their plastic tray. They were dumped into a bin, and are now in a haphazard pile. The robot can no longer depend on knowing the exact position of the cookies in the tray. It has to understand and see the different orientation of each cookie; one cookie could be upright while the next is lying face down. This is now a random bin picking application.
In random bin picking, the parts have no specific arrangement. They can overlap, face different directions, and be all mixed up. This type of picking is more challenging, because the camera and software have to repeatedly determine how to grab each part in its own unique orientation, in addition to avoiding running into other parts or the edges of the bin.
Different bin picking scenarios: Do they need different solutions?
In a structured environment, where parts adhere to a specific arrangement, traditional 2D imaging techniques suffice. However, random bin picking demands a more sophisticated approach, necessitating the integration of advanced 3D technology. Unlike structured bins, random configurations require systems capable of identifying and adapting to variable part positions and orientations.
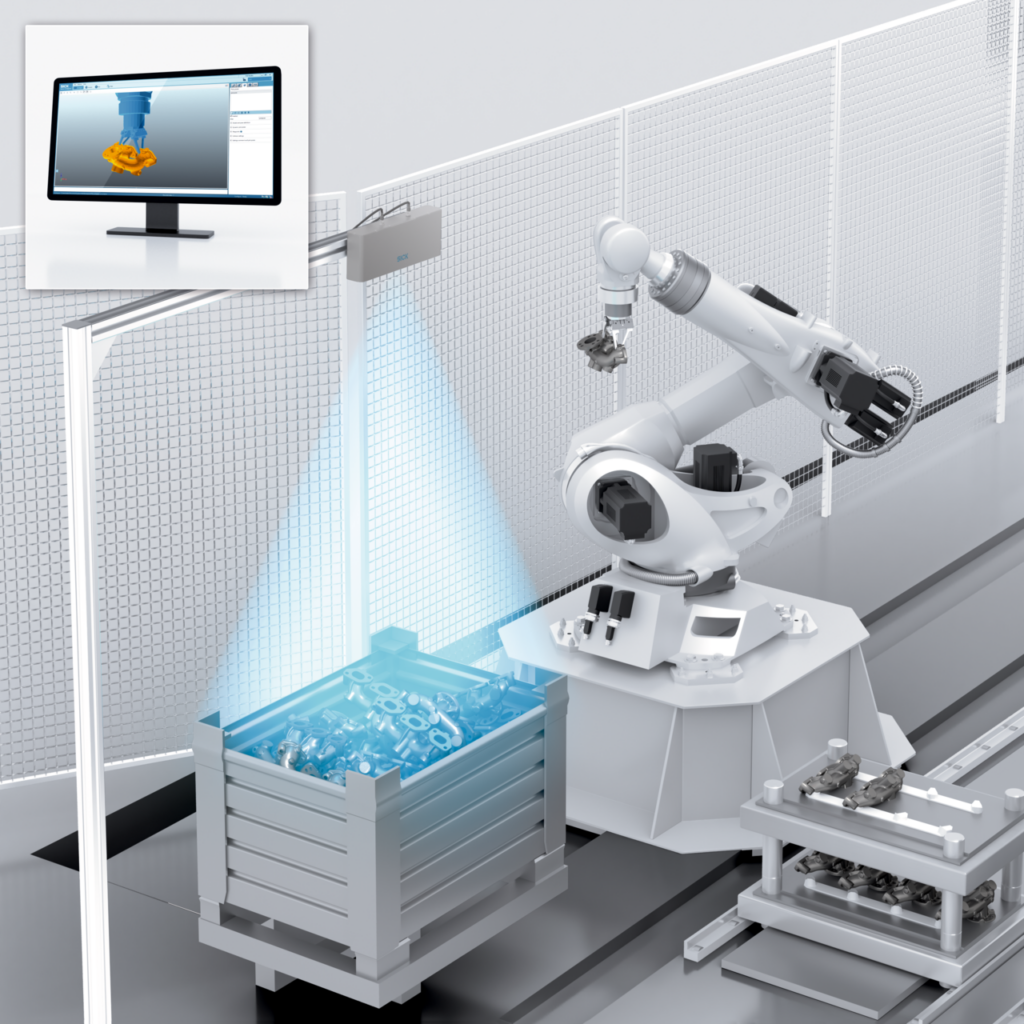
The evolution of bin picking technology: 2D vs. 3D
Initially, bin picking relied heavily on 2D imaging, offering limited depth perception and orientation capabilities. However, the advent of 3D technology revolutionized the field. By capturing spatial data in three dimensions, modern systems can discern not only the X and Y coordinates but also the Z axis, enabling precise depth perception. This enhanced perspective facilitates accurate part identification and retrieval, even amidst varying orientations within the bin. Overall, 3D technology offers a more precise pick point. This is extra helpful when parts are not in predictable positions.
PLB robot guidance for 3D bin picking
Designed to streamline the integration of 3D data with robotic systems, SICK’s PLB software offers unparalleled versatility and efficiency. By leveraging sophisticated algorithms, PLB analyzes 3D point cloud data to identify optimal pick points for robotic manipulation. Whether it's matching parts based on CAD models or adapting to dynamic environments, PLB’s precision is where it shines, thanks to its range of localization algorithms working in conjunction with 3D cameras. Hello, more precise pick point!
PLB software is also agnostic to the type of robot, making it a nearly universal tool, along with the range of communication options SICK offers. And if we don’t have your desired communication option, we can also add another protocol to the software to fit your needs.
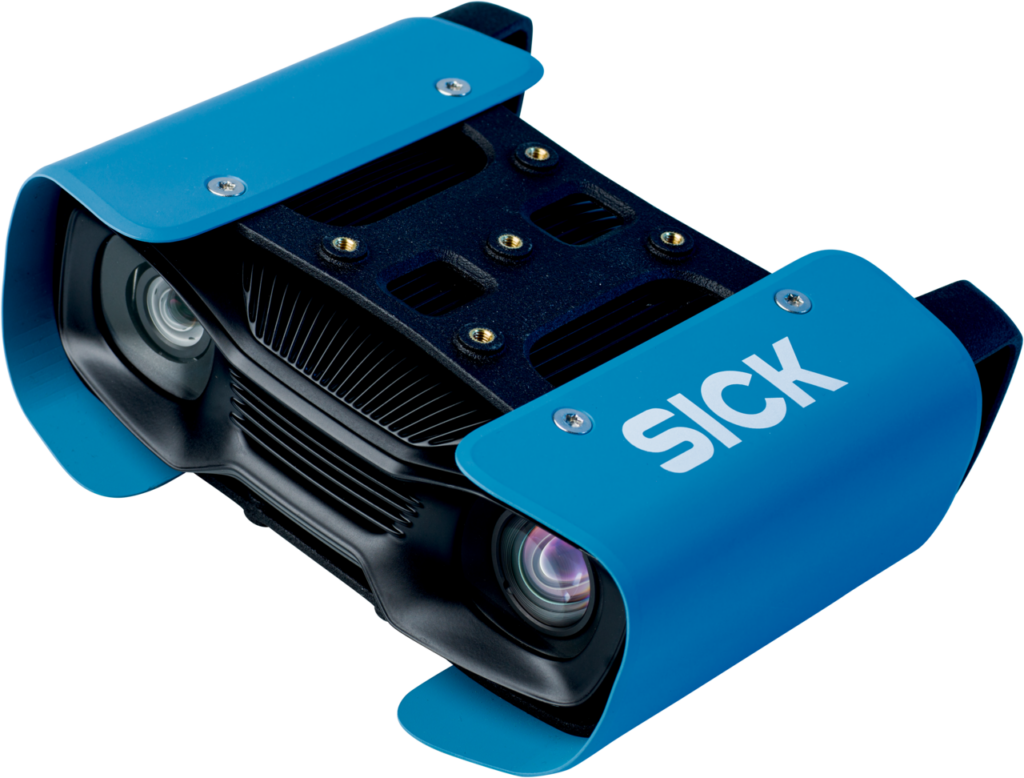
Applications across industries: logistics and beyond
The applications of bin picking extend beyond manufacturing, particularly in the logistics sector. From palletization to order fulfillment, 3D bin picking technology enhances efficiency and accuracy in diverse settings. Whether it's identifying packages on a conveyor belt or optimizing truck unloading processes, the combination of 3D imaging and robotic manipulation can help speed up processes (while maintaining accuracy) along many points of the logistics journey.
The future of bin picking: versatility and precision
As technology continues to evolve, the future of bin picking holds immense promise. With advancements in AI, machine learning, and sensor technology, we can anticipate even greater levels of versatility and precision.
Bin picking technology represents a significant milestone in the journey towards fully automated manufacturing and logistics. And with the power of 3D robot guidance systems, like our PLB software, businesses can unlock new levels of efficiency and productivity.