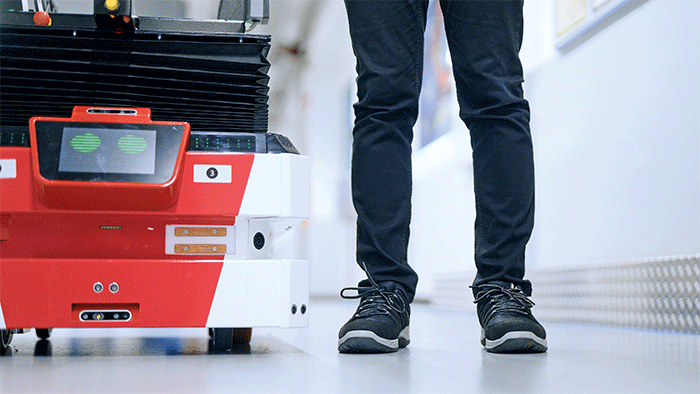
Wilkinson Sword used mobile robots equipped with SICK sensors to optimize operations
Razor blade manufacturer, Wilkinson Sword, had big goals when it came to automating its material flows to decrease employee workload and increase efficiency, flexibility, and safety. Luckily, mobile robots with state-of-the-art technology the GESSbots can guide sharp blades through all stages of the finishing process and help Wilkinson Sword achieve its automation goals.
Enhancing Production with Mobile Robots
Wilkinson Sword GmbH has been producing its famous razor blades in the German ‘city of blades’, Solingen, for over sixty years. In keeping with the high standards of its long-established brand, the company produces innovative and durable shaving products using top-quality blade steel that can handle punching, hardening, grinding, and polishing processes.
Wilkinson continuously strives to drive forward digital transformation in its facility by automating repetitive manual work processes. In this production facility, the blades undergo finishing, whereby they are cleaned after the grinding process and supplied with a hard layer of chromium.
To make the process more efficient, they have added three GESSbots (autonomously navigating mobile platforms, also known as AMRs). These robots have now assumed the task of transporting razor blades between the different manufacturing processes.
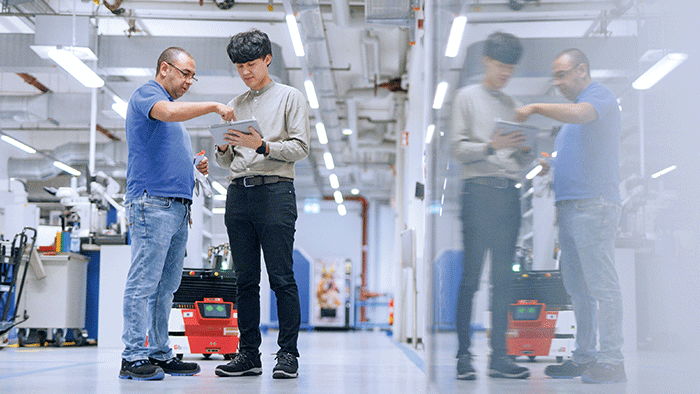
Manufacturing Project Engineer Quin Fat Diu explained the background of this project. “Before this step in automation, our employees used to push the transport carts and load the blades into the system by hand. Our goal was to improve the ergonomics for our operators and enable them to take on more value-adding activities such as quality control tasks,” Quin said.
According to Quin, there is great acceptance among the workforce of the GESSbots in work processes. “The appealing visual and communicative design of the robots also plays a big part here. Our employees understand the great benefits to be garnered from these innovative robots and they have no reservations about their utilization,” Quin said.
Gessmann and SICK – A successful automation partnership
To implement this undertaking in automation, Wilkinson commissioned Gessmann, an experienced specialist in providing tailor-made platform solutions. Gessmann then partnered with SICK to provide expertise on all safety aspects. The two companies have a long-standing working relationship and have been collaborating to solve the ever-changing challenges surrounding sensor concepts for years. The consistent expansion of SICK’s portfolio is reflected in the corresponding growth in the proportion of sensors in Gessmann products.
Steffen Kuhnle, Project Manager for GESSbots at Gessmann, has been a part of this collaboration from the very beginning and knows what is important in a good partnership.
“SICK and Gessmann share great confidence in their partner’s respective high level of technological expertise and market knowledge. It is not only the products from SICK, but also its unique system approach with hardware and software alongside competent advice and service that enable us to meet the individual requirements of our customers,” Kuhnle said. “Equal partnership and SICK's sensor solutions enable flawless automation.”
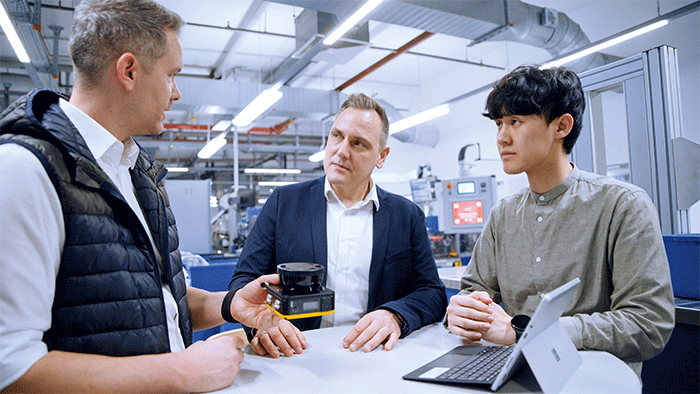
A complete package with state-of-the-art sensor technology
The automation solution at Wilkinson includes five passive transfer stations with a specially adapted holder for the customer's standardized material carriers.
“The SICK safety sensors provide the GESSbot with the data to be able to navigate safely throughout our facility. With the support of SICK, Gessmann has packed the GESSbot with state-of-the-art sensors and control technology to ensure all processes function safely and smoothly,” said Marcus Ichters, Key Account Manager Mobile Platforms at SICK. “With the support of SICK, Gessmann has packed the GESSbot with state-of-the-art sensors and control technology so that all processes function safely and smoothly”
These AMR carriers are recognized and differentiated with the aid of inductive sensors from the IME12 series. If the resource changes accordingly (new workpiece carrier), new orders are automatically created via an Ethernet interface and a GESSbot Gb350 is sent to this station via a new transport order.
The robot identifies its location using the nanoScan3 EFI-pro safety laser scanner and docks precisely to one of the passive stations. Safe motion solutions from SICK ensure the protection of employees and the efficiency of mobile and stationary applications.
The safe position is monitored at the respective station using a transponder switch from the TR4 series. A DFS60S safety encoder checks the standstill. Then, the protective fields of the safety laser scanner are automatically switched so that no one can enter the danger zone of the lifting mechanism.
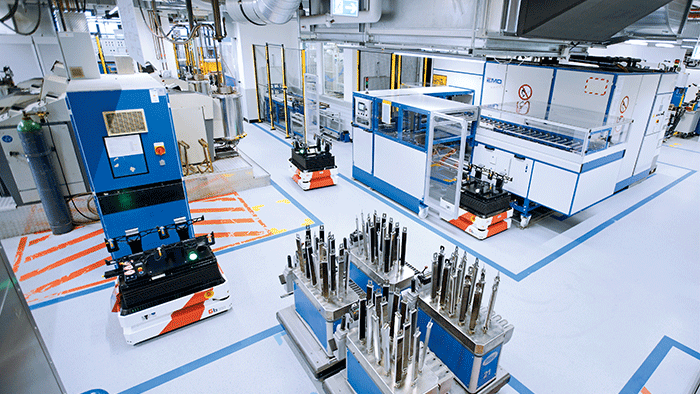
The GESSbot has the appropriate structural design to pick up the workpiece carrier and transport it to the destination. Ichters also highlights the planned implementation of a safe 3D vision camera: “The safeVisionary2 continuously records the surroundings and monitors whether there is enough avoidance room if an obstacle appears. The GESSbot can then actively avoid the obstacle and return to its actual route.”
The GESSbot is also equipped with an additional Flexi-Soft safety controller, which communicates securely with the basic vehicle via the Flexi-Line bus. The safe end position for further travel is queried via an inductive safety sensor from the IME2S series. The project also includes a retrofit for elevator control so that the workpiece carriers can be automatically transported to another floor.
A winning automation combination
Kuhnle is very pleased with the successful implementation of the project.
“Gessmann faced new challenges when it came to incorporating the GESSbots and the corresponding technology into the existing material flow infrastructure. We discussed the individual points together and SICK provided advice with well thought-out solutions and products,” Kuhnle said. “This has enabled us to implement and achieve the goals that Gessmann was looking for. Collaboration is always on an equal footing and communication is excellent.”
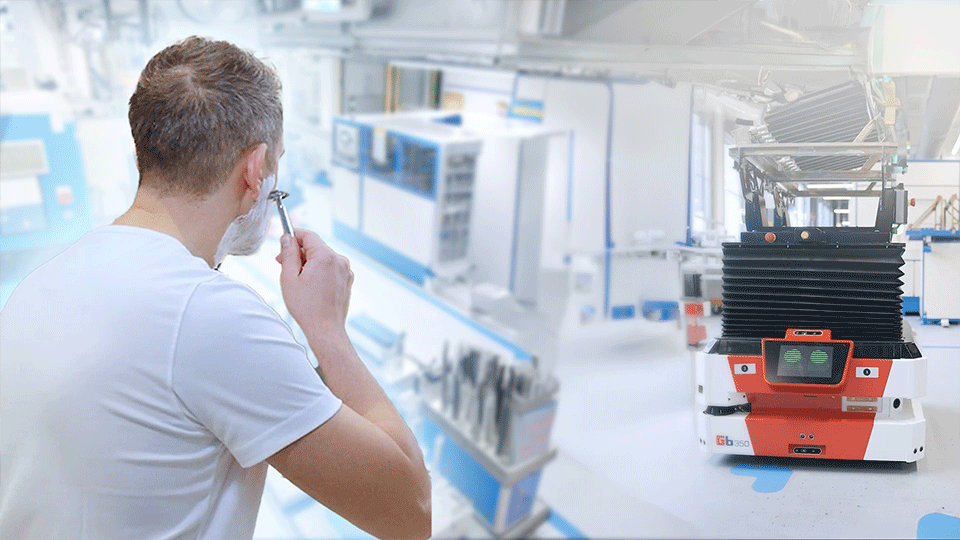
The success and potential of this partnership has also made an impression with Wilkinson.. Qiun Fat Diu has had a very positive experience with the pilot application and three vehicles.
“The system is safely up and running and has significantly relieved the workload of our employees. We have seen a large increase in efficiency and an optimization of resources in this area of material flow,” Quin said. “For this reason, we are working to expand the use of GESSbots and thus automate the entire material transport process. Extending their use to other areas of production is a step we consider to be entirely possible and one that makes perfect sense.”