The collaboration between Mitsubishi Electric and SICK brings innovative solutions in machine vision and safety
Mitsubishi Electric and SICK have been collaborating closely for several years and have just extended this successful cooperation. SICK is now an official partner in Mitsubishi Electric’s e-F@ctory Alliance. The alliance is a 300-member strong global network comprising of manufacturers of industrial components, systems integrators, and software suppliers. The e-F@ctory-Alliance partners collaborate on optimized machine vision solutions that are tailored to customer requirements. SICK and Mitsubishi Electric have been cooperating on the development of innovative solutions in the areas of machine vision and safety technology.
In this interview, we speak to Andreas Fritzsche, Technical Industry Manager at SICK AG, and Andreas Pfaff, Division Manager Factory Automation European Development Center at Mitsubishi Electric about this successful collaboration.
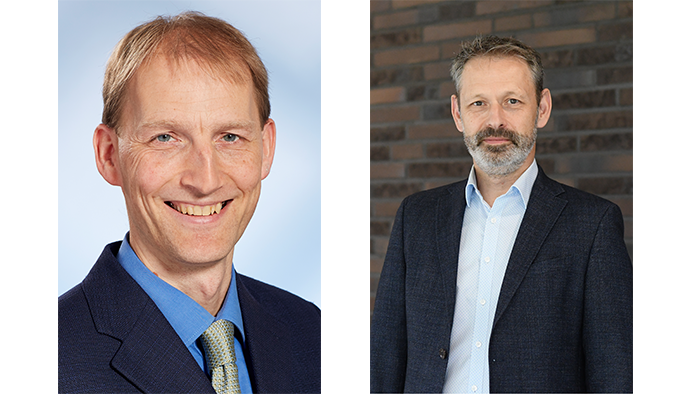
Andreas Fritzsche (left), Technical Industry Manager at SICK AG, and Andreas Pfaff, Division Manager Factory Automation European Development Center at Mitsubishi Electric
How did this machine vision collaboration between Mitsubishi Electric and SICK come about?
Andreas Pfaff: The origins of our collaboration in safety began because of the different principles that Asian and western countries, particularly with protecting machines and systems. A variety of different approaches have been used for this, and it is important for us to be able to optimally accommodate these. The partnership with SICK has enabled Mitsubishi Electric to expand its own product portfolio in this area. It has given us the ability, for example, to offer our customers comprehensive solutions for a wide range of automation applications.
Andreas Fritzsche: This collaboration between SICK and Mitsubishi Electric has existed for a long time. We have also carried out many joint campaigns in safety technology, such as various exhibits at international trade fairs. To further pursue this longstanding and successful collaboration in the safety field, we are now also tackling the machine vision segment.
What advantages does this machine vision partnership bring for its members?
Pfaff: Generally speaking, it gives the members of the e-F@ctory Alliance the opportunity to access a multitude of solutions and consult with the other partners. This enables them to help customers, even in areas where they have insufficient offerings of their own. When it comes to fail-safe automation in particular, our partner companies can rely on the competent and strong partnership of Mitsubishi Electric, with its diverse range of solutions, in conjunction with SICK and its functional safety technology and sensors.
What advantages does this partnership bring for customers?
Pfaff: The key advantage for our customers is that it gives them direct and uncomplicated access to a comprehensive range of solutions for automation projects. Even for more complex tasks, the search for suitable products and solutions within the e-F@ctory Alliance will quickly deliver outstanding results.
Fritzsche: Furthermore, machine automation solutions that incorporate sensors and controllers are easier to implement. The e-F@ctory Alliance partners offer the safe, problem-free interoperability of automation systems and, therefore, offer efficient solutions.
Pfaff: They also provide comprehensive support, from the conception phase right through to commissioning and, of course, if any issues arise after that.
What joint solutions in safety technology do you offer?
Pfaff: Our latest joint solution is the extension of our compact MELSEC iQ-F PLC series with the control technology from SICK. Thanks to the FX5-SF-MU4T5 main module developed and manufactured by SICK, our FX5 compact PLC can be extended with a safety controller. The SICK module is simply connected to the FX5 system bus on the right-hand side, just like other iQ-F expansion modules. The FX5 controller can then read information from the safety module over the bus and evaluate it for an overall control solution, with no negative impact on the status of the fail-safe function.
What added value do customers gain from this tailored safety solution?
Pfaff: Our MELSEC iQ-F series is one of the leading PLCs in small and medium-sized machines and systems, due to its wide range of features. The PLC family comes with diverse network connections, high-performance analog signal processing, and servo/motion control functionality already built in. Thanks to the safety solution with the FX5-SF-MU4T5 and its expansion module, it is also possible to equip the PLC with functional safety. While the safety module autonomously ensures functional safety, the interaction with the MELSEC iQ-F PLC over its system bus makes it possible to implement a reliable overall control concept.
Fritzsche: Specialists are hard to come by, particularly safety engineers. The advantage of this tailored safety solution is that it is very user friendly. For example, it enables downstream or upstream parts of the machine to be checked without error-prone external wiring. This saves not only time, but also cost.
Pfaff: Furthermore, the status of the safety application can be visualized in the HMI connected to the iQ-F, or via information systems connected by means of the network interfaces of the iQ-F.
What application for integrating machine vision have you developed?
Fritzsche: The solution combines the Inspector PIM60 2D vision camera from SICK with a PLC controller from Mitsubishi Electric and is suitable for a broad range of applications: from the automotive industry to food production to machine building. The solution allows for a simple visual inspection of a packaging line. It can be used to check whether a cap has been inserted correctly, or a lid is in the correct position. A shape inspection in mechanical part production is one of the many other examples of common inspection tasks these days.
Pfaff: The solution we developed also gives the users of our control technology access to SICK's diverse portfolio in machine vision. The ability to easily integrate sensors and control technology depends not only on the communication technology, but also on the availability of helpful PLC programming tools. A core element of the developed solution is therefore function blocks for our GX Works engineering software that make integrating the machine vision into the control concept an uncomplicated process.
What advantages does this joint vision solution bring to customers?
Fritzsche: The complex data interface is supported by a function library that makes the engineering task of integration much simpler. A video tutorial that clearly explains to users how to implement this correctly is also available.
Pfaff: Using our joint vision solution, our customers can optimize their processes, minimize production costs, and ensure, or even increase, the level of quality. In doing so, they can put trust in our tried-and-proven technologies and comprehensive support, as for all e-F@ctory solutions.
Can you complete this sentence for us: The e-F@ctory Alliance of the future …
Fritzsche: … proves to the user that integration can be achieved efficiently and easily with the help of competent partners.
Pfaff: … is always one outstanding solution ahead of the customer’s requirements.
Have questions about this partnership?