What you need to know to select the right safety laser scanner for your application
Safety laser scanners are essential tools in modern industrial environments, providing a versatile and reliable means of ensuring worker safety and protecting machinery. A safety laser scanner is a device designed to protect people from injury by detecting their presence and stopping machinery or hazards in the area. They are particularly useful in applications where traditional safety measures, such as physical barriers or light curtains, may not be practical or effective.
Safety laser scanners are ideal for dynamic environments where the layout or operational conditions frequently change, such as in automated guided vehicles (AGVs), robotic systems, and complex manufacturing processes. By offering flexible and customizable detection zones, these scanners can adapt to various scenarios, ensuring comprehensive coverage and immediate response to potential hazards. Their ability to integrate seamlessly with existing control systems further enhances their utility, making them a crucial component in maintaining a safe and efficient workplace.
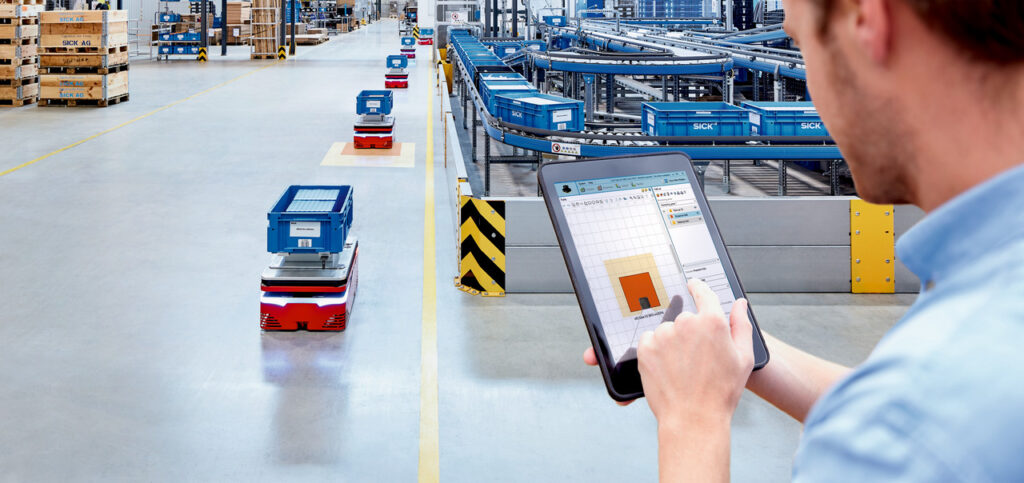
Here’s how they work
The scanner emits laser beams that sweep across a designated area. When the laser beams hit an object or person, they reflect back to the scanner. The scanner processes these reflections to determine if an object or person is within the protected zone. If an intrusion is detected, the scanner sends a signal to stop the machinery or hazard, preventing potential injury.
Safety laser scanners enable humans and machines to collaborate safely in industry. There, laser scanners protect hazardous areas, hazardous points, and access points – indoors and outdoors. Thanks to the safeHDDM® technology, the devices are resistant to ambient light, dirt, dust, rain, fog, and snow. The microScan3, nanoScan3 and outdoorScan3 product families are setting new standards for safety laser scanners, opening new fields of application for you, and increasing productivity.
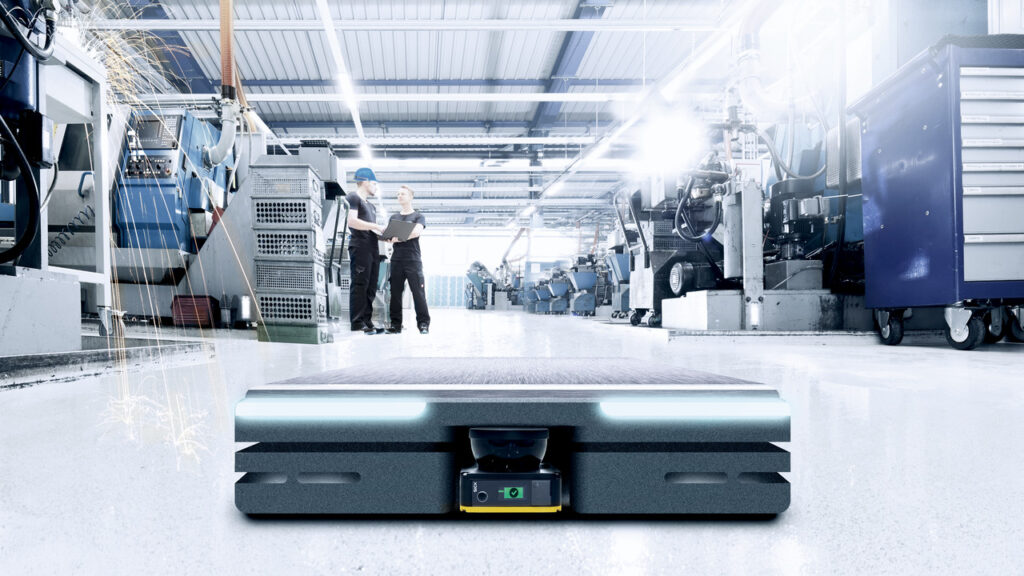
Stationary Applications for Safety Laser Scanners
Safety laser scanners are a versatile safety product for any manufacturing and production facility. Using the time-of-flight principle, the scanner calculates position based on the amount of time it takes for the laser to bounce off an object and return to the scanner. This produces a protection zone that can be customized to fit any need.
Many safety laser scanners are mounted in horizontal applications to prevent hazards and provide general area protection. However, vertical applications of a safety laser scanner can be beneficial if the area needing protection is not a standard rectangle or if you need multiple zone monitoring.
A vertically mounted safety laser scanner operates differently from a horizontally mounted one primarily in terms of the area it monitors and the type of protection it provides.
With area coverage applications, a horizontally mounted laser scanner will scan a horizontal plane, typically used for area protection, access protection, and perimeter monitoring. It ensures that no one enters a hazardous zone from the sides. With a vertically mounted laser scanner, it will scan a vertical plane, which is useful for applications like safeguarding entry/exit points, monitoring doors, or protecting areas with irregular shapes.
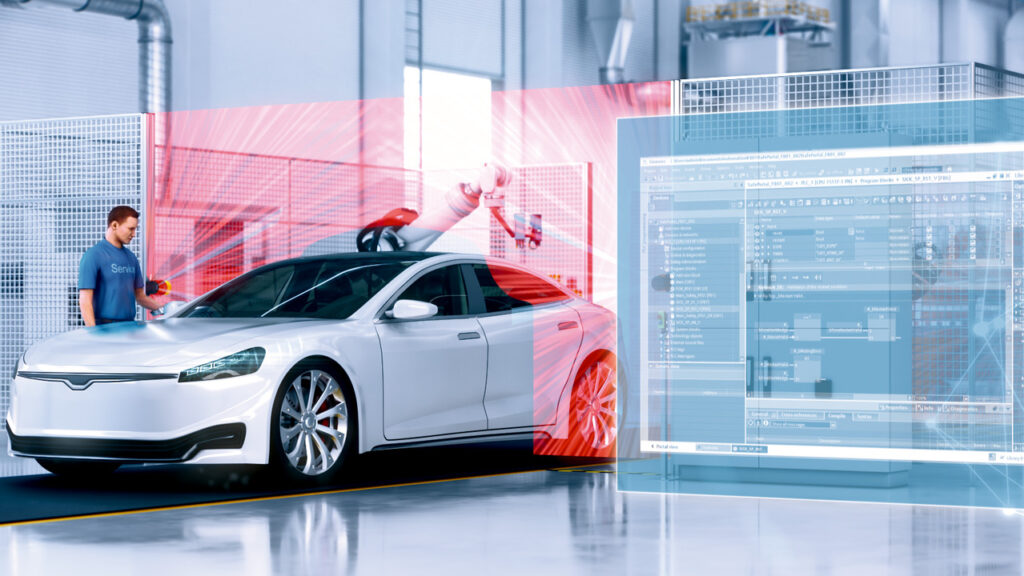
Uninterrupted Work with Safe Portal Solutions
Although you most often see safety light curtains used in access protection applications, safety lasers scanners can also be used in some specific situations. In areas where it may be difficult to mount two perpendicular safety light curtains, a single safety laser scanner can be mounted vertically to detect any entrances into a hazardous area.
A vertically mounted safety laser scanner can be used in entry/exit applications to create a protective field. It requires no alignment of sender and receiver as it is all in one device. And with the compact size of SICK’s safety laser scanners, like the microScan3, it can be easily integrated into the machine design.
The protective field can be contoured to allow for the passage of material, such as a car to avoid interrupted work. Predefined contours can be safely and reliably recognized with contour detection fields.
Also, due to the high number of fields, different field shapes can be configured depending on the material form. This means it can allow the passage of certain materials, while still safeguarding the area immediately around the material so a person can’t pass through undetected. This is ideal for moving materials in or out of hazard zones.
Scanners are also installed horizontally to monitor hazardous zones, ensuring no one is present before machinery starts or continues operation. They also provide access protection, often used to secure entry points, preventing unauthorized access to dangerous areas.
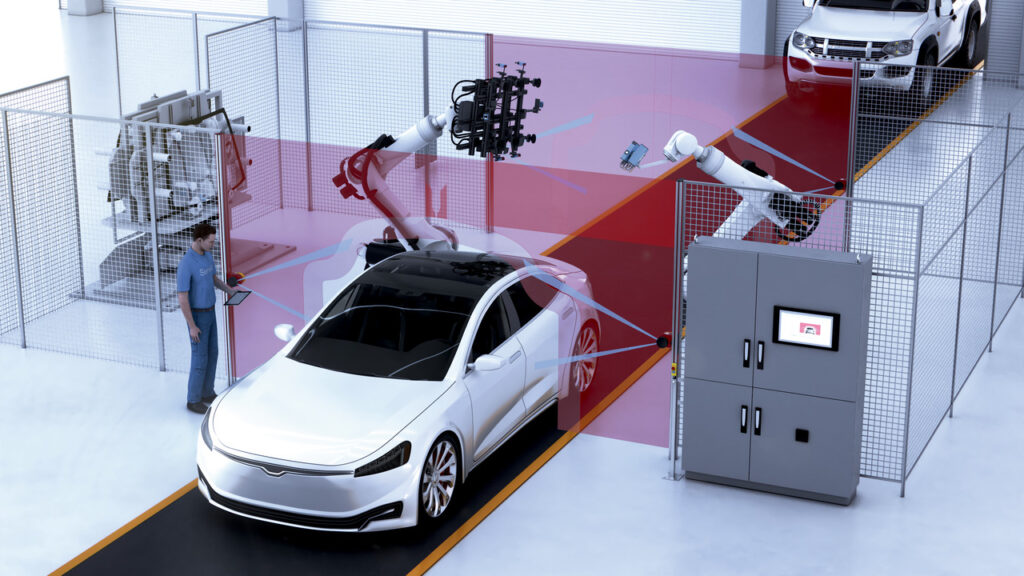
Scanning Multiple Fields for Maximum Protection
Some safety laser scanners can be used in multiple safety functions due to its capability to simultaneously evaluate multiple fields. It can safeguard a hazard point on a single side of a machine, especially when there is close interaction with the machine. The approach of the person is detected by sensing the person’s presence in an area. This is necessary for machines that cannot be viewed completely from the position of the reset device.
If a person reaches into a hazardous area, a vertically mounted safety laser scanner will recognize this by detecting the person’s arm and stopping the process. It would remain stopped if there are people or parts of the body detected in the hazard zones. This enables unrestricted access, frequent interaction, and an unimpeded view into the machine.
It can also monitor multiple fields at once to provide protection in more complex applications. The microScan3 Pro can provide safety information for up to eight protective fields at one time and simultaneously safeguard multiple cells with just one device.
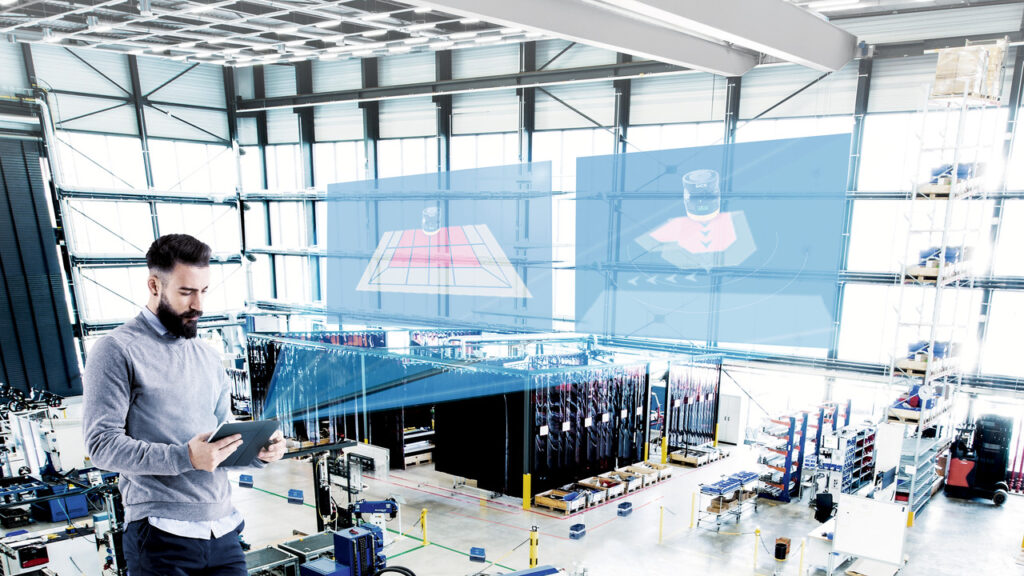
For example, if you were looking to protect multiple cells, you could mount a scanner in the center of the row and have a different protective field for each cell. When someone infringes one of the cells, that single cell would stop, but the others would continue to run.
Whether used in a horizontal or vertical application, safety laser scanners are a versatile product that provide you added flexibility and maximum safety to your production lines.
Human-robot collaboration (HRC) describes a scenario in which humans and automated machines share the same space and work within it simultaneously. Driven by Industry 4.0, this model promises the interaction of highly-flexible work processes, maximum plant availability and productivity, and economic efficiency. But HRC will only be able to live up to this promise when appropriate application-specific safety technology is assured.
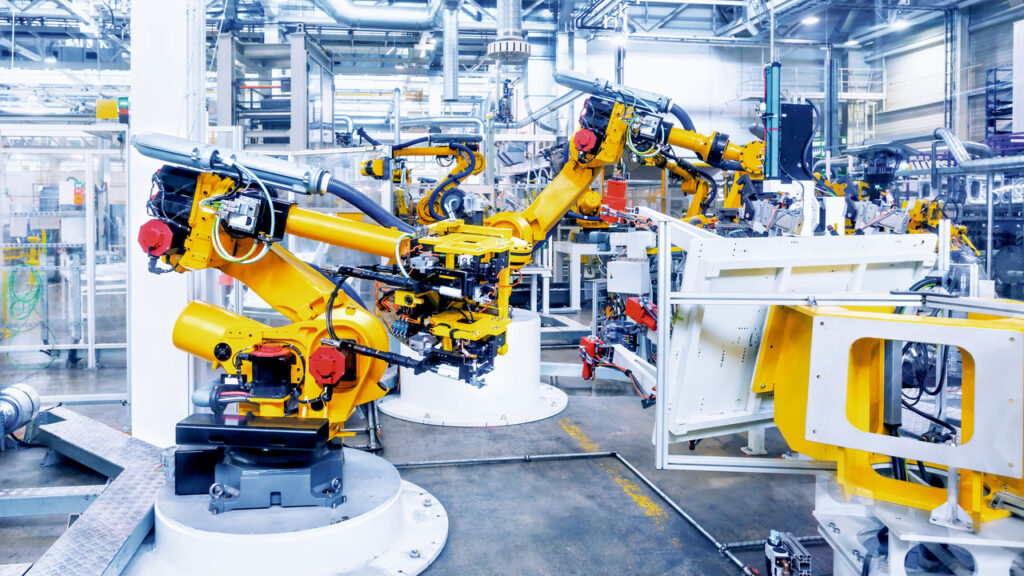
Safety Solutions for Human-Robot Collaborations
Industrial automation focused on interaction between humans and machines long before the initiation of Industry 4.0. Until now, two interaction scenarios – coexistence and cooperation – have dominated, representing about 90 percent of such situations. Space and time are the important interaction parameters here. Coexistence describes a work situation in which the human and the machine are in neighboring areas at the same time during the interaction. Cooperation, on the other hand, is an interaction during which the human and the machine share the same work area, but work within it at different times.
A third form of interaction is increasingly being focused on within the framework of Industry 4.0: collaboration. In this scenario, humans and robots share the same workspace at the same time. In such collaborative scenarios, the standard industrial robot with safe kinematics is no longer sufficiently safe, so collaborative robots must be used. In this case, the forces, speeds, and travel paths of the robot must be monitored – and limited, depending on the actual degree of risk. If necessary, the robot is stopped or switched off. The distance between the human and the robot thus becomes a decisive safety-relevant parameter.
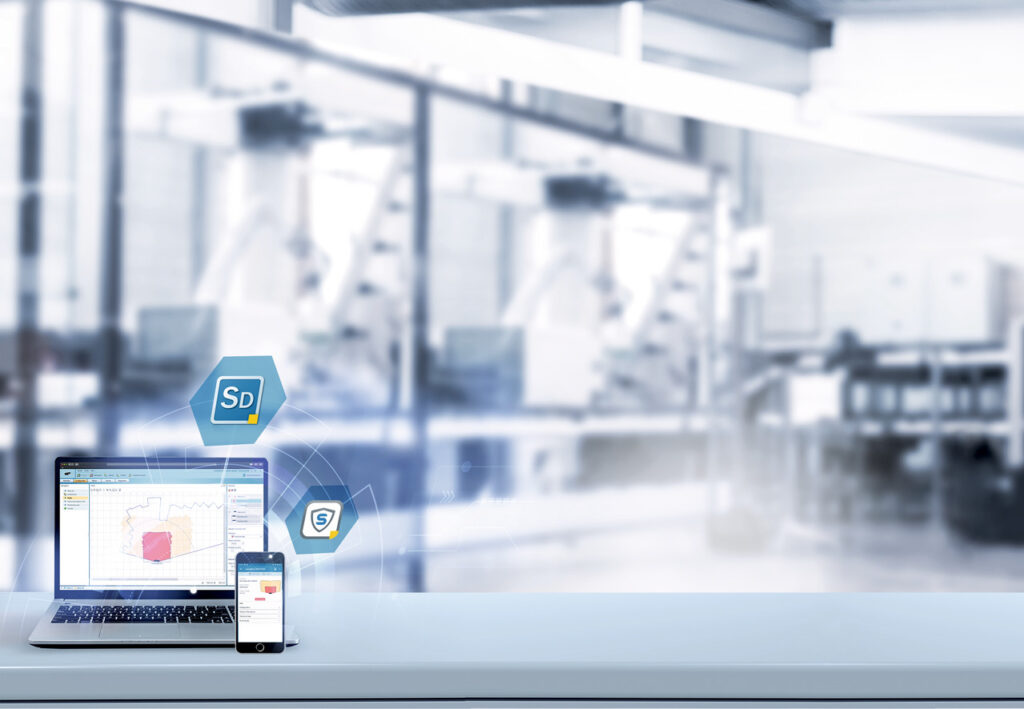
Four types of collaborative operations
According to the technical specification ISO/TS 15066, there are four different types of collaborative operations:
- Safety-rated monitored stop – halts the robot for interaction with the human
- Hand guiding – ensures safe HRC because the robot is deliberately guided manually at an appropriately reduced speed.
- Power and force limiting – necessary safety is achieved by reducing the power, force, and speed of the robot by using limiting functions for safety-relevant control systems, or an inherently safe design of the robot with a biomechanical load limit at which no hazard or injuries are to be expected. This takes place regardless of whether there is any intentional or unintentional physical contact between the robot and a human.
- Speed and separation monitoring – based on monitoring of the speed and travel paths of the robot and adapted to the work speed of the operator in the protected collaboration space
The fourth collaboration is very much in the spirit of highly flexible work scenarios. Safety distances are permanently monitored and, when necessary, the robot is slowed down or stopped, or its travel path is changed. The robot system can automatically resume its movements, with the usual speeds and travel paths, when the distance between the operator and the machine increases again to greater than the permitted minimum distance. This restores the robot’s productivity without delay.
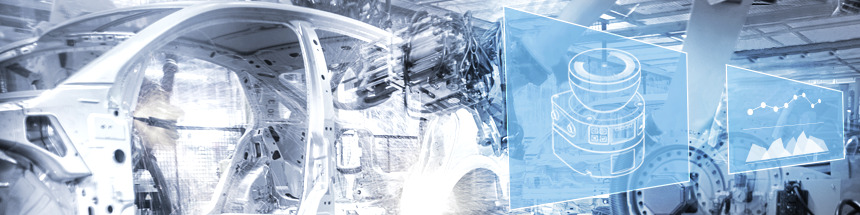
Steps to Selecting a Safety Laser Scanner
Selecting the right safety laser scanner for your application is crucial for ensuring optimal safety and efficiency in industrial environments. These devices offer a versatile and reliable means of protecting workers and machinery by detecting the presence of individuals and stopping hazardous operations. They are particularly beneficial in dynamic environments where traditional safety measures may not be practical.
Safety laser scanners provide flexible and customizable detection zones, adapting to various scenarios to ensure comprehensive coverage and immediate response to potential hazards. Their seamless integration with existing control systems further enhances their utility, making them indispensable in maintaining a safe and efficient workplace.
Whether used in horizontal or vertical applications, safety laser scanners offer unparalleled flexibility and maximum protection. By understanding the key features and capabilities of these devices, you can make an informed decision to select the best safety laser scanner for your specific needs, ensuring a safer and more productive industrial environment.