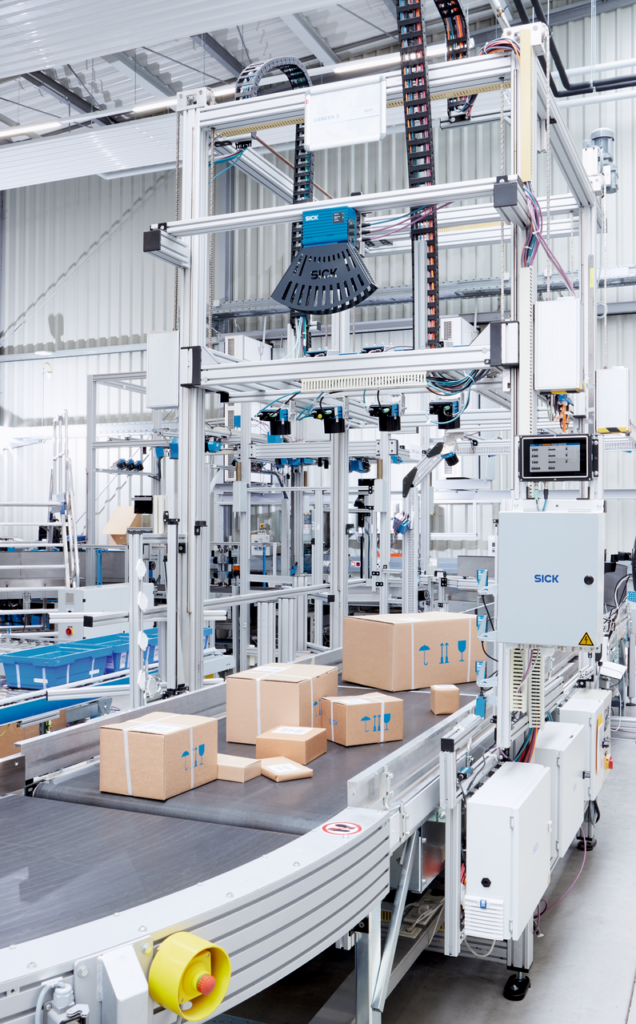
The Shape of Success and the Crucial Role of Contour Verification in Optimizing Warehouse Operations
Contour verification in logistics refers to the process of accurately identifying and verifying the shapes or contours of products within the supply chain, especially in warehouse and distribution center operations. This technology involves using advanced imaging systems, sensors, and algorithms to analyze the physical characteristics of items, ensuring that they match specified criteria for shape and dimension.
So why is it important? Well, the primary objective of contour verification is to enhance the efficiency, accuracy, and overall performance of logistics and warehousing processes. And who wouldn’t want that in their operations?
In this article, we discuss the crucial role contour verification plays in optimizing warehouse operations and how SICK sensors can help you overcome common challenges associated with this application.
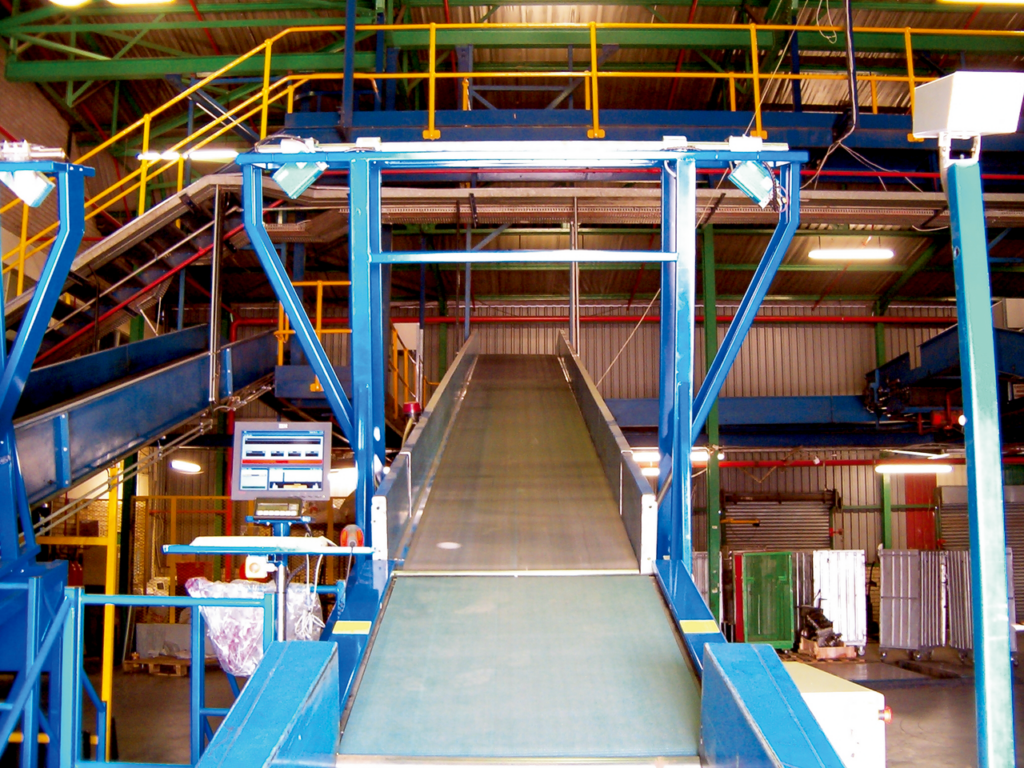
Accuracy in Inventory Management to Optimize Storage and Enhance Sortation
Contour verification helps ensure the accurate measurement and identification of items based on their shape or contour. This is especially important for products that may have irregular shapes or dimensions. Accurate inventory data is essential for efficient warehouse management and preventing errors in order fulfillment. With this, warehouses can also optimize storage space.
The collection of master data from these systems leads to accurate volume measurement, contour verification, and quality checks of incoming goods. Incoming goods are then better sorted for storage optimization, when these systems are used in combination with auto ID and weighing systems. Whether it's during receiving, storage, or order fulfillment, accurately identifying and sorting items based on its contours ensures that the right products are in the right place at the right time.
Many warehouses employ automated handling systems. With this level of accuracy, it leads to the prevention of downtime prevention in automated warehouses caused by damaged goods on conveyor or handling systems. Contour verification enables these systems to recognize and handle items based on their shapes, streamlining the automation process. This contributes to faster and more efficient order fulfillment.
One solution that is best suited for this application is SICK’s VMS4400 with the Contour Verification variant. It is a track and trace system ideal for challenging applications in the field of non-contact dynamic measurement as well as position determination and deformation detection for objects on a diverse range of conveyor systems.
When using a certified system, the dimension data of the objects can be used for billing purposes. The system variant for deformation control detects even the smallest deformations on any of the six sides of cuboid objects and provides a perfect monitoring tool to check objects during goods receipt and storage. Using the Contour Verification system variant, the smallest deformations on any of the six sides of cubic objects can be detected.
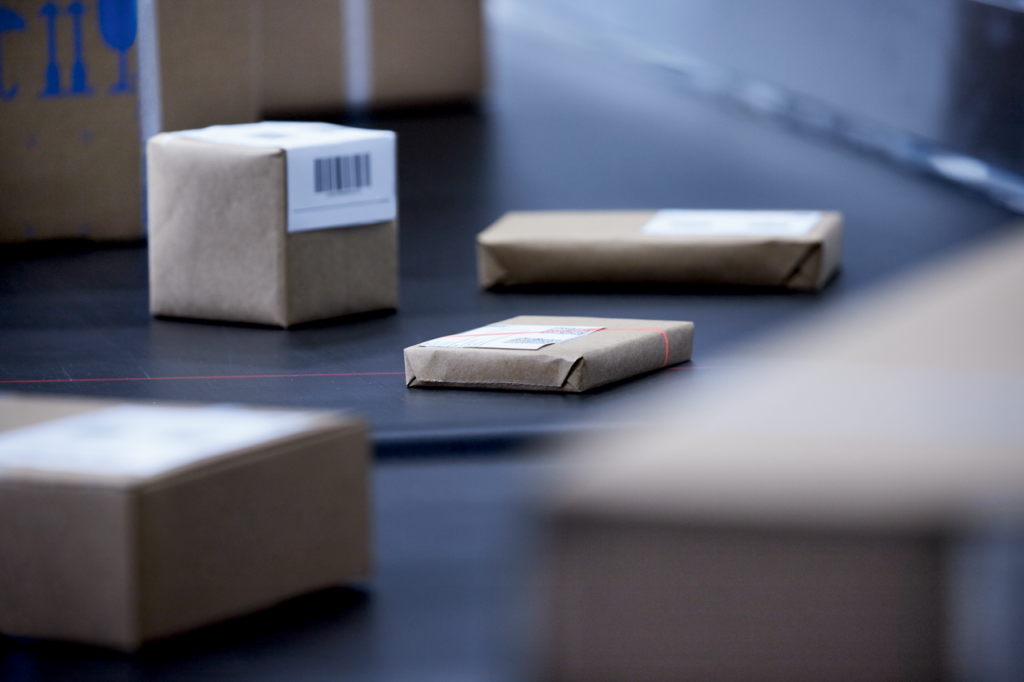
Common Challenges with Contour Verification
Identification of Irregular Shapes and Product Variability
Many products have irregular shapes or dimensions that can vary significantly. Products often come in irregular shapes or have varying contours, making it challenging to develop a one-size-fits-all contour verification system. Dealing with the variability in product shapes requires sophisticated technology and algorithms.
Contour verification allows logistics systems to identify and categorize items based on their unique contours, ensuring accurate handling and storage.
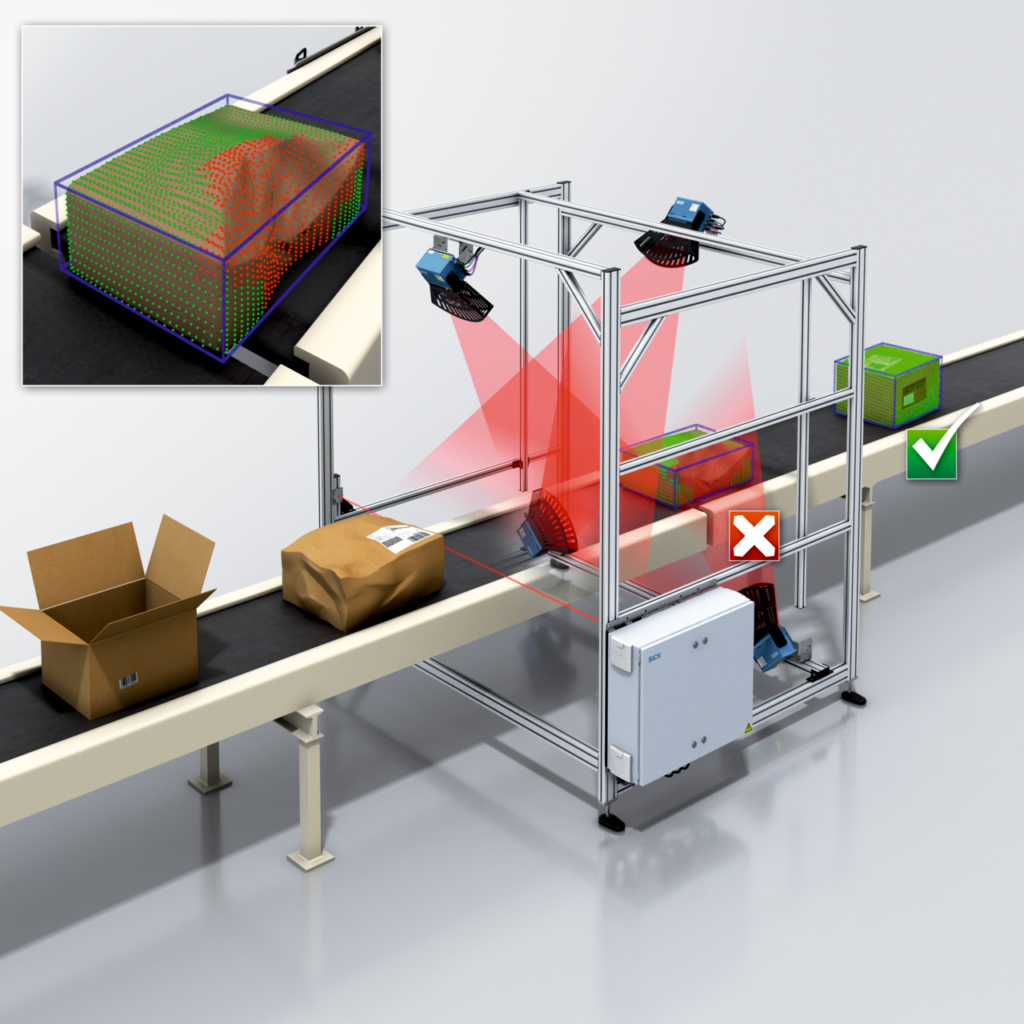
Optimized Storage and Picking
By precisely recognizing the contours of products, warehouses can optimize storage space and improve the accuracy of order picking. This helps in reducing errors, minimizing the risk of damaged goods, and enhancing the overall speed of fulfillment processes.
Achieving high accuracy and precision in contour verification is crucial. Even small errors in measurement or identification can lead to significant issues, such as incorrect inventory records, misplaced items, or errors in automated handling systems.
Automated Handling Systems
Contour verification plays a crucial role in automated handling systems, such as robotic pickers and conveyors. These systems use contour information to grasp, move, and sort items efficiently, contributing to the automation of logistics operations.
Environmental conditions, such as poor lighting or dusty environments, can impact the performance of contour verification systems. Ensuring robust performance in diverse environmental conditions is a challenge that needs to be addressed.
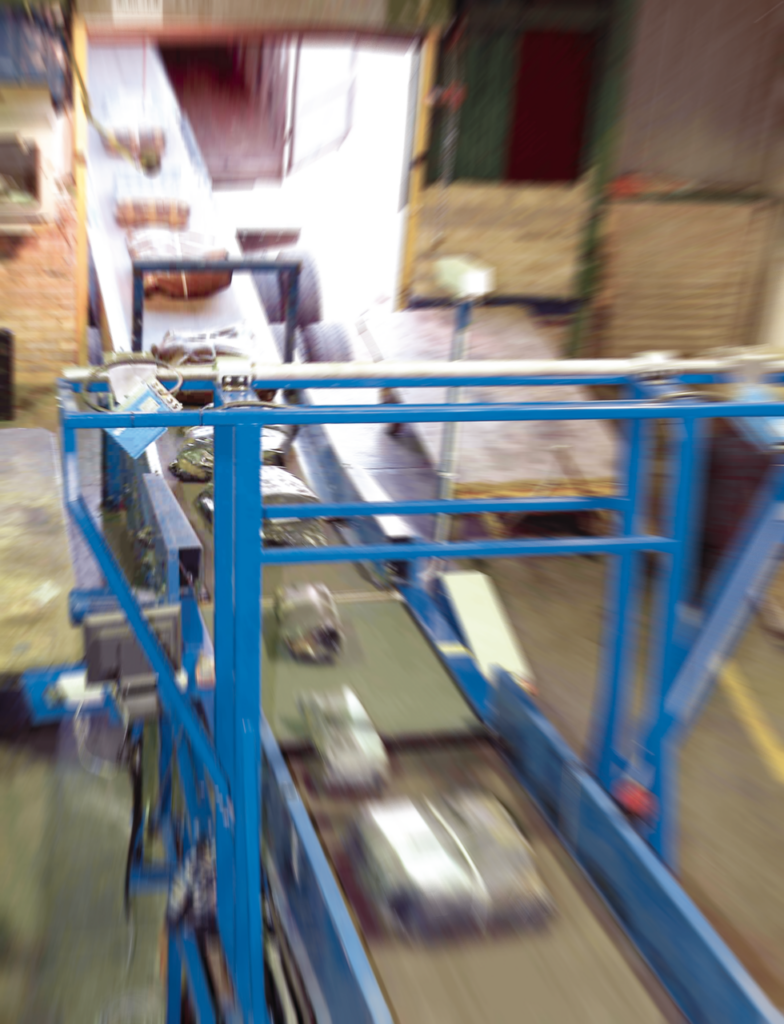
Quality Control to Reduce Errors and Returns
The technology is instrumental in quality control processes by ensuring that products meet specified shape and size requirements. It helps prevent the shipment of defective or incorrectly sized items, contributing to customer satisfaction and compliance with industry standards.
Accurate contour verification helps minimize errors in order fulfillment, reducing the likelihood of sending the wrong products to customers. This, in turn, lowers the rate of returns and enhances customer trust and satisfaction.
Integration with Warehouse Management Systems (WMS)
In dynamic warehouse environments, real-time processing is essential for quick decision-making and timely responses. Contour verification systems need to operate swiftly to keep up with the pace of activities in the warehouse, such as order picking and sorting.
Implementing contour verification systems may require integration with existing warehouse management and automation systems. Ensuring seamless integration can be complex and may involve adapting or upgrading current technology infrastructure.
Contour verification systems are often integrated with WMS to provide real-time data on inventory levels, location accuracy, and order status. This integration improves the overall visibility and management of warehouse operations.
Implementing advanced contour verification technology can be expensive. This includes the cost of acquiring the necessary hardware, software, and training personnel. Smaller warehouses may find it challenging to justify the investment. However, the return on investment is noticeable when operations are streamlined and more efficient.
Adaptability to Diverse Product Catalogs
The introduction of new products with different contours may require adjustments or updates to the contour verification system. Ensuring that the system can adapt to changes in the product catalog is an ongoing challenge.
Contour verification systems are designed to be adaptable to a wide range of product shapes and sizes. This flexibility allows warehouses to handle diverse product catalogs without significant reprogramming or adjustments.
Overall, contour verification in logistics contributes to increased efficiency, cost-effectiveness, and precision in handling inventory. As technology continues to advance, the application of contour verification is likely to play an increasingly important role in shaping the future of logistics and supply chain management.