Understand the differences between these two common encoder types
Encoders are sensors that provide feedback by converting motion into an electrical signal that can be read from a control device. The encoders provide information about position, angle, and rotation counts. Using this information, speed and position can be determined. Encoders are the ideal solution when it comes to precise position detection in industrial automation.
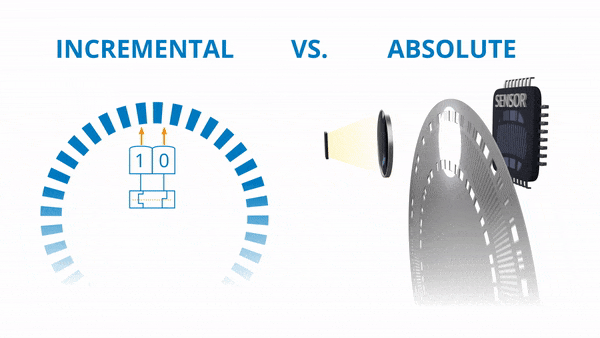
Two of the most common encoder types — absolute and incremental — output different information. Take a look at the quick one-minute video below from one of our engineers to get a better understanding of the differences.
What's the difference?
An incremental encoder is an encoder that outputs either a square or a sine/cosine wave. The number of periods can be counted with the sin/cosine output, while the number of pulses is counted for the square output to obtain speed or velocity information. Incremental encoder feedback is generally used in industries such as packaging, printing, conveyors and converting for speed and velocity control.
Incremental encoders can provide information on the directional travel and speed of an automated guided vehicle (AGV) by being mounted either directly on the motor, on an axel or a revolving wheel. The speed that this measure is used to calculate the position and ensure the security field is observed by the AGV.
In contrast, an absolute encoder outputs a unique positional value for each shaft position. This value is obtained over SSI, Profibus or Ethernet interfaces. Absolute encoder feedback is typically used in transport logistics, robotics, packaging, and staging systems applications to control and monitor position.
An absolute encoder is used to determine the position of a gripper. In this application, plastic bottles are stacked in multiple layers on pallets in a palletizer system. The gripper of the pallet handling machine must be positioned in the X and Y directions. Using an absolute encoder, the exact position of the gripper can be determined and the gripper can efficiently move the pallets.
One of the biggest differences between the two types of encoders is positional information. With incremental encoders, positional information is not retained after a power cycle and does not indicate a specific position, only a positional change. Meanwhile, an absolute encoder will tell you the exact position on power-up and indicates a positional change and a specific position.
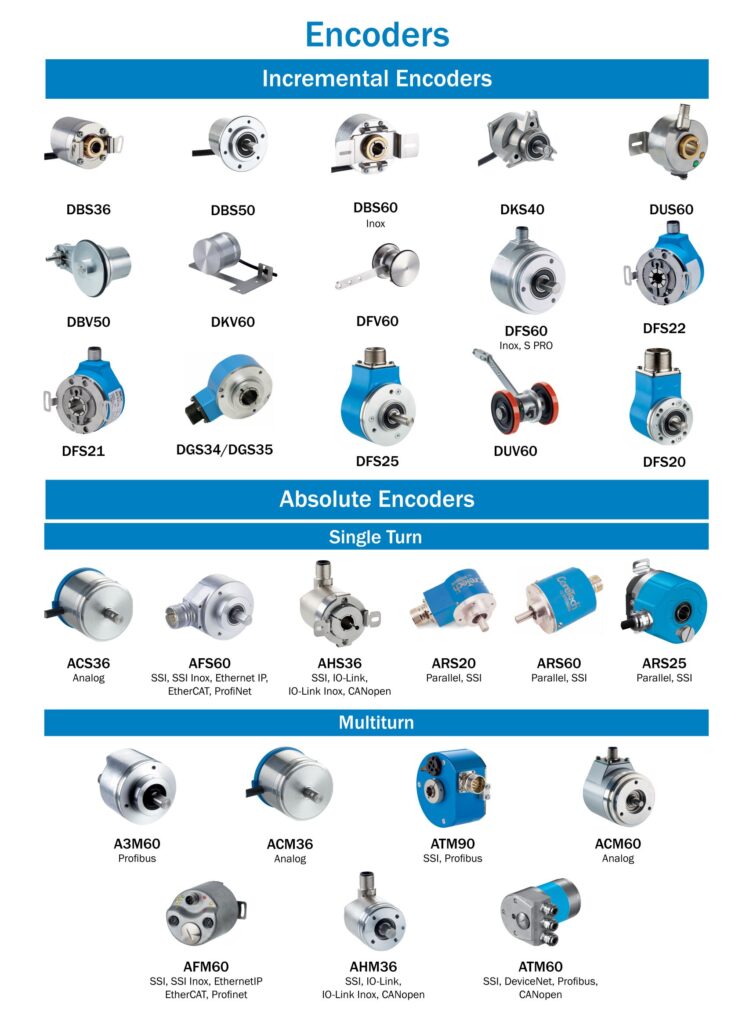