We discuss all you need to know about photoelectric sensors and why you should use them for your manufacturing applications
Photoelectric sensors have become indispensable in manufacturing due to their versatility, long sensing range, high speed, and accuracy. But why are they so useful for the manufacturing industry? And exactly how do they work?
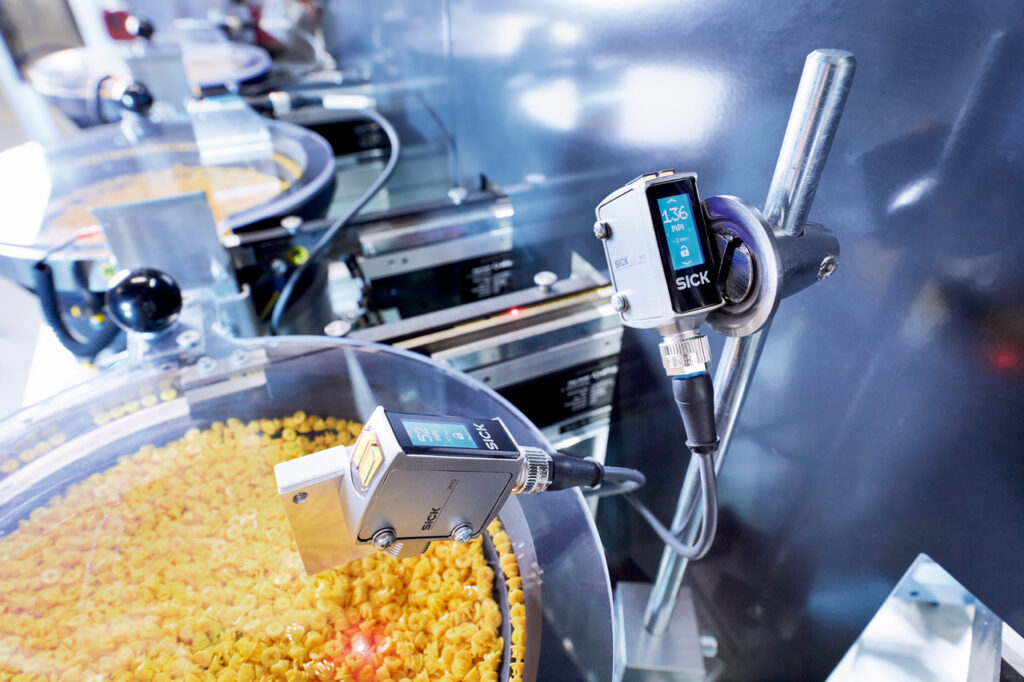
The Ins and Outs of Photoelectrics
A photoelectric sensor works by using light to detect the presence, absence, or distance of an object. The sensor consists of an emitter, which sends out a light beam (usually infrared or visible light), and a receiver, which detects the light.
Depending on the sensor type, the emitter and receiver can be placed opposite each other, housed together with a reflector, or in the same housing. When the light beam is interrupted or reflected, the receiver detects the change and converts it into an electrical signal, which is then used to trigger actions like activating machines or stopping conveyor belts. This allows photoelectric sensors to perform various tasks in manufacturing, such as detecting objects, measuring distances, and ensuring safety.
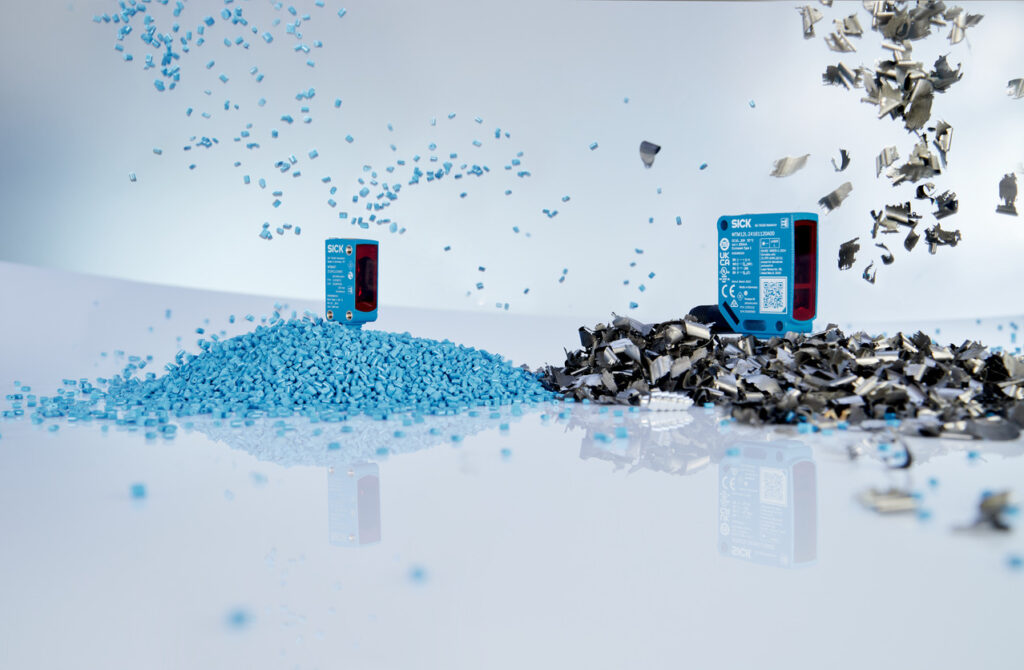
What Can They Detect?
These sensors can detect a wide range of materials, including metals, plastics, glass, and liquids, making them suitable for diverse applications. Their ability to operate without physical contact reduces wear and tear, leading to longer lifespans and lower maintenance costs.
Additionally, photoelectric sensors are cost-effective and perform reliably in harsh environments, such as dusty, wet, or high-temperature conditions. This reliability ensures continuous operation and minimizes the need for frequent adjustments.
Advantages of Photoelectrics
Photoelectric sensors play a crucial role in manufacturing operations due to their ability to enhance efficiency, accuracy, and safety.
- Accurate Detection and Measurement: Photoelectric sensors can detect objects, measure distances, and determine the orientation of items on production lines. This ensures that products are correctly positioned and counted, which is vital for quality control and efficient production.
- Non-Contact Sensing: Unlike mechanical sensors, photoelectric sensors operate without physical contact. This reduces wear and tear, leading to more reliable and long-term performance.
- Versatility: These sensors are adaptable to various applications, from detecting small components in electronics manufacturing to ensuring precise positioning in robotic operations. They can be customized for different tasks, such as detecting objects over long distances or distinguishing between different surface materials.
- Safety Enhancements: Photoelectric sensors are integral to safety systems in manufacturing environments. They can stop machinery when an object or person is detected in a danger zone, preventing accidents, and ensuring a safer workplace.
- Improved Automation: In automated assembly lines, photoelectric sensors provide essential feedback that machines rely on to function smoothly. They help in monitoring the flow of products, detecting missing components, and ensuring that each part of the system works in harmony.
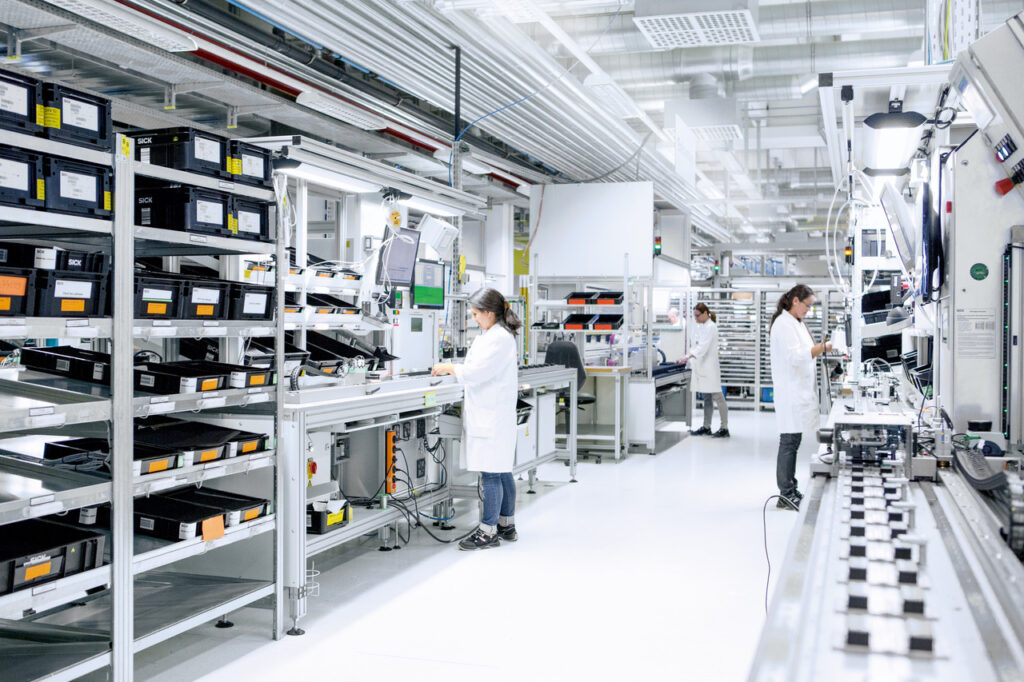
Why SICK Sensors Outperform Others
Highly automated processes require reliable object detection. But no matter the challenge, photoelectric sensors from SICK are the superior choice for an intelligent solution. So what makes them so great?
First, the high detection quality of SICK sensors ensures accurate object detection results. The photoelectric sensors can detect objects precisely even at large sensing ranges. The sensors solve even demanding detection tasks.
SICK also offers different technologies in various designs and housing materials. The resulting diversity of product variants covers many applications and provides a high level of flexibility when designing the application and system. Many are also designed to withstand harsh industrial environments, including exposure to dust, extreme temperatures, and mechanical stresses like shock and vibration.
Because of this design element, many photoelectric sensors from SICK provide a high level of ruggedness and durability. The resulting reduction in downtimes leads to increased productivity of your machines and systems, which gives you a decisive competitive advantage.
SICK sensors are also easy to integrate into automation networks, thanks to modern communication methods like IO-Link, and they offer customization options to meet specific application requirements.
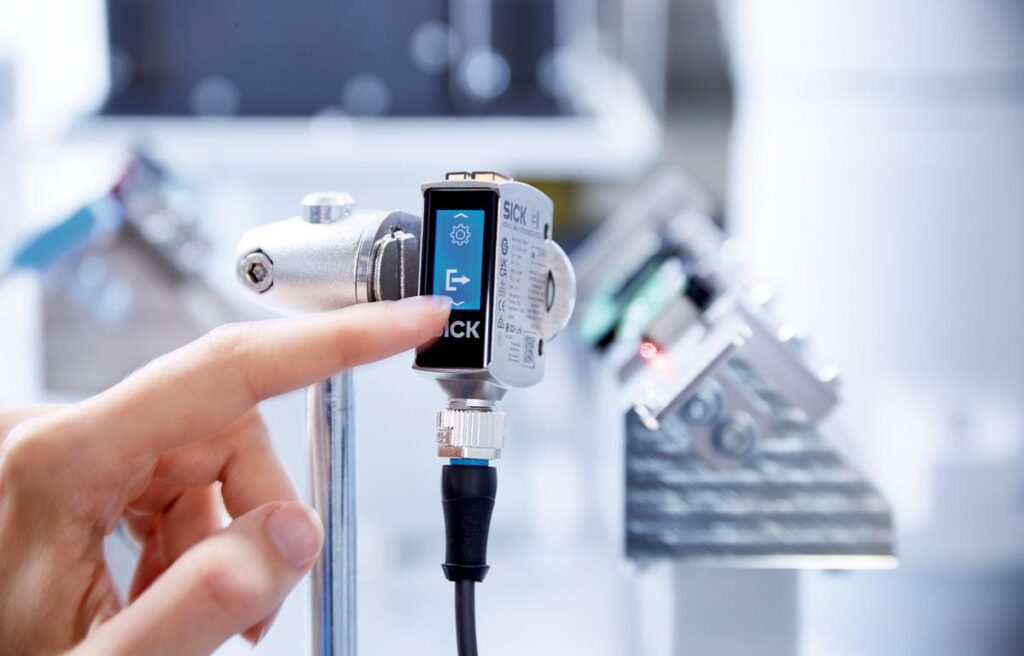
SICK's W10 Photoelectric Sensor
One of SICK's standout photoelectric sensors is the first touchscreen one of its kind. The W10 photoelectric proximity sensor’s ease of use, sturdy design and performance make it ideal for precise object detection in demanding environments.
The touchscreen display is intuitive to use, allowing parameters to be set quickly. Situation-dependent teach-ins allow convenient sensor adaptation to individual applications.
The fact that various MultiMode functions and configurations, such as foreground and background suppression, are combined in a single sensor allows success in a wide range of applications. The W10 photoelectric proximity sensor combines simplicity with versatile performance. It is easy to operate and can be adapted to specific detection tasks in no time at all.
Overall, the reliability, precision, and versatility of photoelectric sensors make them indispensable in modern manufacturing, contributing to higher quality products and safer, more efficient operations.