We explore how sensors help to optimize automated storage and retrieval systems (AS/RS) to enhance performance in logistics operations
Automated Storage and Retrieval Systems (AS/RS) have become the backbone of modern logistics, driving performance to new heights. At the heart of this transformation lie an array of sensors, each with a specific role in enhancing the capabilities of AS/RS.
In this article, we delve into the various types of sensors employed in AS/RS and their invaluable contributions to the seamless orchestration of logistics operations.
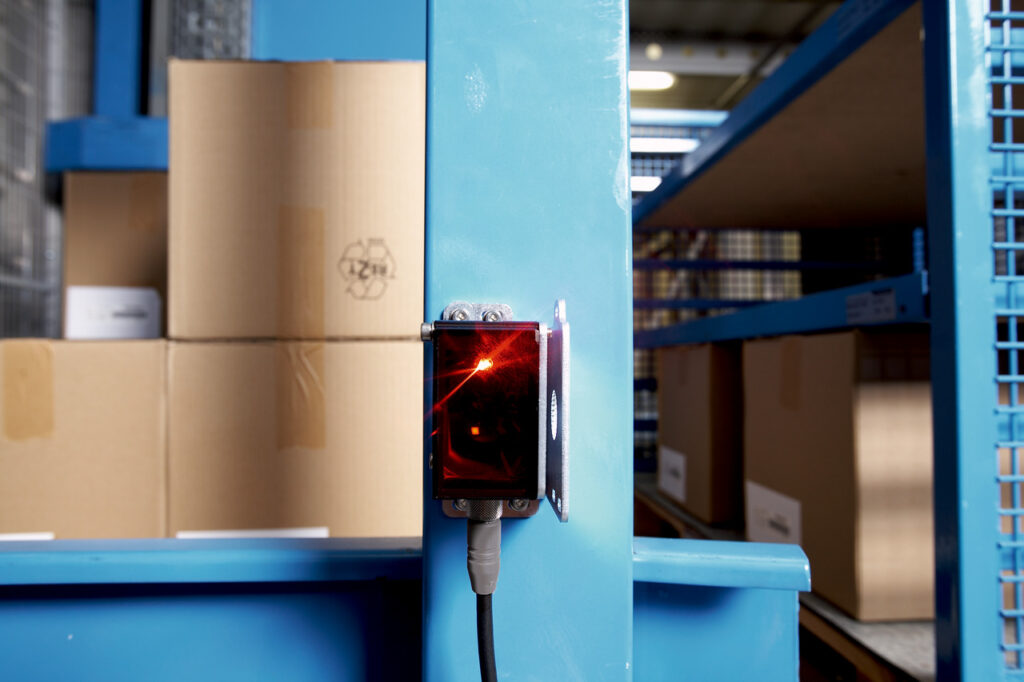
Position Sensors: Precision in Motion
Position sensors are the navigators of an AS/RS, ensuring that every movement within the system is accurate and controlled. The positioning of the driving and lifting unit of an AS/RS can be accomplished using distance sensors, wire draw encoders, or using linear measurement sensors and a bar code tape. To enable the driving unit to move at high speeds and accelerate quickly, the sensors must have a high resolution, repeatability, and measuring speed.
Encoders play a pivotal role in determining the position of moving components, such as cranes or shuttles. These sensors provide real-time feedback, enabling the system to precisely locate items within the storage structure.
Laser distance sensors are valuable components in AS/RS for precise positioning of racking and shelving structures. These sensors utilize laser technology to accurately measure distances to objects, providing crucial feedback for the automated movement and placement of storage elements within the AS/RS.
Get the Best Position Sensors from SICK: OLM100, Dx100, HighLine, Dx50
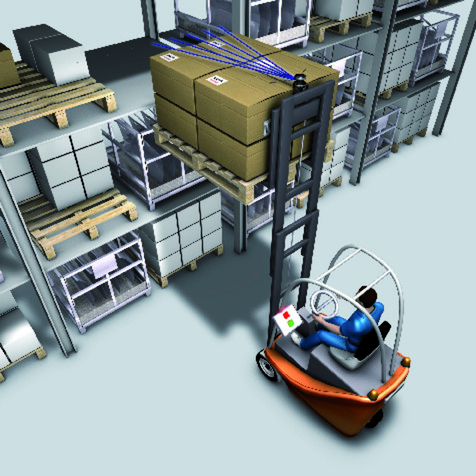
Distance Sensors: Empty Bay Detection
Before a load carrier is stored on a shelf, it is first necessary to check whether the allocated storage location is empty. Besides being able to detect different object colors, it is also necessary to support single-depth or double-depth storage. Distance sensors and laser scanners offer reliable solutions for this task.
Distance sensors are instrumental in detecting empty bays within an AS/RS. These sensors, typically ultrasonic or laser-based, play a crucial role in optimizing storage space utilization, facilitating efficient inventory management, and enhancing overall system performance.
Distance sensors continuously monitor the distance between storage bays or shelves within the AS/RS. By emitting ultrasonic waves or laser beams and measuring the time it takes for them to reflect back, these sensors can accurately determine the distance to nearby surfaces.
When an item is retrieved from a storage bay, the absence of an object alters the distance measured by the sensor. By detecting this change in distance, the sensor identifies the bay as empty. This real-time detection enables the AS/RS system to update its inventory records promptly and accurately reflect the availability of storage space.
Get the Best Photoelectric Sensors from SICK: PowerProx, Dx35
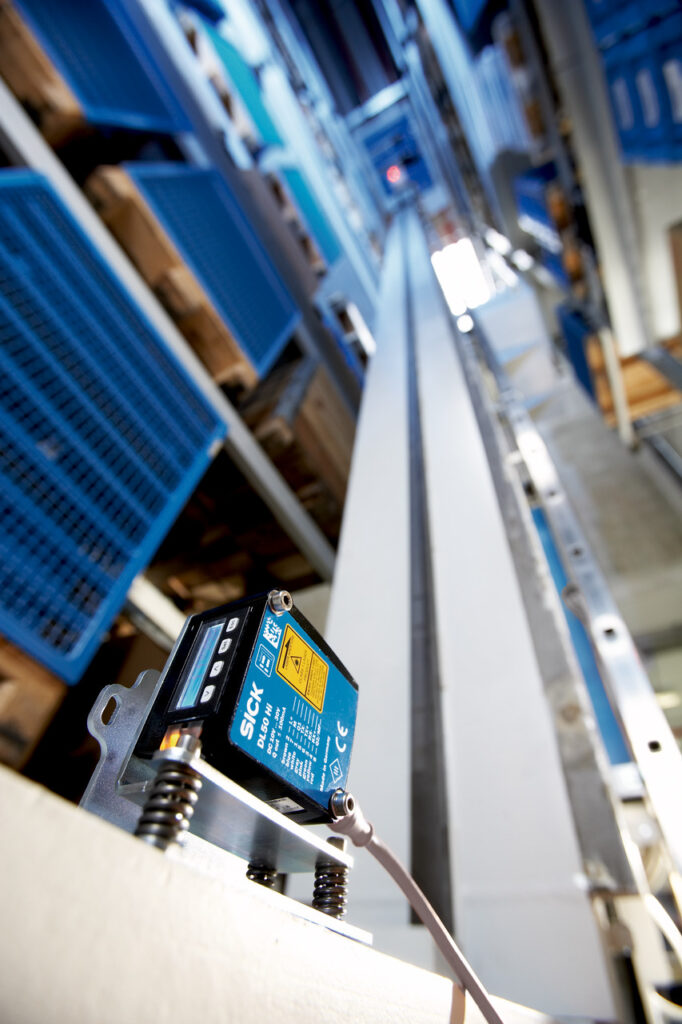
Photoelectric Sensors: Occupied Load Carrying Unit
Efficient load management is paramount in logistics, and load sensors are the unsung heroes in achieving this balance. Before the carton, container, or pallet is placed on the load-carrying unit, it is necessary to check whether it is actually empty.
Photoelectric, retro-reflective sensors from SICK provide an optimal solution to this application, even in the case of challenging surfaces. These sensors utilize light beams to detect the presence or absence of objects, enabling precise monitoring and control of loads.
When deployed at strategic locations within the AS/RS, photoelectric sensors can detect the presence of loads on conveyors, shuttles, or other moving components. When a load interrupts the light beam emitted by the sensor, it triggers a signal indicating the presence of an object. This load detection capability enables the system to accurately track the movement of goods throughout the storage and retrieval process.
In addition, you can ensure the proper positioning and alignment of loads within storage locations or on conveyor belts within the AS/RS. By detecting any protrusions or misalignments of loads, these sensors provide feedback to the system's control mechanism. This allows the system to adjust the movement of the loads, ensuring that they are accurately positioned and securely held during storage and retrieval operations.
Get the Best Photoelectric Sensors from SICK: G6, G10, W16
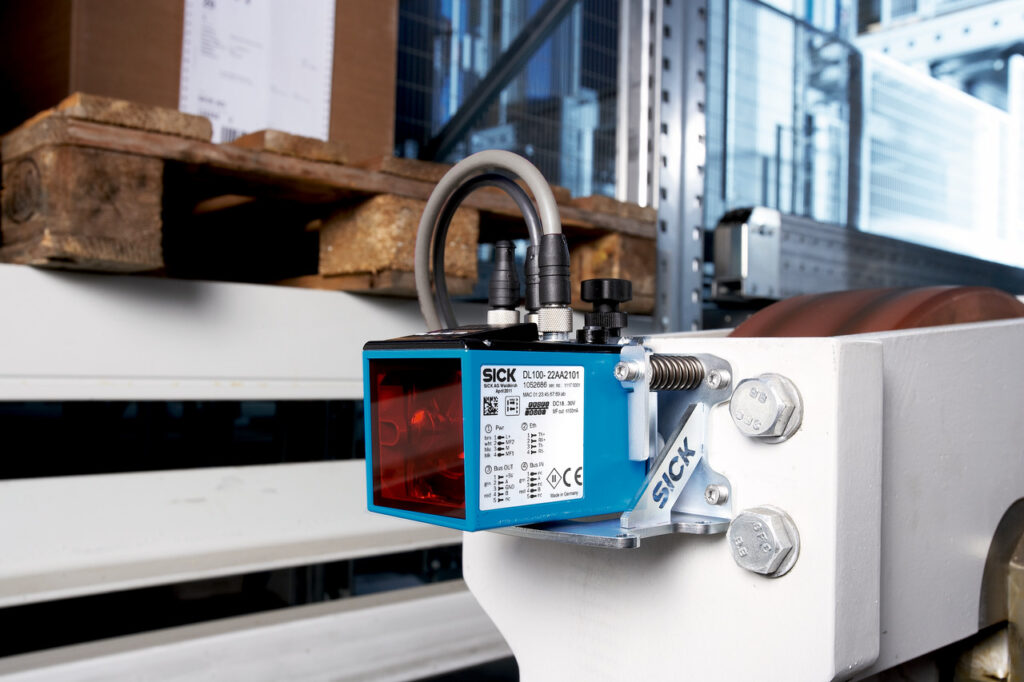
Photoelectric Sensors: Protrusion Monitoring
After the pallet has been placed on the load-carrying unit, a photoelectric, retro-reflective sensor checks whether the pallet is still protruding and could cause a collision. Protrusion monitoring involves detecting any objects or loads that extend beyond specified boundaries or clearance limits within the AS/RS environment. Thanks to their low sensitivity to ambient light and reflection, the sensors ensure a stable process is carried out.
Photoelectric sensors are strategically positioned along the edges of storage locations, conveyor belts, or other moving components within the AS/RS. These sensors emit a light beam that serves as a virtual boundary or clearance limit. Any object or load that protrudes beyond this boundary interrupts the light beam, triggering the sensor to detect the protrusion.
In addition to monitoring boundaries and clearance limits, photoelectric sensors help detect obstacles or obstructions within the AS/RS environment. Any object or load that protrudes into the path of moving components can be detected by these sensors. This enables the system to implement appropriate collision avoidance measures, such as slowing down or stopping the movement of the affected components to prevent damage or accidents.
Get the Best Sensor Options from SICK: FlexChain, W26, G10

Barcode and RFID Sensors: The Code for Efficiency
Barcode and RFID sensors bring a new level of intelligence to inventory management within AS/RS. Barcode readers scan barcodes on items, facilitating accurate tracking and identification. RFID readers, utilizing radio frequency identification, enable automated, real-time tracking of items throughout the storage and retrieval process. These sensors not only enhance accuracy but also streamline the logistics chain by providing instant data on inventory levels and locations.
Barcode sensors labels are attached to items, pallets, or containers to capture the encoded information contained in the barcode. With this, you gain accurate item identification as the system can verify the identity of each item, reducing the risk of errors in inventory records.
In addition, barcode sensors facilitate real-time tracking of inventory movements within the AS/RS. Each time an item is stored or retrieved, the barcode sensor captures the relevant data, allowing the system to update inventory records instantly.
As a result, logistics operators can streamline order fulfillment processes within the AS/RS. By scanning barcode labels on items, the system can quickly locate and retrieve the required products, expediting the picking and packing operations. This also contributes to maintaining accurate inventory records within the AS/RS. By ensuring that each item is correctly identified and tracked, these sensors minimize discrepancies and errors in inventory counts.
As an alternative, operators could use RFID sensors to wirelessly communicate with RFID tags attached to items, pallets, or containers. These tags contain electronically stored information that can be read and processed by RFID sensors. These provide similar benefits as barcodes, with improved inventory visibility and automated identification of items in the AS/RS.
Get the Best Barcode and RFID Sensors from SICK: CLV61x, RFU630
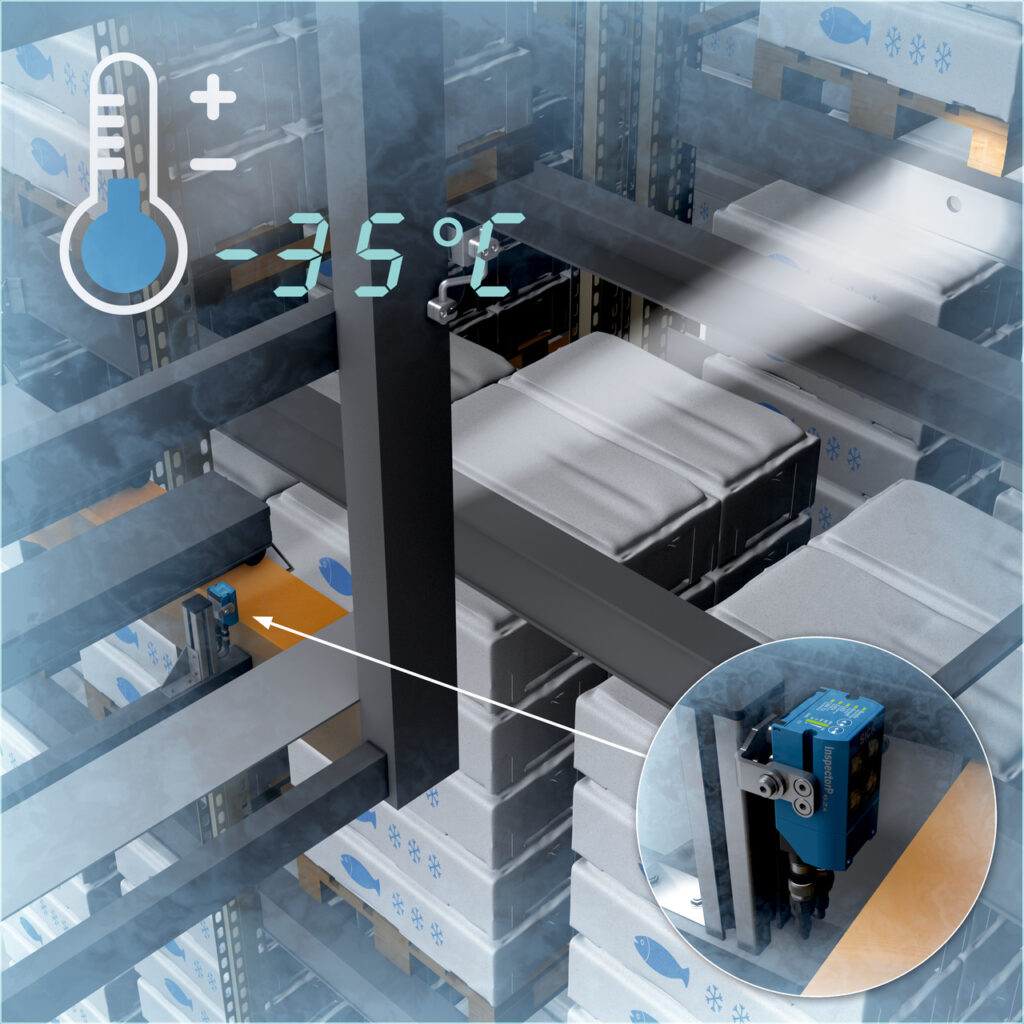
Vision Sensors: Rack Fine Positioning
Incorporating vision sensors into AS/RS introduces a visual dimension to the system's capabilities. Cameras capture visual data, enabling tasks such as object recognition, quality control, and navigation. Vision sensors play a crucial role in identifying items, confirming their condition, and aiding in the efficient movement and placement of goods within the storage structure. This visual intelligence enhances the overall flexibility and adaptability of the AS/RS.
Vision sensors can identify and recognize objects with a high degree of accuracy. By analyzing visual data captured by cameras, these sensors can distinguish between different items based on their size, shape, color, or other characteristics. This capability allows the AS/RS to precisely identify the objects it is handling, facilitating accurate positioning and placement within the storage system.
The InspectorP Rack Fine Positioning for cold storage is exceptionally suited for fine positioning of driving and lifting units in cold storage facilities because it can be employed without difficulties at temperatures down to -35 degrees Celsius. After absolute positioning of the driving and lifting unit, the 2D vision sensor allows precise fine positioning in front of the storage bay even in double deep applications for pallets.
In addition, you gain dynamic adjustment of positioning parameters based on real-time feedback. By continuously analyzing visual data, these sensors provide instant feedback to the system's control mechanism, allowing it to make rapid adjustments to the positioning of items as needed. This ensures that items are placed with precision, even in dynamic or changing environments within the AS/RS.
Real-time Visibility and Analytics: Data-Driven Decision Making
The integration of sensors in AS/RS provides a wealth of real-time data, empowering logistics operators with valuable insights. Data and analytics capabilities enable comprehensive monitoring of system health, inventory levels, and overall efficiency. With the ability to make informed decisions based on this data, operators can optimize processes, identify areas for improvement, and respond promptly to changes in demand or system performance.
In conclusion, the diverse array of sensors employed in AS/RS plays a pivotal role in transforming logistics operations. As logistics operators continue to embrace automation, the symbiotic relationship between AS/RS and sensors promises a future where logistics is not just a process, but a seamlessly orchestrated dance of precision and intelligence.