Comparing and contrasting 2D and 3D machine vision
Machine vision solutions give machines the gift of sight, enabling manual inspection tasks to be supported, or even completely replaced, by machine vision solutions. Machine vision technology is used to automate production processes in numerous industries and applications.
When do you need a 2D vision solution and when do you need a 3D vision solution? This is a question that often arises. When does which technology make sense? This blog article looks at these questions and provides instructions on how to correctly use the technology.
Recent years have seen significant progress being made in the field of machine vision. Solutions are becoming more affordable and thus more economically viable. They have the potential to significantly improve the efficiency of industrial applications.
Increasing competitive pressure, a shortage of skilled workers, high quality standards and the need to manufacture customized products in shorter cycles have all made production automation a goal worth trying to achieve. The corresponding technologies are solutions that use optical sensors and machine vision tools to perform tasks such as quality control or transmit coordinates and position data to a robot.
Powerful vision technologies enable precise object capture and analysis in real time. This leads to improved product quality, lower error rates and optimized processes. Further benefits include increased yield, throughput and customer satisfaction, as well as reduced resource consumption.
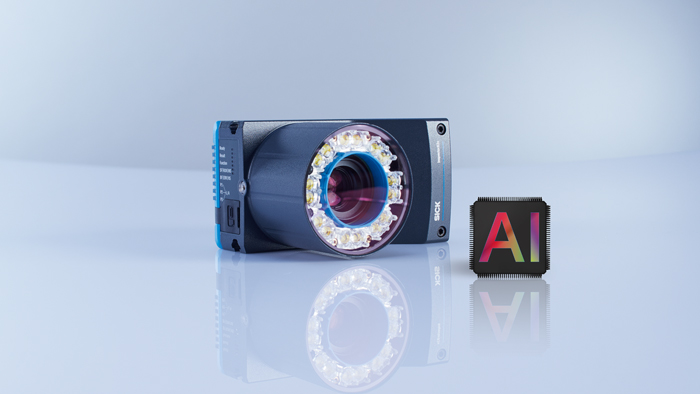
WHAT IS 2D VISION TECHNOLOGY?
2D vision solutions lay the foundation for many industrial automation processes. A major advantage of 2D technology is the precise detection of patterns and contrasts on differently shaped object surfaces, as well as the accurate detection of irregularities and defects.
2D solutions are particularly useful when the information lies in the difference in contrast. This technology is currently very widespread. 2D vision is intuitive and highly flexible: different types of light sources can be used to optimize the performance of the vision solution. This allows 2D vision cameras to accurately capture the desired object properties.
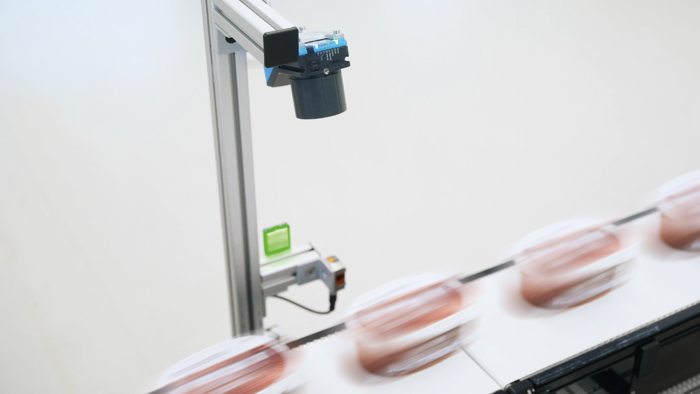
2D VISION APPLICATIONS
With the aid of user-friendly software, these solutions are easy to integrate into machines and systems and are simple to operate. Robust and adaptable, they are ideally equipped to meet the challenges of industrial environments and a variety of tasks. These include:
- Completeness check and assembly test
- Detection of defects
- Detection of foreign objects
- Inspection and classification of objects
- Code reading and label verification
The strengths of 2D vision solutions lie in their simplicity, cost-effectiveness, versatility and easy integration into existing processes. However, the technology is limited to applications where depth information is not required.
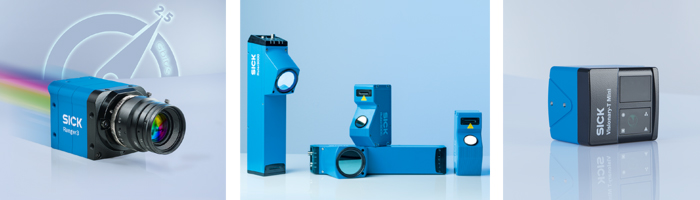
WHAT IS 3D VISION?
3D vision solutions utilize depth perception to provide detailed images of an object's geometry. The object's shape or color has no influence on the application. 3D solutions are primarily used when the information lies in the difference in height.
In contrast to 2D technologies, 3D technologies aim to capture the shape and spatial arrangement of objects. A distinction is made between the following technologies:
Scanning technologies
These capture 3D images on a profile-by-profile basis, either by moving the object through the measurement area or by moving the camera over the object. This method requires a constant or known motion, e.g. using an encoder.
Snapshot technologies
These produce detailed 3D images with a single shot. No movement of the object or camera is required, but the images are often less accurate than those produced by scanning technologies.
3D VISION – A DETAILED LOOK AT THE VARIOUS TECHNOLOGIES

Laser triangulation
A laser beam is projected onto an object and a camera records the reflected light. By measuring the position of the reflected laser line on the camera sensor, the object's height position can be calculated. The camera records the reflected light sequentially and creates a three-dimensional representation of the object from the recorded profiles.
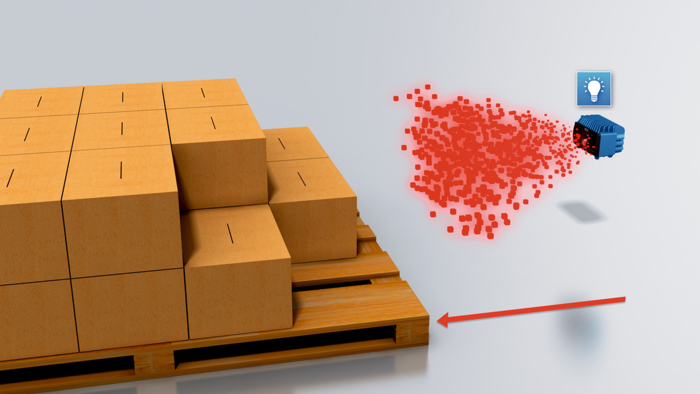
Time-of-flight technology
This snapshot technology measures the time it takes for a light beam to travel to its target and back, thus creating a 3D image in real time. Time-of-flight technology is particularly suitable for applications with a large field of view and working distances of more than half a meter.
Stereo technology
This snapshot technology works similarly to human vision by combining two 2D images from different positions. It is highly suited to applications with a wide field of view and to outdoor use. Measurement accuracy can be improved with an additional light source that projects patterns onto the object.
3D VISION APPLICATIONS
3D vision is used, for example, in quality control and robot vision applications that require precise measurements and detailed analyses. Applications include:
- Completeness and assembly check
- Detection of defects
- Detection of foreign objects
- Measurements
- Classification and sorting of objects
- Localization of objects
- Control of robots/gripper arms
The major advantage of 3D vision is that it provides a detailed 3D image of an object. This is important for applications where depth, volume and precise measurements are crucial.
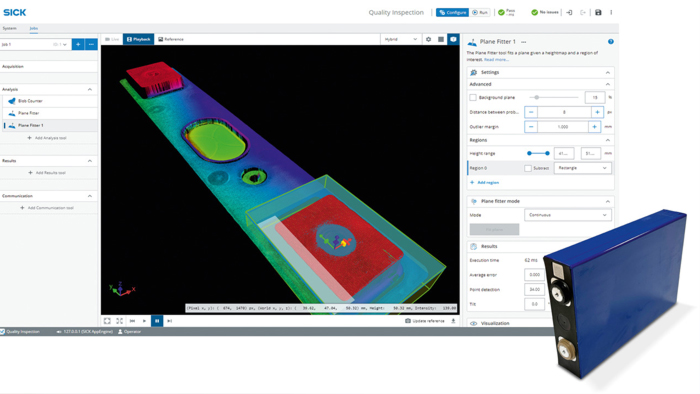
THE VISION SOLUTION PORTFOLIO FROM SICK
Depending on the customer's requirements and the complexity of the task, SICK can always offer the right solution. From individual vision sensors and application-specific systems for vision sensors to digital solutions and services for machine vision: SICK's vision portfolio includes a wide variety of different cameras and solutions for machine vision tasks.
Regardless of whether 2D or 3D cameras are used, the SICK Nova software supports the quick and easy configuration of vision applications. Tailored to the task and area of application, SICK offers a wide range of state-of-the-art solutions as well as comprehensive consulting to find the right machine vision solution for your specific challenges.