Keeping track of incoming goods with digital detection using SICK’s new software solution
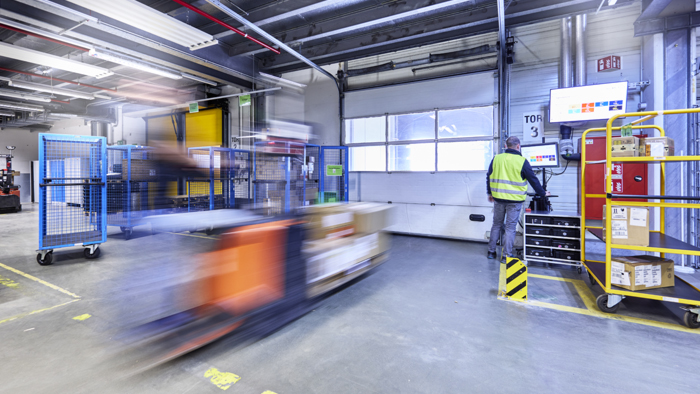
Every day, the incoming goods department at the automotive supplier Continental logistics center in Regensburg, Germany, receives up to 400 individual parcels and countless pallet consignments. These include a wide range of standard and express shipments, priority and less urgent deliveries, complete consignments, individual batches, and the occasional misdirected or damaged parcel. All of these are delivered by numerous parcel firms, each with their own unique proof-of-delivery systems.
“It is not completely unheard of for a parcel to disappear without a trace, as you can soon lose track of what’s happening in these kinds of scenarios,” said Marco Immisch, the man in charge of the Continental logistics center in Regensburg.
Because of this, Continental and SICK have joined forces to achieve transparency in incoming goods. Building on a test version, the two partner companies gradually developed the Incoming Goods Suite (IGS), a system solution for digitalized incoming goods handling, to the point of operational readiness – a solution steeped in real-world experience.
The ability to reduce the number of lost parcels became a priority for Otto Schweiger from Continental, who handles processing technology in the logistics center’s incoming goods department.
“Whether it was the uncertain status of shipments that had been announced but not necessarily received or parcels getting held up in incoming goods and being assigned to the wrong category, it all made pinpointing individual consignments a complex business,” Schweiger said. “It tied up resources, consumed valuable time, disrupted other processes, cost money, and resulted in frustration, both for incoming goods and in-house recipients.”
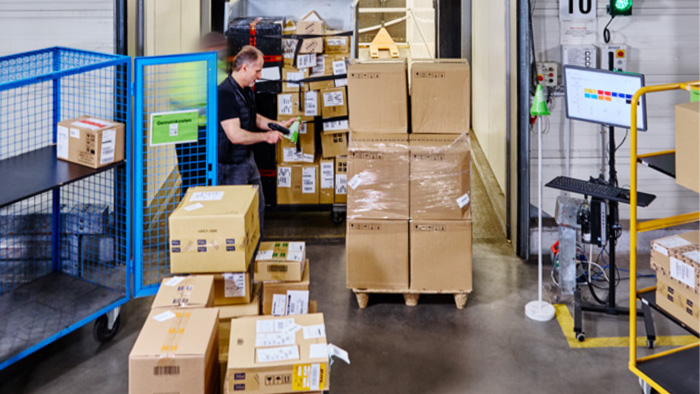
Similarly frustrated about a complex system that was supposed to make life easier, the two Continental managers became interested in the IGS system from SICK. Continental was looking for a simple, cost-effective, and flexible system that could be implemented quickly.
“There was still work to do to modify the IGS version at the time to cover all processes and logic systems used in incoming goods at Continental in Regensburg and to deploy it as a live system that needed to be connected with a data center,” Schweiger said.
A further consideration was that Continental was not looking for a proprietary solution for exclusive use at its own company.
“Therefore, we entered into a partnership agreement with SICK, the aim being to take over the finished system while also designing it as a marketable solution for other companies,” Immisch said.
Alexander Aberle, Head of HSCC Product Management at SICK in Waldkirch, and his distribution colleague Carsten Kunze from SICK Vertriebs-GmbH in Düsseldorf worked in tandem with Continental to create the first test of this system.
“This allowed us, in tandem with Continental, to gradually transform the first stand-alone test system into a network-enabled live system by adding application-specific extension modules,” Aberle and Kunze said. “As such, the current incarnation of IGS has been developed from the bottom up – in a step-by-step process that always centered on customer preferences and practical needs.”
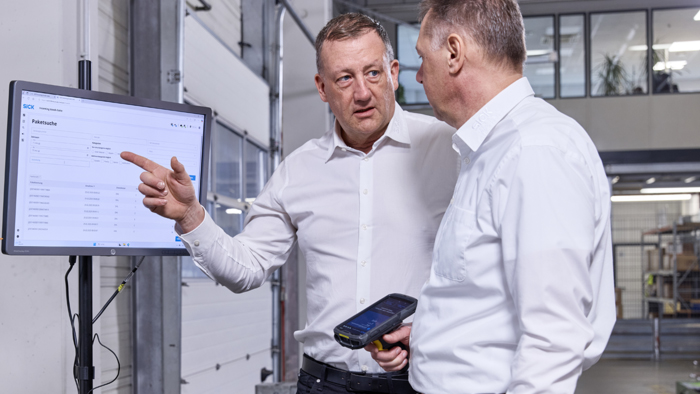
IGS functionality gradually expanded
The joint functional development process for IGS began with a stand-alone test system. Mobile devices – and their functionality, user friendliness, and therefore acceptance – represented another focal point.
“The system’s performance and ergonomics were continuously optimized, and a wealth of features incorporated within the Operator Assistance App developed by SICK, which assists users with the real-time parcel registration process,” Schweiger said.
The basic functions, such as optimization of the user interface and the automatic recognition of labels from different parcel companies, were included within the IGS solution. Custom features, e.g., storage place allocation (which Continental uses to temporarily store parcels on pallets), were developed as functional extension modules.
“Continental or any other company can tailor the functionality of IGS to their own requirements,” Aberle said.
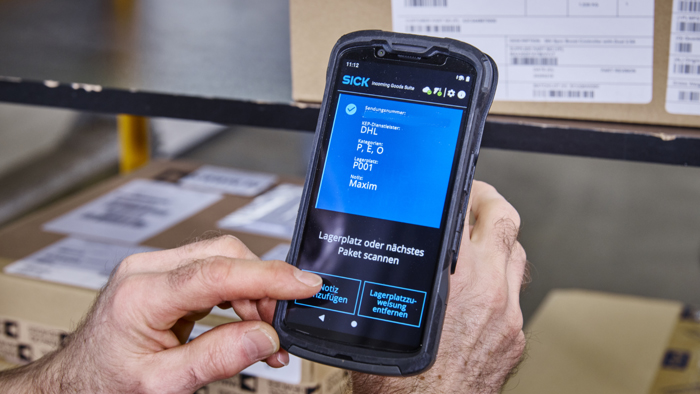
The Operator Assistance App, developed by SICK, assists users with the real-time parcel registration process.
IT integration of the software within the Continental data center in Regensburg was also completed step by step.
“The standalone version was initially limited to incoming goods,” Immisch said. “In order to nonetheless provide SICK with remote access for support and service reasons at this stage of development, a corresponding connection was set up via VPN and a mobile network. Subsequent integration within the data center could be prepared alongside testing of the increasingly more functional IGS.”
Today, each parcel is entered into a database in real time when it is scanned by a mobile computer. The central overview list not only stores the shipment number, but also other shipment-specific delivery and processing data, e.g., tracking numbers, assignment to parcel delivery providers, data and time information, priority status, storage location ID, and information on completion of the internal transport process.
Alongside improvements to the processes themselves, IGS also enables the aggregation of incoming goods data for specific analysis. The IGS solution can generate and show data analysis in real time to ascertain, for example, which providers have delivered how many parcels and when, the condition of these parcels, the volume of priority shipments, and the times at which delivery volumes peak and diminish.
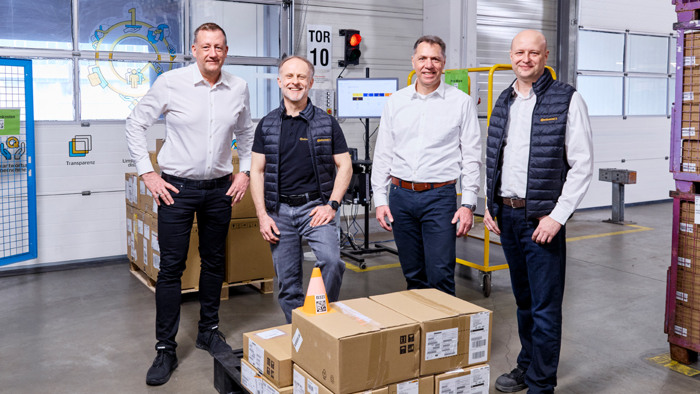
Unearthing valuable incoming goods data
Digitalization begins with data collection; in this regard, each incoming consignment harbors valuable data. Together with SICK, the managers at Continental have successfully mined this data, transforming what was once a “black box” into a transparent incoming goods department.
But the potential extends still further, as Marco Immisch and Otto Schweiger now want to use this data for claims management documentation. The idea is to photograph damaged shipments as soon as they are received and registered, before quickly and unambiguously associating this data with the existing shipment details.
The relevant supplier and parcel company data is completed using the ERP system, meaning that a digital complaint instruction can be automatically generated at the push of a button – and eventually via AI. Another idea is to adapt the IGS to the outgoing goods and shipping departments, as there is considerable overlap in terms of requirements.