How an autonomous robot helps gardeners transport potted plants
To ensure plants grow optimally, pots sometimes weighing over 20 pounds in a tree or garden nursery need to be moved and rearranged regularly — each and every day. It’s arduous and strenuous work, so it’s essential that visionaries like Pierre Delarboulas and Adrien Jauffret from Instar Robotics in France developed an innovation. Their “Trooper” autonomous robot transports potted plants and contributes to automation in the horticultural industry. The MRS1000 SICK 3D LiDAR sensor ensures accurate navigation and environment perception in this harsh environment.
Instar Robotics is a young start-up company that was founded in 2018 by Delarboulas and Jauffret. Pursuing a long-time interest, both have their doctorates in the fields of artificial intelligence and robotics. Their mission: create practical robotics that help humans in their everyday life and let them focus on their profession.
Taking the burden off tree nurseries
The founders of Instar Robotics had the desire to work in farming from a young age. This industry in particular poses numerous technical challenges on robotics. The conditions in outdoor applications are extremely variable and constantly changing (like the weather, ground, etc). Because of this, it was clear a robot solution that was adaptable, flexible, and reliable was needed.
After extensive research, Delarboulas and Jauffret came across the horticultural sector and the task to transport potted plants — a predominantly manual, frequently recurring, and physically strenuous job. Furthermore, these tasks were mainly performed by seasonal workers who were becoming increasingly hard to find due to the uncontrollable conditions.
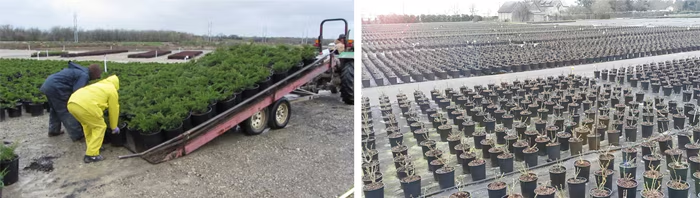
Two of the tasks in a tree nursery are particularly important for the quality of the plants: placing them either closer or further apart. At the beginning of their life cycle, keeping the plants closer together helps optimize the available space. In the preparation phase and during potting, the pots are arranged next to each other “in rectangles” to support the initial growth phase. After a certain time, the pots are then transported individually to a different location in the nursery. This enables the plants to thrive and stops the spread of diseases. Some nursery operations are several hundred (if not thousand) acres in size, and have more than 100,000 pots that can weigh up to 22 pounds each that need to be regularly moved. You can imagine how this highly repetitive task would benefit from an automated solution.
Trooper was born
Instar Robotics developed Trooper, a small autonomous robot to help gardeners and tree nurseries transport pots from point A to B within their operation, and to place them either closer together or further apart.
What quickly emerged was the problem of environment perception. The robot needed to be able to…
- Move about independently
- Understand its environment
- Recognize hindrances
- Recognize the pots
- Position itself correctly to grasp them
- Orient itself
…and do all of this in a safe manner and in collaboration with humans!
It therefore made good sense to use a 3D LiDAR sensor — and, in the end, Instar Robotics chose the MRS1000 multi-layer scanner from SICK.
How can the Trooper move around autonomously? The MRS1000.
The MRS1000 is a multi-layer scanner and, so to speak, “the eyes of the Trooper,” says Delarboulas. It generates a point cloud that provides the distance to the object, which is then used to calculate the route, and can also be used to model a reconstruction of the objects. An algorithm developed by Instar Robotics recognizes the objects by searching for circles (i.e., pots), that were reconstructed with the help of the point cloud and four layers of the LiDAR sensor.
The sensor also determines the reflection factor of the object, which makes it easier to distinguish the objects by their color. This increases the responsiveness of the robot to make better decisions and to interact appropriately with the environment.
3D LiDAR acts as the “eyes” of the Trooper
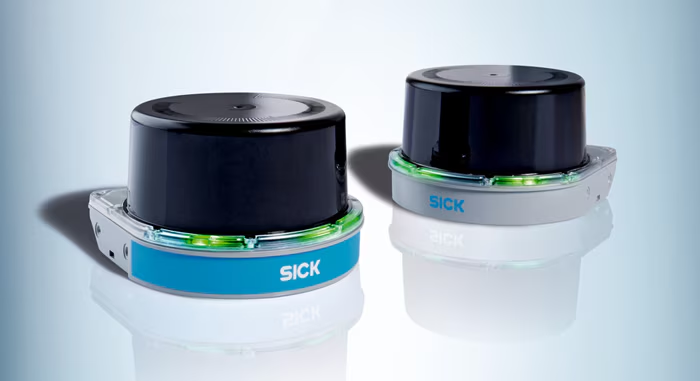
The performance of the MRS1000 was one of the key factors in the success of the project. It detects and measures objects within a field of view of 275°. The ability of the MRS1000 to take simultaneous measurements on four different levels enables it to detect objects in detail and track their direction of movement. The rugged housing is resistant to dust, heat, and moisture, and, thanks to the HDDM+ technology, is also especially reliable and efficient even in fog or strong light. This met all of Instar Robotics’s requirements.
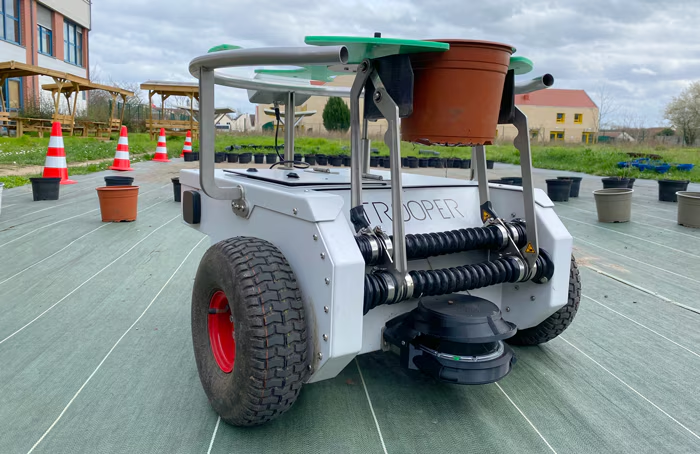
Serious cost savings for nursery operations
The horticulturalists agree: “There’s before the Trooper, and there’s after the Trooper,” says Delarboulas. There was a glaring lack of workers in this sector, due to the strenuous work of placing the pots closer together or further apart. Thanks to the robot, the employees are now relieved from this task and have more time for more demanding and motivating tasks.
Regarding productivity, the project also paid off. The robot is never tired, works in any weather, and places the pots in the optimal location. This saves up to 15% of the working area in the nurseries.
It takes about four to five years to amortize the investment in a Trooper, depending on the machine utilization rate. This is a relatively short time for an investment in the agricultural sector.
The SICK team backs the Trooper, rain or shine
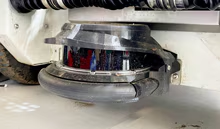
“There is always someone to support us,” Delarboulas comments, regarding the various SICK teams in France. The Trooper was incrementally designed and continuously improved in collaboration with SICK. For example, the sensor was initially very vulnerable to external conditions (rain, earth) due to its position on the robot. It needed to be shielded with a customized hood. After an investigation by the SICK team, compact protection was designed in order to achieve even better performance — the best of both worlds for both parties.
Wondering what’s next for Trooper and the industry?
There is no lack of ideas for new products. Three new tools are currently being developed to extend the capabilities of the Trooper and address the issue of a labor shortage in the horticultural industry:
- The cutting and pruning of plants
- Pest control by wrapping plants with adhesive strips
- Soil treatment, e.g., uniformly distributing fertilizer around the plant in the pots
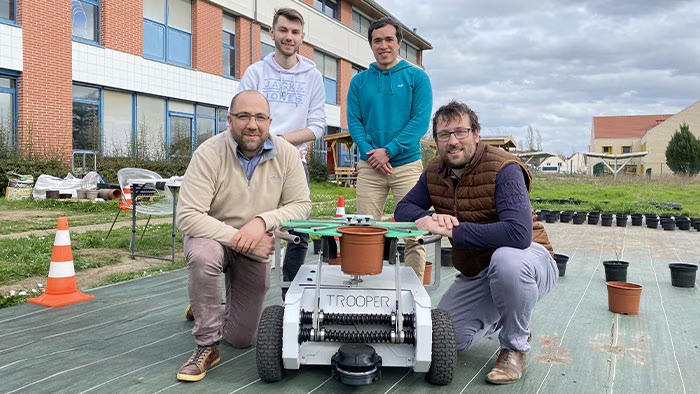