Safety components, relays, controllers, and how they all work together
Not your grandma’s machine setup!
Factory of the Future, Industry 4.0, Smart Factory…whatever you call the industrial operations of today, we can all probably agree on one thing: there are a lot of working parts. And if you have many a sensor that needs to communicate with a higher system controller, it’s easy for wires to get crossed—literally. That’s why it’s important to integrate a safe series connection.
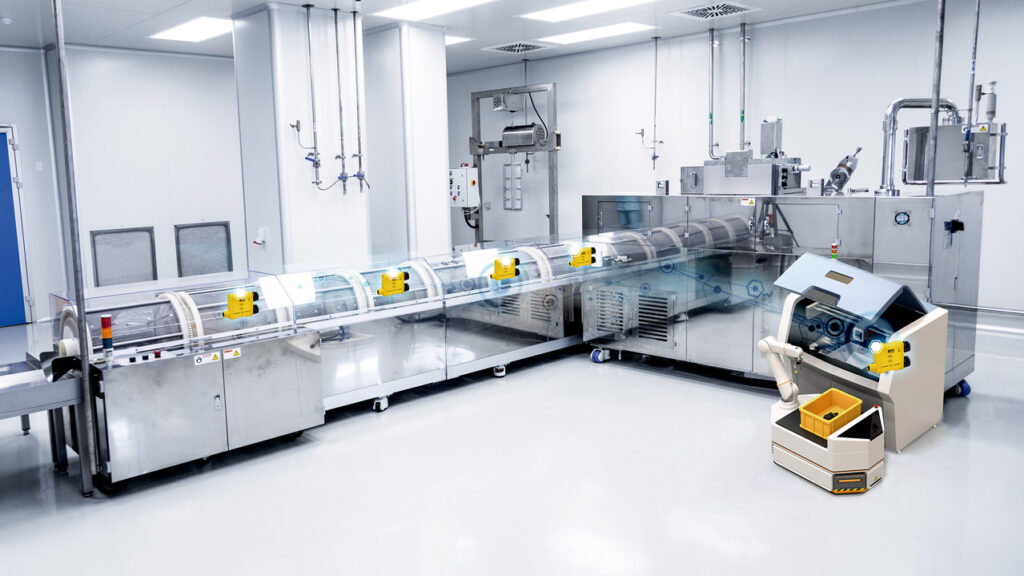
What is a safe series connection?
A safe series connection is a particular wiring method used to connect several safety devices. Within an industrial safety system, multiple safety sensors or switches can be connected in series, meaning that if any single component fails, the entire circuit is broken, immediately stopping the machine and preventing potential hazards. This design allows for enhanced safety by ensuring that all safety devices must be functioning properly for the machine to operate.
Another advantage of connecting safety devices in a series is that only a single pair of inputs on the controller or relay is required. This lowers the cost by not having to have multiple input modules or relays. It also saves cable and cable management. With a series, only one cable needs to run back to the control cabinet. With individual connections, a separate cable is needed for each sensor.
For example: If a machine has multiple safety guards, a safe series connection allows each to be connected with a single cable run. Without a safe series connection, each one is individually wired to either a safety relay or a safety controller. This not only increases setup time but can make the setup itself a little messy. You’d rather have one wire to deal with than several wires tangled up, right? With each guard connected in series with the others, if any guard is not properly closed, the circuit will be broken, preventing the machine from operating.
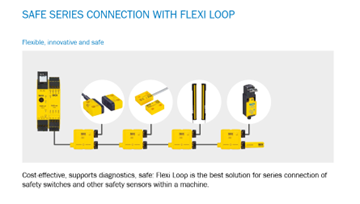
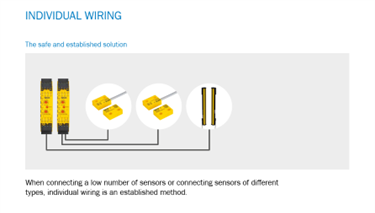
The end goal is to make the connection as seamless as possible from the safety components to the safety relay or the safety controller. As a result, you gain a high level of safety and protection against accidents.
All about Flexi Loop, the safe series connection from SICK
The Flexi Loop safe series connection allows you to connect up to 32 safety sensors up to PL e. It makes it easier to connect a variety of safety components, like safety locking devices, light curtains, and door switches, to a safety controller.
Integrating a safe series connection with a safety controller also ensures compliance with safety standards while optimizing performance. If your operation doesn’t meet the complexity that requires a safety controller, a safe series connection also works with a safety relay.
Flexi Loop benefits at-a-glance
- Reduced wiring and installation time: Faster and more cost-effective installations!
- Enhanced diagnostics: Identify and resolve issues faster
- Flexibility: Wire safety switches and sensors with OSSD outputs in the mix, regardless of manufacturer
- Cost: Cost savings from reduced wiring and fewer required safe inputs
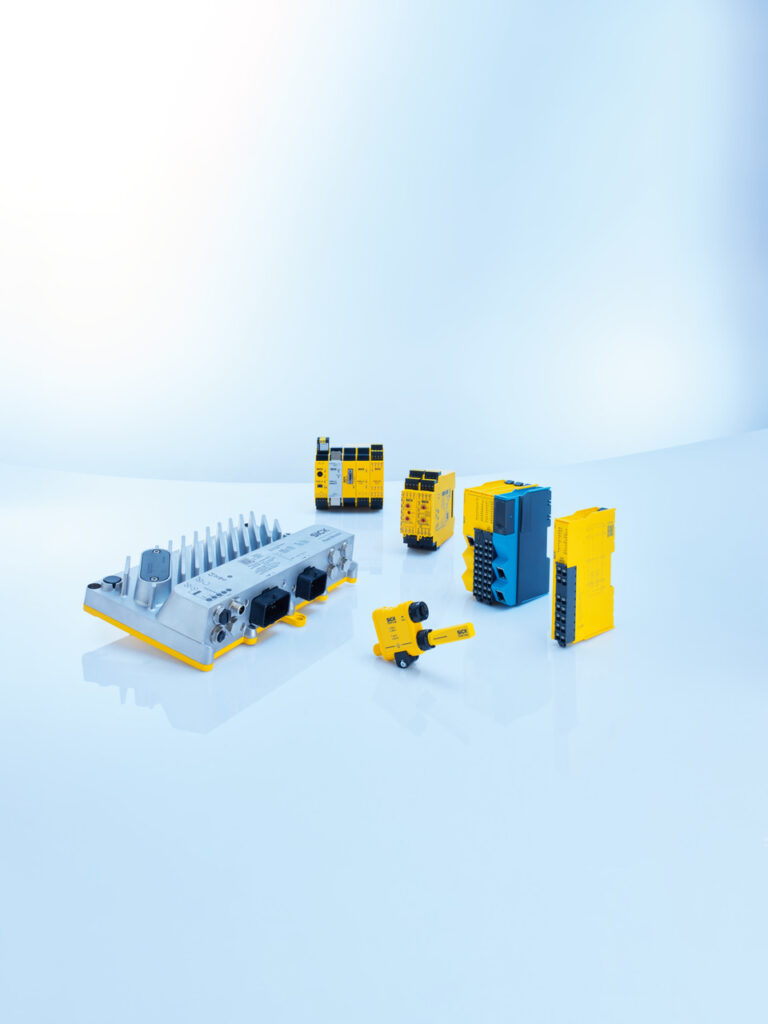
The whole is greater than the sum of its parts with Flexi Loop
Safety solutions from SICK allow you to work more efficiently. And the principle is simple: Combine a safety sensor with a Flexi Loop node up to 32 times. By connecting to a safety controller (like Flexi Soft), you create a series connection tailored to your requirements and the complexity of your machine system. In addition to the individual components, you receive the safe series connection as an additional benefit in this combination.
A bit about safety controllers: Flexi Soft
Flexi Soft is modular and intuitive. It can easily and freely be configured using our free software. Using a range of main modules, expansion modules, motion control modules and gateways, it is possible to create a customized solution for your safety application. And, together with Flexi Loop for the safe series connection of up to 32 switches and sensors, it is particularly suitable for protecting large machine systems.
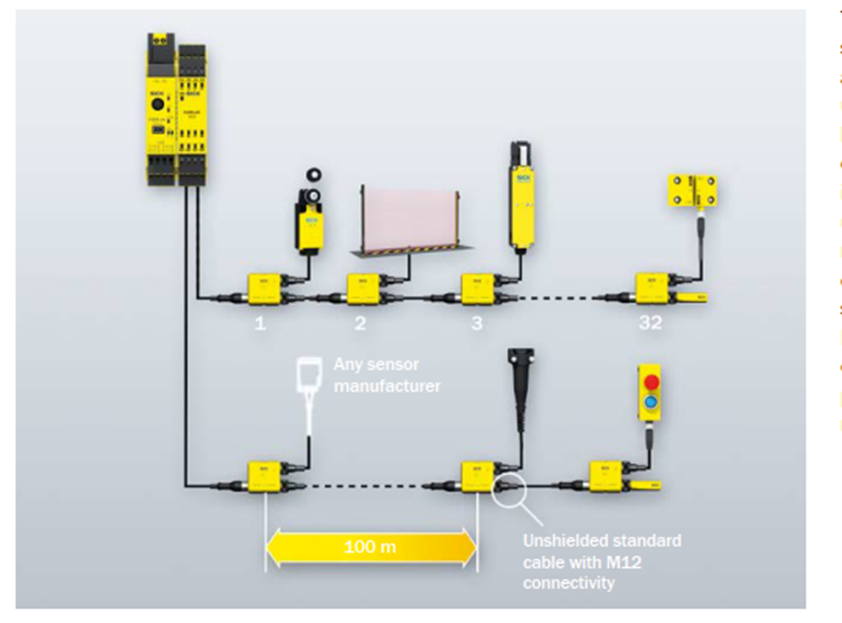
What about fault masking?
Fault masking, or hidden faults, is often a concern when integrating a safe series connection. This means a fault in the safety system is masked by another one, which makes the original fault difficult to detect. And if you haven’t detected the initial problem, this most likely means you will continue to run into safety issues on your machine. Which also means more downtime, and probably more money lost from maintenance and repair. But with the proper diagnostics…you can bid farewell to fault masking!
It's all in the detail(ed diagnostics)
The potential for fault masking is a significant flaw in a series connection, especially if you have limited diagnostic options.
But Flexi Loop puts an end to this by:
- Providing detailed information: which safety sensor has operated and why (normal operation vs. sensor fault)?
- Monitoring the entire safety cascade
- Processing all information once implemented into the software logic
- Transferring information: information can be transferred to gateways and is therefore available in all standard fieldbuses for integration into standard automation
- Reducing idle times through information visualization via man-machine interfaces
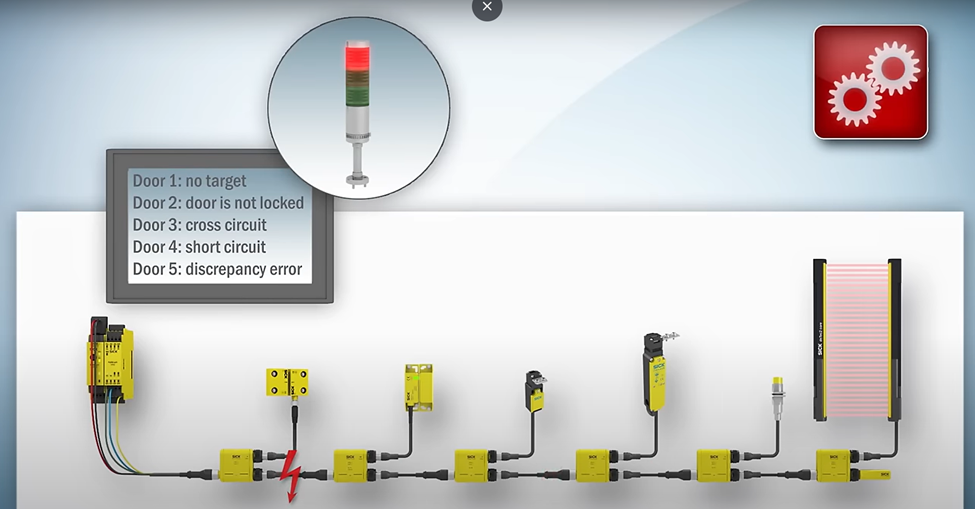
Flexi Loop allows the connection of different safety sensors in a series without a reduction in the performance level and offers detailed diagnostic information for each safety device. Flexi Loop monitors the wiring to each sensor and in between the Flexi Loop nodes and detects every possible fault instantaneously.
Have more questions about safe series connection?