Enhancing Efficiency and Safety with Autonomous Mobile Robots
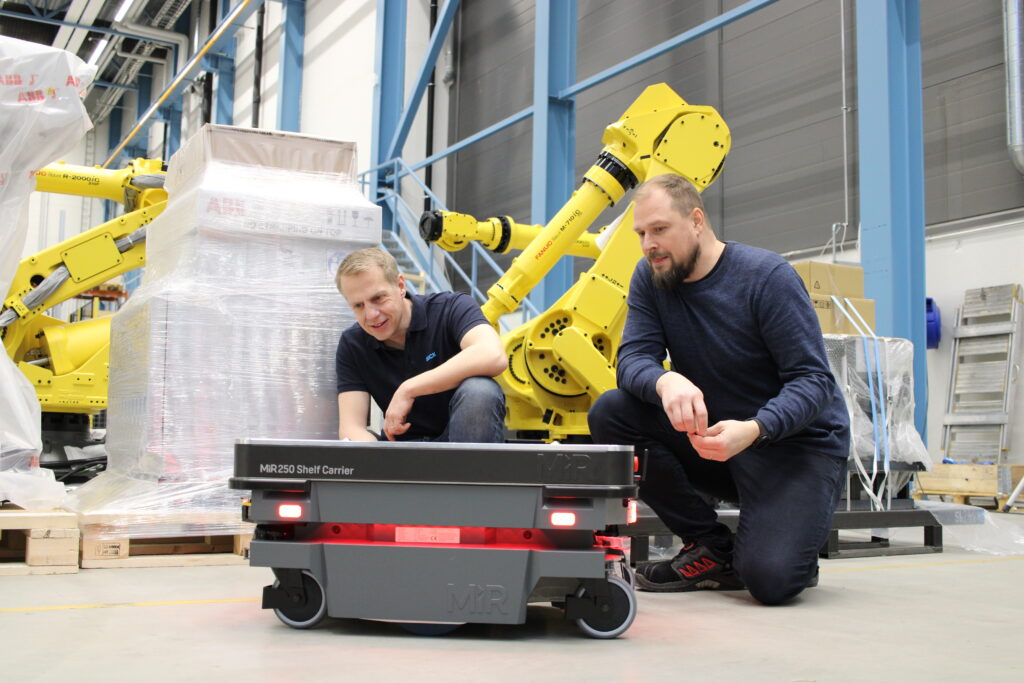
In the field of production and logistics, JTA Connection from Finland is a leading provider of tailored automation solutions. Their mobile robots are designed to handle tasks like transporting goods with a high degree of flexibility. These autonomous mobile robots (AMRs) use safety laser scanners to ensure the safety of people and to aid in their navigation and localization.
“Productivity, profitability, speed and safety are our mission,” said Juho Pulakka, Technical Director of JTA Connection Oy. “All of our solutions are based on the requirements of our customers.”
The company began its work in 1998 with “one man and one delivery van,” recounted the Chairman of the Executive Board Timo Ahonen. They began with installation work and monitoring of electrical systems. The company’s sales exceeded the €1 million threshold in 2006, and last year it was already €18 million with 110 employees.
The solutions from JTA Connection can roughly be divided into robotic and machine service cells, indoor logistics and material management solutions, and digital services. Its customers include the metal and machine construction industry, conveyor technology companies, breweries, and forestry.
“The collaboration with SICK has steadily grown and SICK is one of our most trusted suppliers. Our discussions are always frank, we can always trial solutions first, and SICK offers regular product and safety training sessions,” Ahonen said.
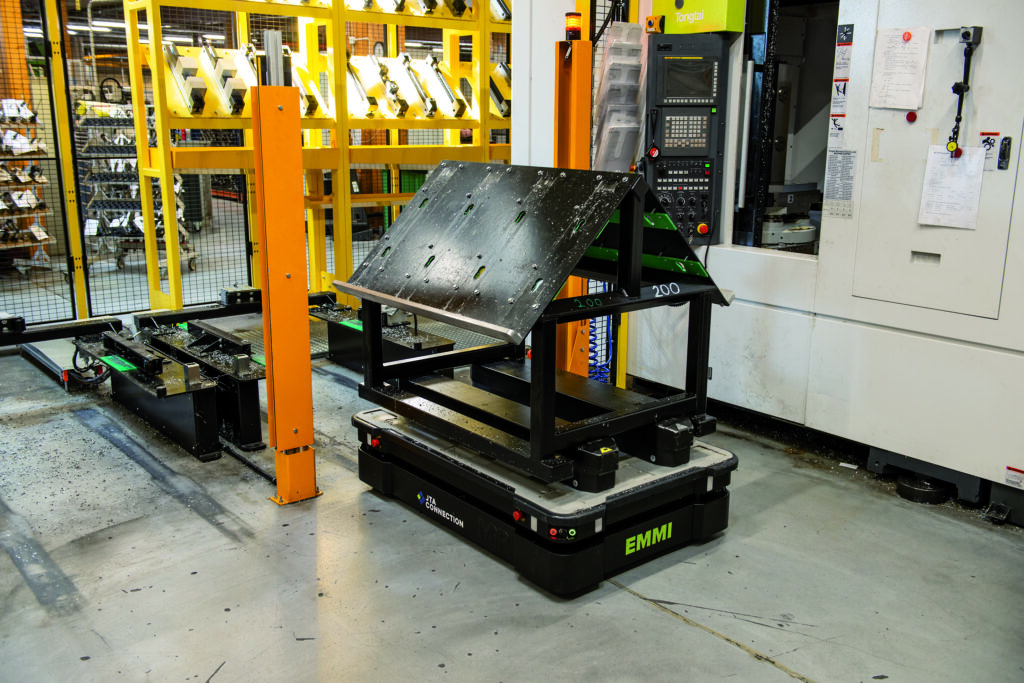
A versatile mobile robot for manufacturing
The mobile robot from JTA Connection comprises of a mobile platform and a structure of some level of complexity. In a simpler setting, this could be a hoisting device that lifts a pallet so that the mobile robot can transport it to another location. A more complex structure could be a robot on the platform.
Localization and navigation of the mobile robot occurs via the functionality of the safety laser scanner from SICK. With its help, a map of the working area of the mobile robot is created so that it can find its way around reliably during operation.
The mobile robot requires no pre-manufactured physical controller. A map is programmed in the device’s memory that allows it to continuously recognize its position in its environment and act accordingly.
With the help of the laser scanner, the mobile robot precisely detects walls or obstacles in its environment. The AMR acts autonomously in its operation by selecting the most economical route from one destination to another and looking out for obstacles and people in its environment. When it encounters an obstacle, it goes around it and, if necessary, selects an alternate route.
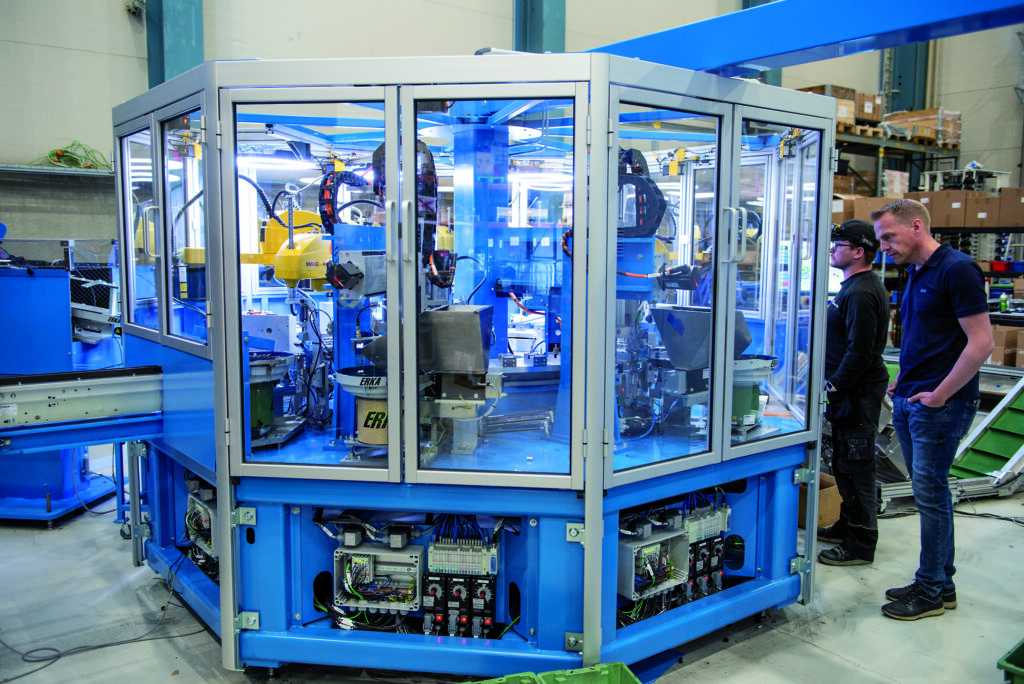
JTA Connection has the right size and flexibility
“Our strength is that we focus fully on the requirements of our customers,” said Janne Seikola, Sales Manager at JTA Connection. “Our in-house manufacturing facility ensures a high level of flexibility in the implementation and delivery time. Furthermore, we are also large enough that our larger customers can feel confident in using our services.”
What distinguishes JTA Connection from its competitors, according to Seikola, is that the company not only delivers a robot cell but also offers further advantages for the customer. From application development, production management, design, and manufacturing right to installation, commissioning, and maintenance.
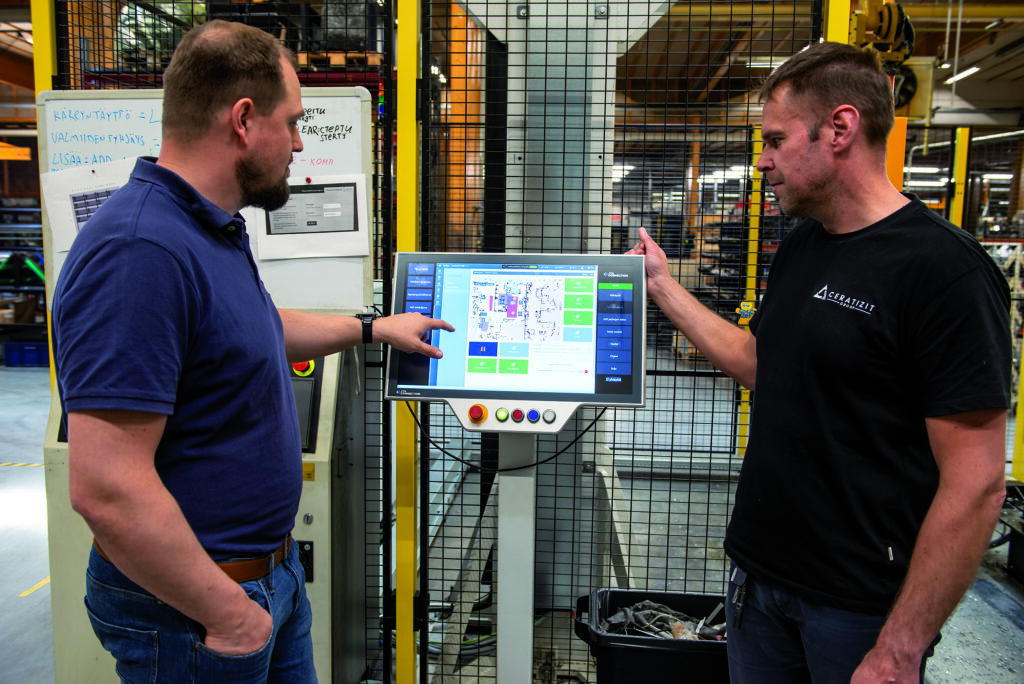
Mobile robots in use at family business
A longstanding customer of JTA Connection is the family business ST-Koneistus Oy, which is one of the leading suppliers of hydraulic blocks and components in Europe.
“Our product portfolio is very broad and we have customers from machine builders to windmill builders,” said Hannu Tapio from ST-Koneistus.
The proprietor Tommi Peltonen already had the idea some time ago to automate the internal logistics using a mobile robot.
“That was new at the time, but fit perfectly into our concept,” Tapio said. “The warehouse does not need to be located right next to the machine tool, but can be positioned elsewhere depending on the situation.”
The autonomous mobile robot is a great help to Tapio and his team and relieves people in other areas. The dynamic environment and limited space are a challenge for the system, but it has been operating well under the difficult conditions. In future, the mobile robots will not only be used to move parts, but also to exchange dies in the machine tools.