Precise excavator bucket movements with absolute encoder solution for tilt rotators
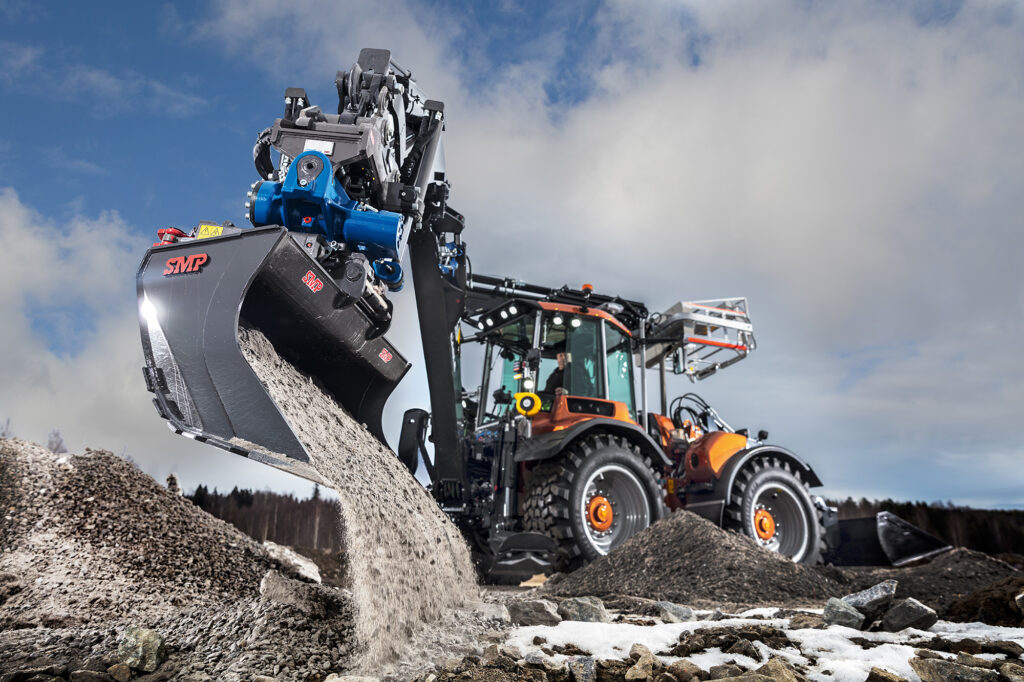
Tilt rotators significantly enhance the precision of excavation tasks. To measure and guide the intricate movements enabled by this equipment, SMP turned to AHM36 CANopen absolute encoders from SICK.
A tilt rotator, positioned between an excavator’s boom and bucket, allows for complex movements, enabling the operator to rotate the bucket and adjust its incline. This capability supports precise trenching and slope pulling, reducing the need to frequently reposition the vehicle. Encoders measure the bucket’s rotary position relative to the boom, ensuring accuracy.
Identifying an Industry Need
SMP, with its background in excavator bucket production, identified a market need for tilt rotators. The specific configuration and placement required a highly customized product from SICK, capable of operating in harsh environments. SMP needed a compact, reliable encoder that could fit in a small space and connect to a worm gear inside the tilt rotator. The encoder also had to withstand high shock and vibration levels, temperatures as low as -40°C, and function within a grease-filled casing, necessitating its own protective housing.
The AHM36 CANopen absolute encoder was selected for its high performance, durability, and compact size. At just 36 mm, it offers a space-saving, cost-effective design and is easy to install with its rotatable male connector. Its stainless-steel design and IP69K enclosure rating (Inox versions) make it resilient to environmental influences, while its robust magnetic sensor system ensures reliability in harsh conditions.
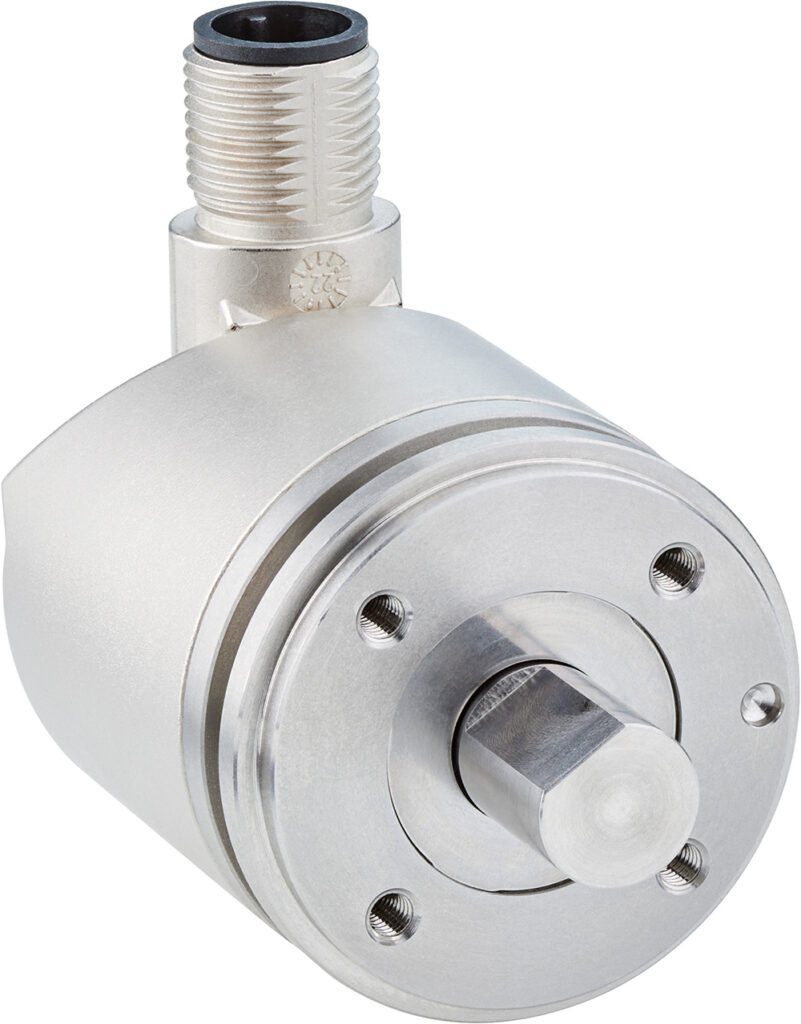
Innovation Through Collaboration
The unique application initially presented challenges, but continuous communication between SMP and SICK led to improvements. This is a unique type of installation of SICK encoders on tilt rotators, and the solution has evolved over time.
Early iterations of the encoders allowed some grease to bypass the protective layer, prompting SICK to quickly refine the design.
Engineers from SICK visited the site in October 2023, and new prototypes were tested the following month. Series delivery of the finalized product began in early 2024.
Rather than creating an entirely new product, the team adapted the current setup using existing hardware – a hybrid between IP69K and IP67. The housing located at the front of the worm gear where the flange and shaft connect needed the level of protection offered by the IP69K. Otherwise, the shape of the IP67 version with the necessary rotatable M12 connector was used. This means that the part has room to turn without crowding the other parts.
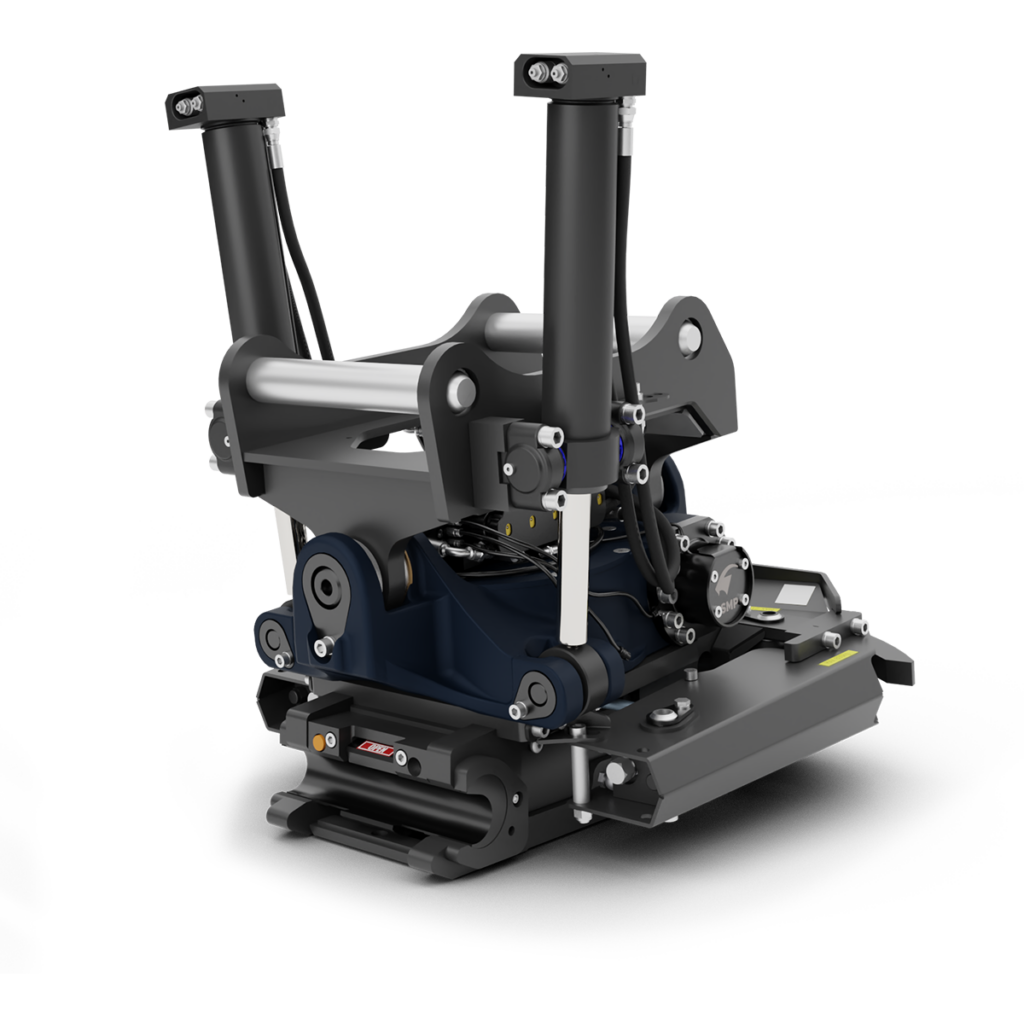
Expanding Potential
The collaboration between SICK and SMP facilitated quick resolution of challenges. The CANopen interface of the absolute encoders benefits excavator operators by providing immediate on-screen feedback in the cabin, enabling precise digging.
This successful application opens new possibilities for SICK’s absolute encoders in mobile outdoor automation, and the partnership between SICK and SMP is set to deepen further.