How intelligent integration increases efficiency and flexibility with the new IO-Link Master, SIG300
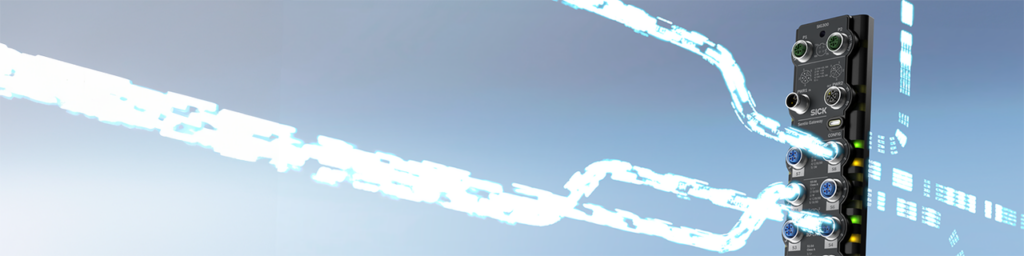
Companies are looking for ways to make processes more efficient. Some are designing more modular machines and reducing maintenance costs. The intelligent use of sensor and process data plays a key role here.
An IO-Link master enables seamless acquisition, analysis and integration of this data and therefore makes a decisive contribution to implementing sustainable automation solutions more quickly, easily and cost-effectively. In this blog, you will find out more about the added value of a seamless data integration with the new SIG300 IO-Link Master.
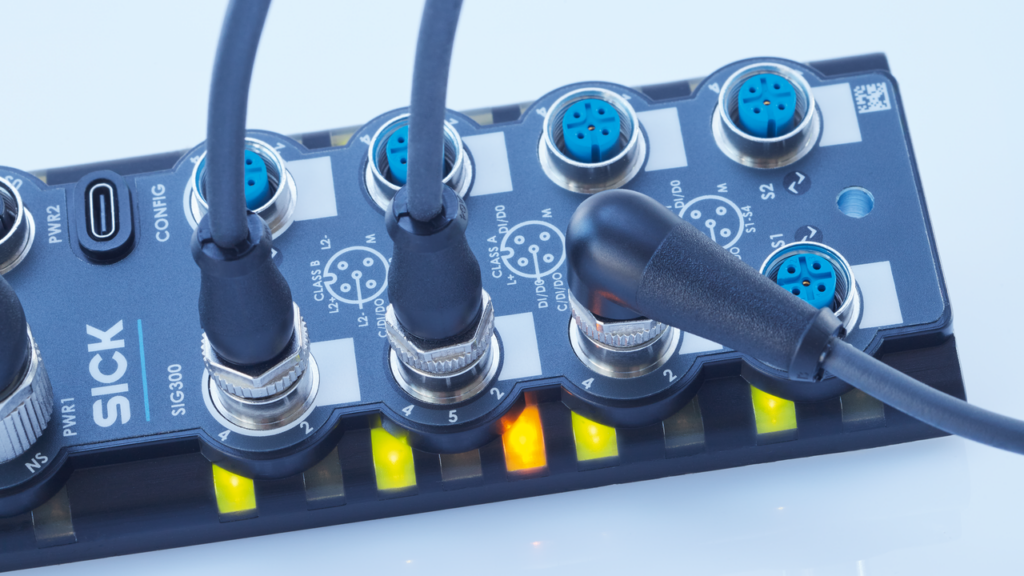
Transparency and strategic decision-making
Data-based automation and the networking of IT and cloud systems are crucial for efficiently controlling production and logistics processes. SIG300 acquires sensor data and delivers meaningful KPIs such as throughput, capacity utilization and downtimes. This enables precise analysis of overall equipment effectiveness (OEE).
Transparent and comprehensive data enable real-time monitoring of production processes and material flows. Intuitive dashboards provide a sound decision-making basis to increase efficiency and reduce costs in the long term. This allows processes to be continuously optimized and resources to be deployed in a targeted manner.
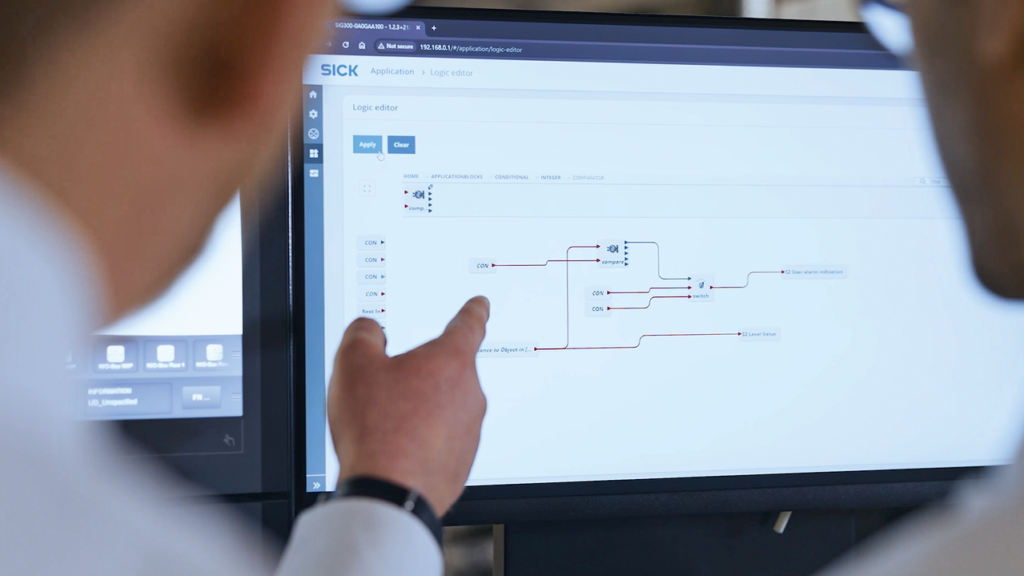
Modularity and future-proof design in machine construction
Modern automation combines robotics, sensor technology, machine learning, artificial intelligence and traditional control systems to increase productivity and conserve resources. These technologies must harmonize to be flexible and adaptable. Only in this way can they keep pace with smaller batch sizes, rapidly changing production requirements and individual customer requirements. This adaptability often requires the development of complex algorithms and control systems based on real-time data. One challenge here is to seamlessly integrate sensor and actuator technologies to cope with the increasing complexity of automation.
The SIG300 serves as a decentralized interface for intelligent data integration. The IO-Link Master shifts control tasks to the periphery thereby freeing up the central controller. This leads to an improved load distribution and enables the machines to react more quickly. Bidirectional communication between sensors, actuators and the controller enable continuous data traffic, facilitates integration and optimizes device management. As a result, machines can be adapted and converted more quickly.
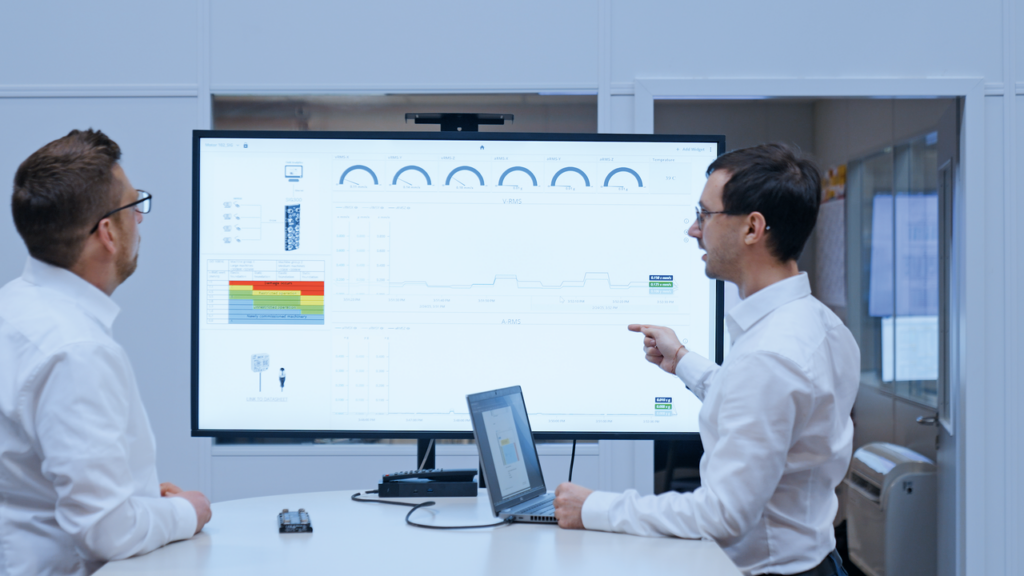
Needs-based diagnostics and maintenance options
Unexpected machine downtimes and high maintenance costs often result from insufficient process and condition data. Traditional systems only provide limited information and, consequently, maintenance is either performed too late or even unnecessarily.
With the SIG300, extended diagnostics of the connected devices are performed remotely and wear and tear, contamination and deviations are detected at an early stage. This enables needs-based and cost-effective maintenance. Critical changes can be visualized in real time via several channels: A connected signal light informs employees immediately while the data is sent to IT monitoring systems in parallel. Furthermore, the bi-directional communication with the connected devices enables efficient remote maintenance – for higher machine availability and lower costs.
Investment in the future
The SIG300 IO-Link Master from SICK is more than just an interface – it seamlessly acquires, manages and integrates process and device data. As a powerful all-rounder, it supports precise analyses and optimizations in IIoT applications and enables easy integration into existing automation systems through decentralized data processing. With its rugged design and ability to provide diagnostic data, the SIG300 opens new possibilities for networking at field level and connection to IT and cloud environments. Find out more about the versatility of this intelligent IO-Link Master.