Power, mobility, and safety for the construction industry with Baubot, KUKA, and SICK
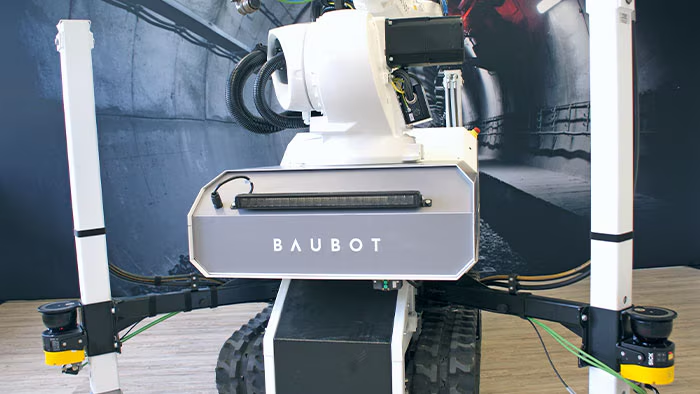
The Austrian start-up Baubot is revolutionizing the construction sector with its cutting-edge automation solutions, pushing innovation to new heights. Their robotic marvels, like the tunnel construction robot, are setting new standards. Meanwhile, SICK’s advanced sensor technologies ensure the safety of both people and machines.
While robots have long taken over strenuous manual tasks in industrial settings, construction has lagged behind. This gap in automation in other industries and construction is stark. Even small industrial enterprises often embrace comprehensive automation, whereas construction remains more traditional.
The collaborative robots thriving in industry aren’t designed for the rugged demands of construction, where power and mobility are crucial. However, implementing the necessary safety measures in construction can be challenging, sometimes becoming a hindrance.
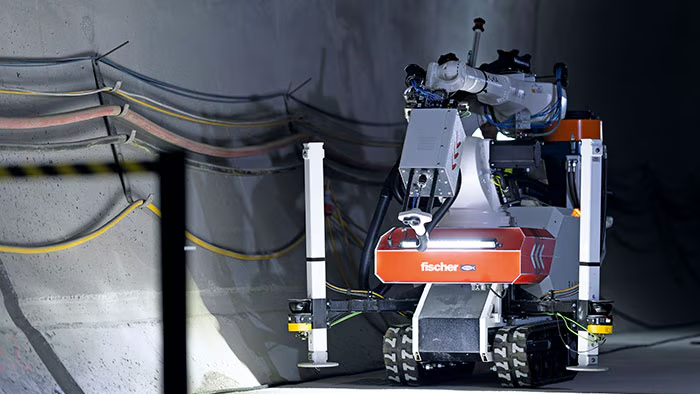
Creating Versatile Robots
Baubot excels in developing comprehensive automation solutions tailored for the construction industry, integrating KUKA robots and SICK sensor technology. Their “Baubots” (construction bots) are equipped with advanced safety features, including state-of-the-art sensors and collision detection systems.
These innovations ensure safe operation even in dynamic environments, allowing humans to work seamlessly alongside mobile robots without compromising on reliability or safety.
Victor Rodionov, COO of Baubot, discussed the pivotal role of their new construction robots and the company’s three core areas of focus.
“Our first priority is developing and constructing bespoke robotic systems tailored to our clients’ needs, utilizing our two flagship models: the MRS5 and MRS12. The MRS5, being more compact with a shorter arm and lower payload capacity, complements the larger MRS12,” Rodionov said. “These ‘mechatronic colleagues’ are versatile, handling a wide array of tasks on construction sites, from drilling, grinding, polishing, welding, and spraying.”
One of the primary tasks for the MRS12 Baubot is drilling holes. Thanks to its advanced programming, the robot requires no training or manual guidance—it instinctively knows where to position itself for each drill. This results in swift and precise work, eliminating any need for improvisation.
Construction and drilling proceed exactly as planned, with every step meticulously documented by the system. This thorough logging makes additional inspections or other on-site logging mechanisms unnecessary.
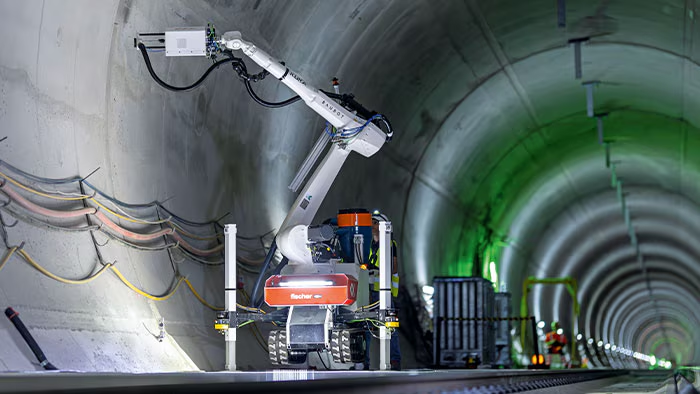
Intelligent Software and Control Systems
The second core focus of Baubot is crafting the software and control systems that empower their robots to autonomously execute specific tasks.
“Take drilling, for instance. While the robot arm is equipped with an end effector, that’s just the beginning. Robust software solutions are essential to drive these operations,” Rodionov said. “Additionally, we incorporate technical features like dust control systems, ensuring dust is extracted directly at the drill hole for a cleaner, safer work environment.”
Providing a Complete Solution
The third area at Baubot is the application software that includes all processes as a complete solution. The Baubot Planning and Simulation Environment (PSE), for example, supports quick graphical planning of the mission positions and driving paths for the mobile robotic system in a virtual environment.
The software imports BIM files, Point Clouds, 3D CAD files as well as 2D drawings of the construction layouts directly into the 3D environment. Baubot PSE also features a built-in post-processor that converts virtual simulations into mission programs tailored specifically to the requirements on site.
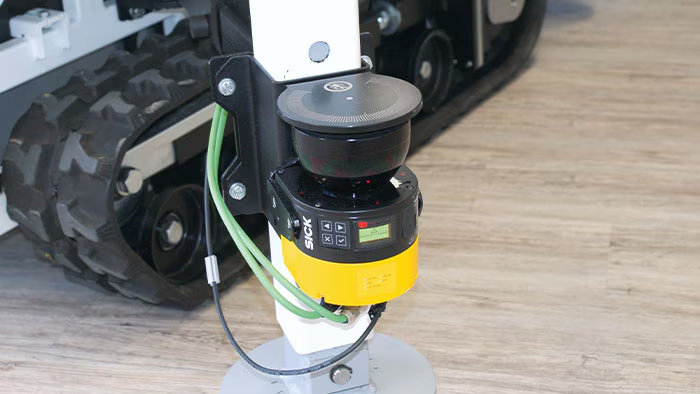
More Safety in Construction
Construction sites have long been hazardous environments. With Baubot, safety becomes more simple on construction sites.
“Over the past 50 years, not much has changed in construction processes. The same tools and planning methods from half a century ago are still in use today,” Rodionov said. “This stagnation is evident in the alarming risk statistics, which show that every employee experiences an accident every four days on average. This is astonishing, even if many incidents are minor.”
The introduction of robots with specialized safety features can significantly improve this situation. Unfortunately, adequate protection is often lacking during manual tasks, and over time, people tend to become overconfident and careless. Rodionov highlights that deploying Baubots dramatically enhances the safety level on construction sites.
“The safety consulting services from SICK experts raised many insightful questions and issues, which we incorporated into the machine’s development,” Rodionov said.
This collaboration led to the creation of a controller with an integrated safety CPU that oversees all Baubot operations. The result is a fully integrated robotic system for construction, with safety built-in from the ground up!
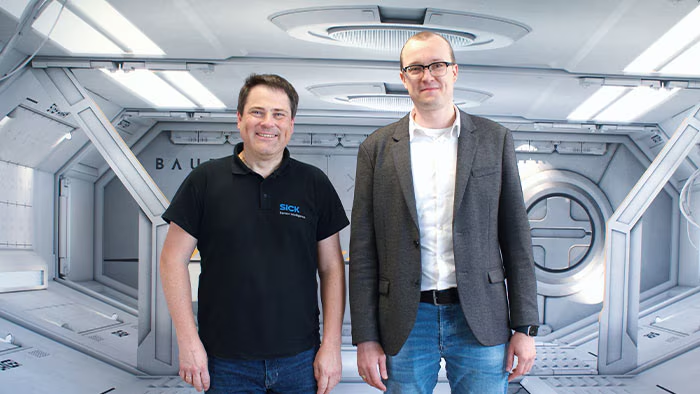
Automation, Not Autonomy
A prime example of the MRS12 Baubot’s capabilities is its role in tunnel construction, specifically installing railings. Take the Koralm Tunnel, for instance, which requires 30 kilometers of railings in each direction, with up to four holes drilled every half meter for brackets.
“We’re not talking about a machine making autonomous decisions,” Rodionov said. “Our focus is on automation within regulatory limits, meaning an operator must be present. However, this operator no longer needs to endure the arduous task of drilling for eight hours straight. The Baubot handles the heavy drilling, while workers manage the installation.”
Initially met with skepticism, these robots are now embraced by construction workers, who see them as valuable tools rather than competitors.
Ensuring safety, SICK has been a crucial partner from the start, leveraging its extensive expertise in machine safety and robotics.
“Our experts collaborated with Baubot’s developers to identify all potential hazards,” said Ingo Wegscheider, Regional Sales Manager at SICK Austria. “We also considered the challenging tunnel conditions—dusty, moist, and dirty.”
Safety risks, such as the robot’s mobility, are mitigated using microScan3 safety laser scanners, which detect obstacles or fallen workers. With two scanners covering a 270-degree range each, the entire surroundings are monitored for safety.