Manufacturers need encoders, but they don’t really want to think about them
Encoders are arguably one of the most necessary sensors in manufacturing, but many aren’t sure what to consider when installing them.
Encoders are sensors that translate motion into an electrical signal that can be interpreted by a control device. They provide data about position, angle, and rotation counts. This data can be used to determine speed and position, making encoders the perfect solution for accurate position detection in industrial automation.
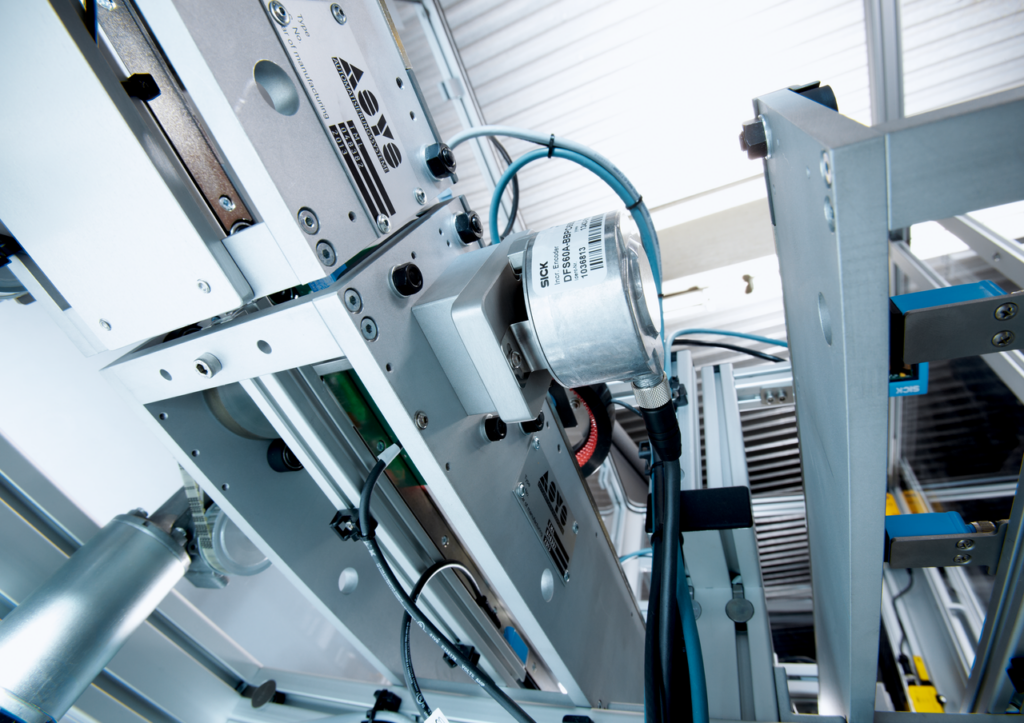
Encoders use different types of technologies to create a signal, including mechanical, magnetic, resistive, and optical. For example, in optical sensing, the encoder provides feedback based on the interruption of light.
There are two main types of encoders — absolute and incremental — each providing different kinds of information. Absolute encoders provide a unique position signal that describes the specific location of a system within its range of motion, while incremental encoders produce a pulsed signal as their position changes, providing fast and precise feedback.
If you’re looking for an encoder where you don’t have to think about it after you buy it, SICK has the answer for you. There are several encoder options out there, but lately, there has been buzz about some HS35 and HS25 class encoders having very long lead times and even some production issues. With SICK’s DGS80, we can solve that problem for you and give you a much shorter lead time – even as short as one week, depending on what you need!
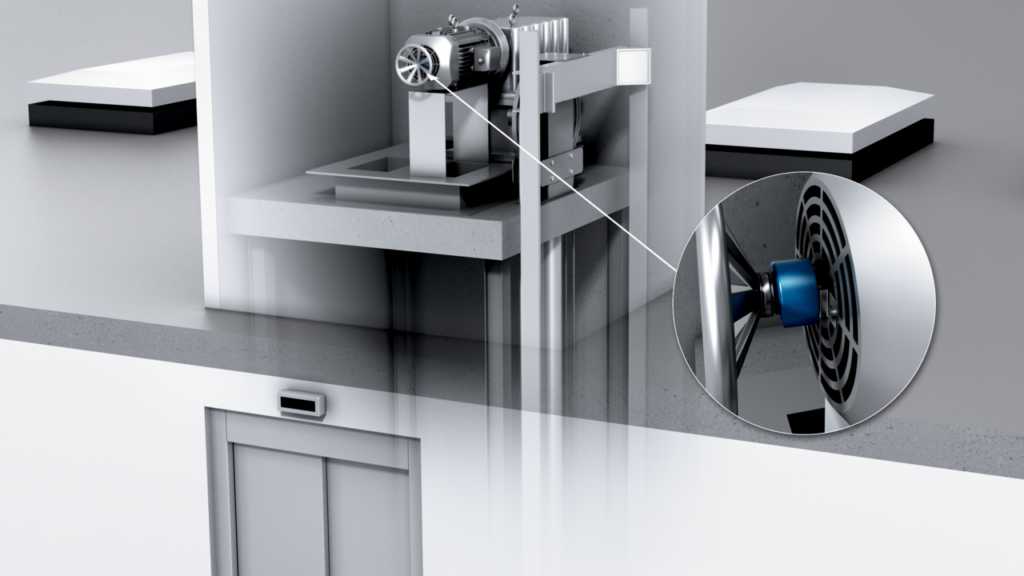
All About Hollow Shaft Encoders
A hollow shaft incremental encoder is a type of rotary encoder that provides velocity feedback and is typically used in positioning and motor speed feedback applications. These are often referred to as HS35 class and HS25 class encoders.
Hollow shaft encoders are often utilized because they are more compact than solid shaft encoders, making them ideal for applications where space is limited. These encoders can be directly mounted to a motor shaft and affixed using a flexible tether or torque arm to prevent the encoder from rotating. This makes the installation, positioning, and alignment easier.
Hollow shaft encoders can be used in a variety of industries, including manufacturing, automotive, and robotics. They are commonly used in applications where a solid shaft encoder is not practical, such as in large rotating machinery or when a shaft must pass through the encoder.
Hollow shaft encoders are more forgiving in terms of shaft sizing, especially in length. They can be mounted onto a wide range of shaft sizes. The hollow shaft insulation acts as a galvanic separator and thermal decoupler. It reliably eliminates shaft currents, bearing corrosion, and wear while keeping down encoder temperature.
Hollow shaft encoders offer moderate resistance against shock and vibration. This is particularly beneficial in industrial environments where machinery often experiences significant amounts of physical stress.
Without the need for an extra coupling, hollow shaft encoders have a smaller installation profile. This can be advantageous in applications where space is limited. Hollow shaft encoders provide a strong foundation for speed and RPM feedback. This is crucial in many applications where precise speed control and feedback are required.
Get Your Encoder – FAST!
SICK’s DFS20/DFS25 and DGS80 encoders are built or stocked in Minneapolis, Minnesota. That means you don’t have to wait weeks – or even sometimes months – to get your encoder. Our incremental encoders can ship from our factory so you can receive what you need in a matter of days, not weeks.
DFS20 / DFS25: Made in the USA for High Performance and Reliability
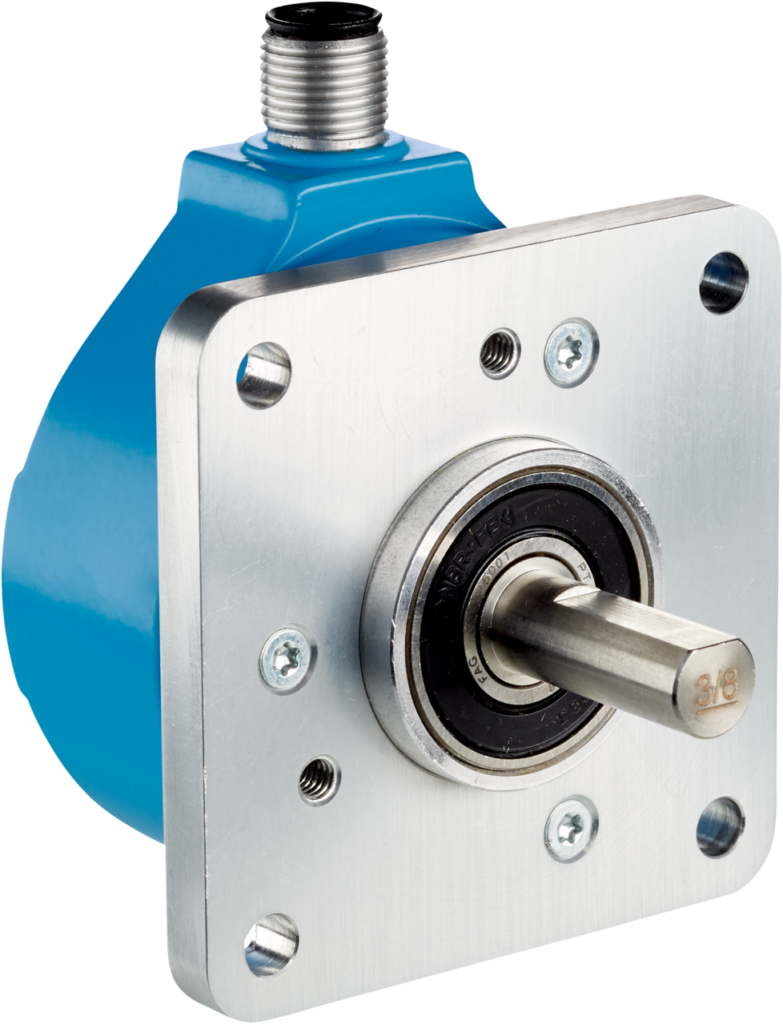
- High Resolution: more precise positioning for applications that require high accuracy.
- Reduced Costs: Spare parts inventory requirements are reduced because a single programmable DFS2x encoder can be used across a variety of applications.
- Reduced Machine Downtime: Wide operating temperature range and high tolerance of shock and vibration reduce machine downtime.
DGS80: The new generation of Large Bore Encoders in the HS35 class
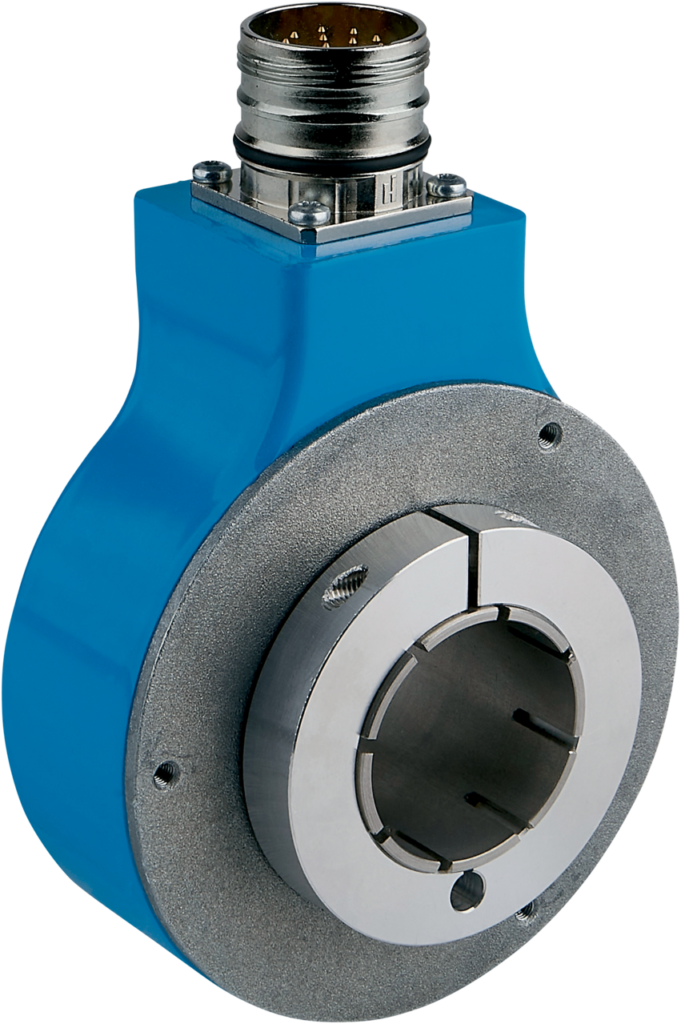
- Easy Installation: Universal tethers and reliable clamping ring help to reduce set-up time.
- Simplicity: Large bore eliminates the need for special couplings and allows simple integration into numerous applications.
- Space Saving: Compact design allows for seamless integration in designs where space is limited.
- High Resolution: Gain high resolution of up to 8,192 pulses per revolution, capable of measuring speeds up to 3,600 revolutions per minute.
The DGS80 at Work
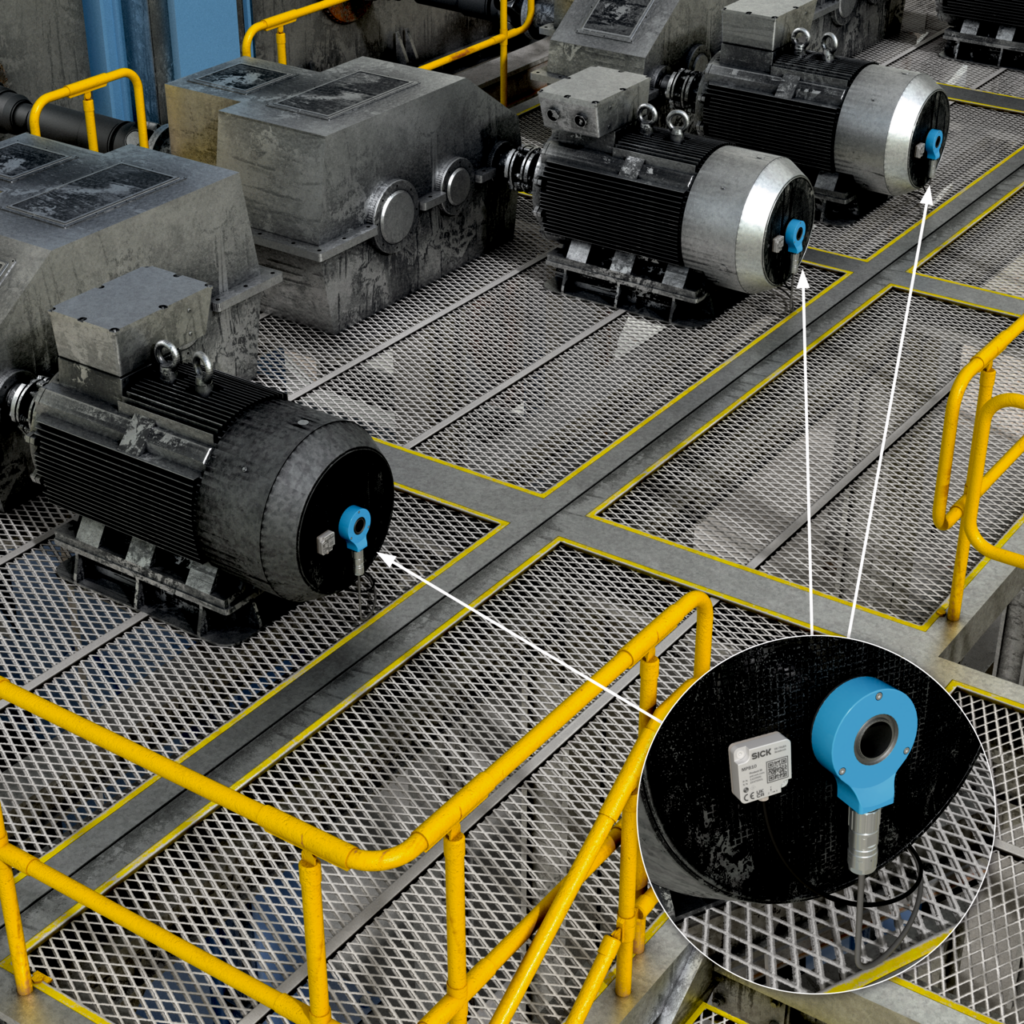
But perhaps you’re curious how the SICK DGS80 encoder can impact day-to-day work in industrial applications? It is effectively used in various industrial applications to improve efficiency and precision, making a significant difference in various industrial automation applications.
The large resolution range means the encoder is well-suited for many different industrial applications such as printing, scanning and elevator speed control. Industrial applications such as speed measurement of AC motors, printing, scanning.
For example, the DGS80 encoder is used to detect the position of overhead traveling crane gears. This helps in precise positioning and movement of the crane, improving safety and efficiency.
If you’re looking to control speed on conveyors, the DGS80 encoder can be used to calculate belt speed and running direction. This helps in maintaining the correct speed and direction of the conveyor belt, ensuring the smooth flow of materials.
Looking to get your encoder quickly? Contact a SICK representative today!