Boosting Efficiency and Quality in EV Battery Production with Advanced Sensor Technology
Electric vehicle (EV) battery traceability is crucial for ensuring quality, safety, and scalability in production. SICK sensors play a pivotal role in this process by providing high-precision inspection and monitoring solutions.
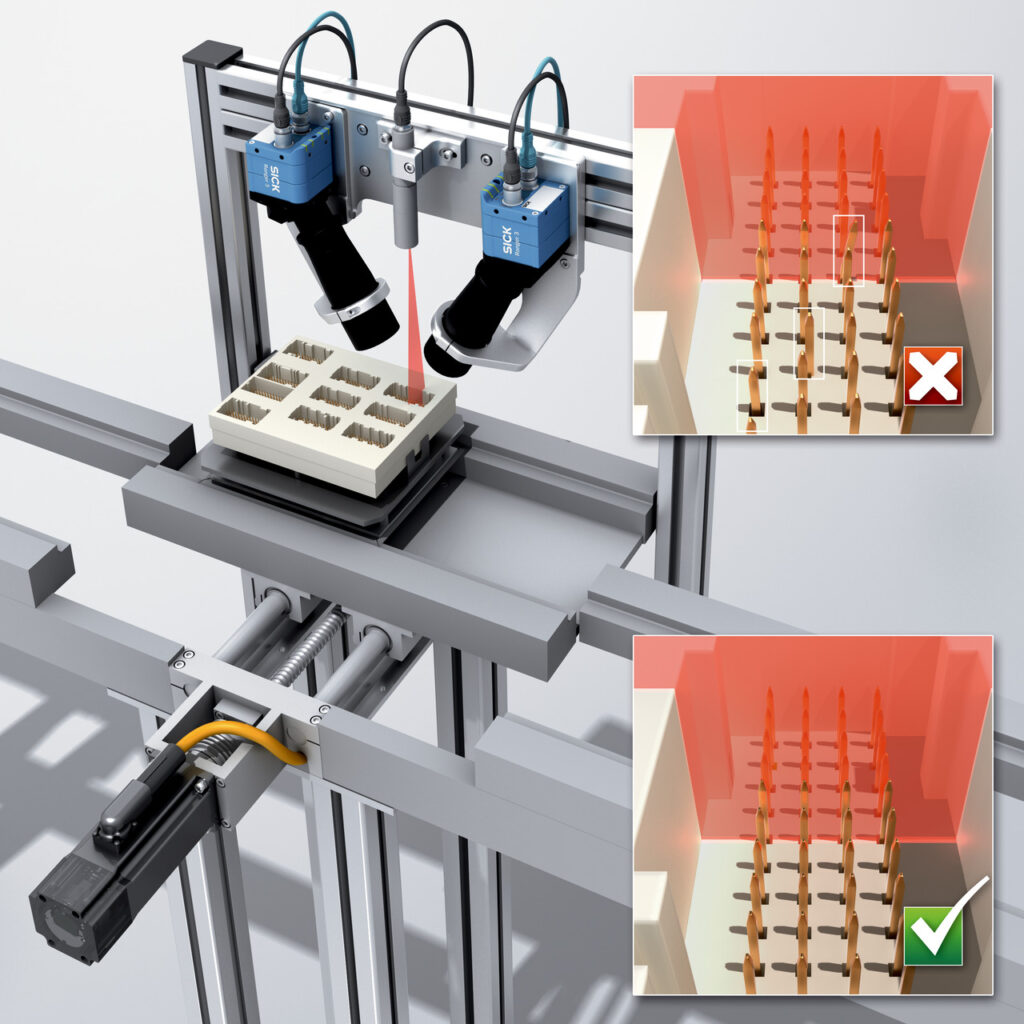
High-Precision Inspection
SICK's advanced vision systems, like the Ranger3 cameras, use high-definition imaging and laser triangulation to inspect EV batteries with exceptional accuracy. They can detect even the smallest defects or foreign objects, ensuring battery integrity. The high-resolution imaging captures minute details, crucial for identifying tiny, potentially compromising defects.
SICK's programmable Sensor Integration Devices process data in real-time, allowing for immediate defect detection and correction. These complete inspection systems, including cameras, lasers, and software, integrate seamlessly into production lines. They are particularly effective at detecting foreign objects, even those matching the battery's color, preventing assembly damage, and ensuring battery longevity and safety.
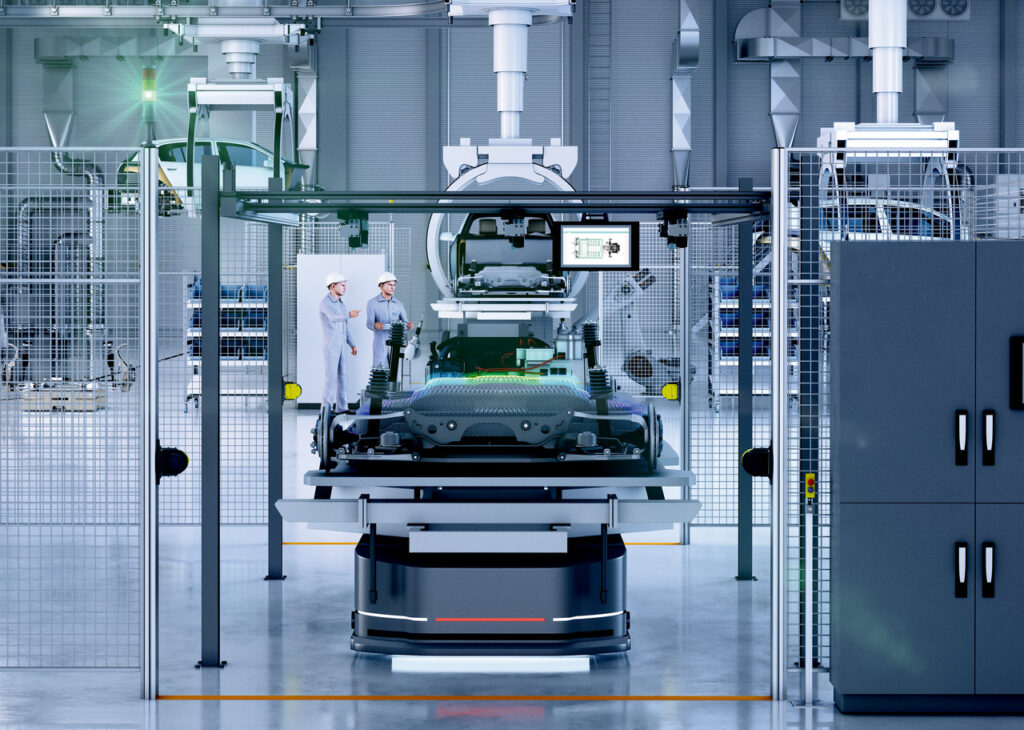
Foreign Object Detection
The Foreign Object Detection System from SICK is a quality control solution that uses 3D cameras and laser triangulation to detect even the smallest foreign objects on various surfaces, including high-voltage batteries. It ensures consistent inspection quality across different materials and conditions, making it suitable for both small and large-scale manufacturing.
The system generates real-time 3D profiles of surfaces, allowing for immediate detection and action. It can also be customized to detect specific types of foreign objects, such as missing screws or issues with adhesive and sealant beads. These features help manufacturers maintain high standards of quality and safety.
By leveraging these advanced technologies, SICK sensors help manufacturers maintain high standards of quality and safety in EV battery production, ultimately supporting the reliability and efficiency of electric vehicles.
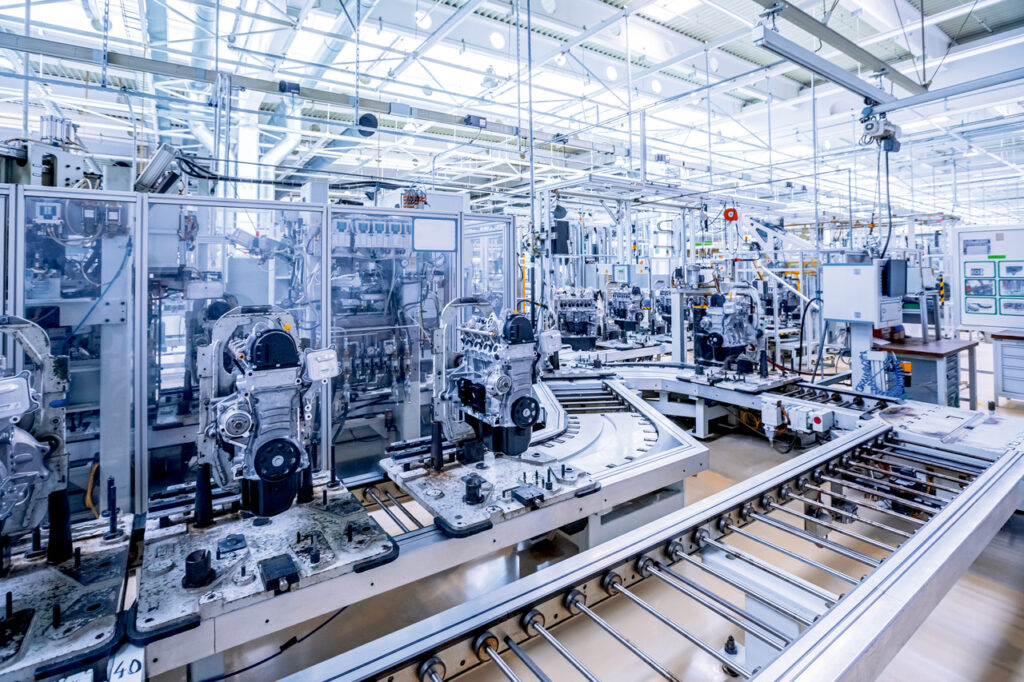
Real-Time Monitoring
SICK sensors enable real-time monitoring of the battery assembly process by continuously tracking and recording data on each battery's condition and production stage. The Multi Physics Box collects data on parameters like vibrations, shocks, and temperature, helping identify potential faults early. This data is processed in real-time using advanced software, allowing for quick detection and response to anomalies.
SICK's Monitoring Box visualizes status data through a comprehensive dashboard, ensuring secure data transmission and long-term storage. The system can send customizable alerts when thresholds are exceeded, notifying relevant personnel immediately. Additionally, historical data analysis supports predictive maintenance, reducing unplanned service interventions and costs. These features enhance the reliability and efficiency of manufacturing processes.
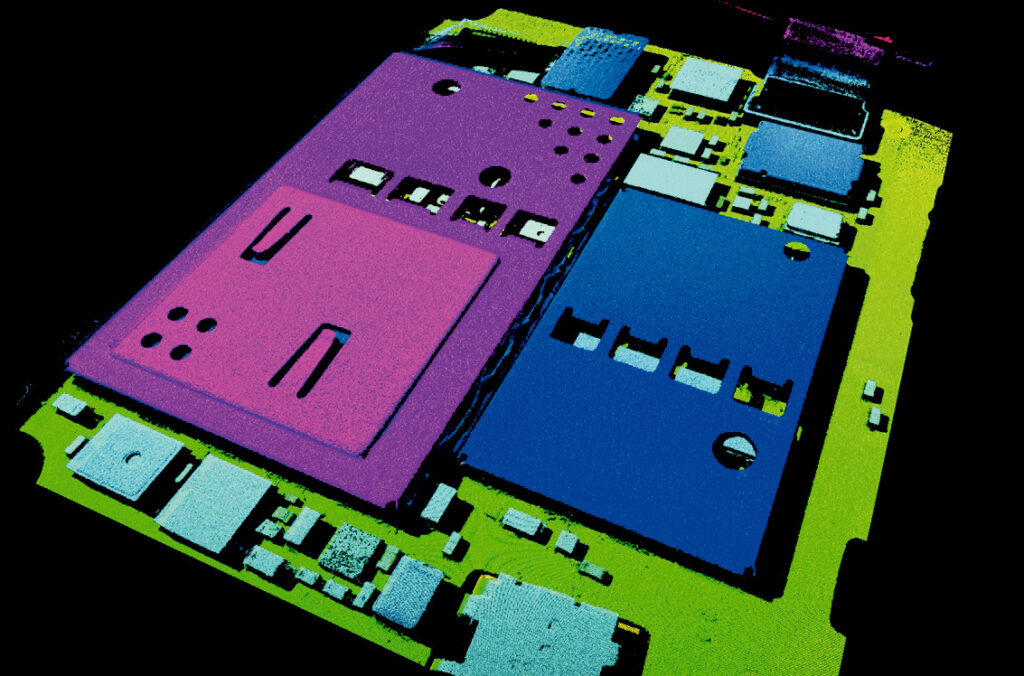
Comprehensive Traceability
With SICK's sensor technology, every battery can be traced back to its origin, including details about its components and manufacturing process. This comprehensive traceability ensures that any issues can be quickly identified and addressed, minimizing the risk of recalls and enhancing overall production efficiency.
By tracking each battery through its production stages, manufacturers can ensure that all components meet quality standards. This helps in identifying and addressing defects early in the production process.
Traceability allows for the monitoring of battery performance and safety throughout its lifecycle. This is crucial for preventing potential failures and ensuring the safety of the end-users. Many regions have strict regulations regarding the production and disposal of batteries. Traceability helps manufacturers comply with these regulations by providing detailed records of each battery's lifecycle.
Traceability supports recycling and proper disposal of batteries by providing detailed information about their composition and usage history. This contributes to more sustainable manufacturing practices.
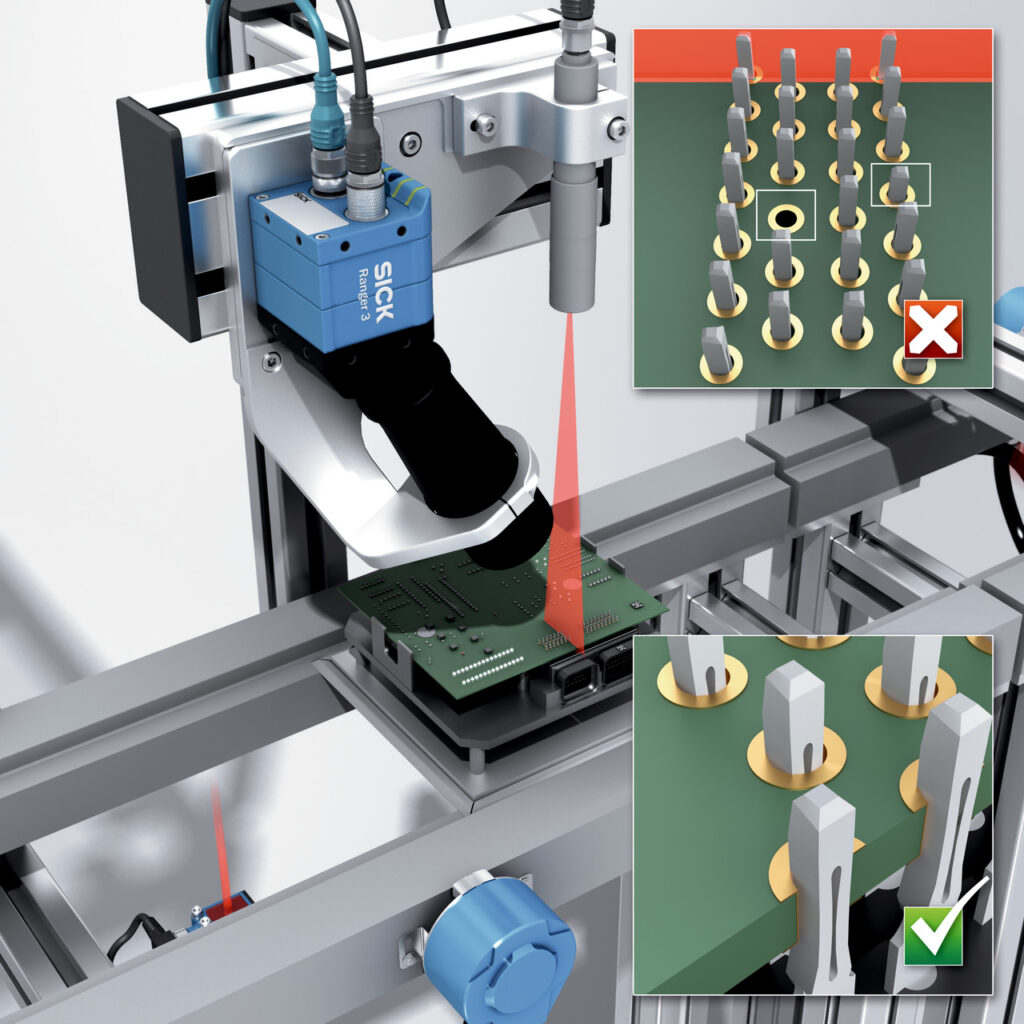
Scalability and Efficiency
SICK sensors enhance scalability and efficiency in EV battery manufacturing by automating inspection processes and providing real-time data collection and analysis. Their advanced vision systems, like the Ranger3 cameras, reduce the need for manual checks, speeding up production and ensuring consistent quality. This automation supports high production efficiency, even as manufacturing scales up.
The sensors also enable comprehensive traceability by tracking each battery from raw materials to the finished product. This ensures quick identification and resolution of issues, facilitating efficient recall processes if necessary. Additionally, SICK's scalable solutions can be adapted to different production volumes, offering flexibility for both small and large-scale operations.
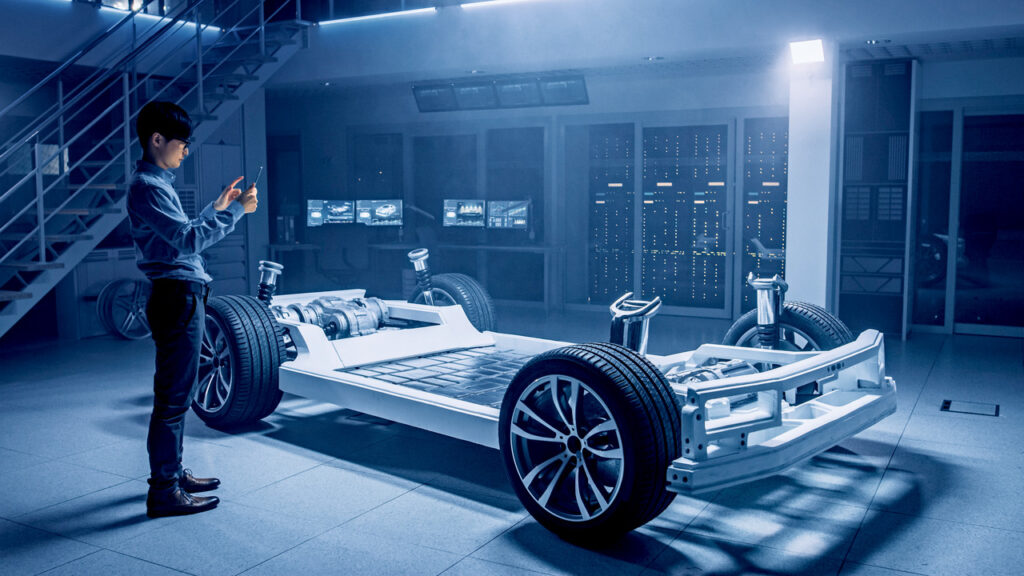
Real-time monitoring capabilities support predictive maintenance, identifying potential issues before they cause equipment failure. This proactive approach reduces unplanned downtime and extends the lifespan of manufacturing equipment. Overall, SICK sensors help manufacturers achieve scalable, efficient, and high-quality production of EV batteries, meeting growing market demands while maintaining stringent quality and safety standards.