How SICK’s SPEETEC sensor powers the CorruJET 170
In the push for sustainable packaging, retailers are turning to corrugated “ecoboxes” as a reusable alternative to plastic bags. These boxes aren’t just functional, they’re a branding opportunity, showcasing high-quality logos and designs that reflect a store’s identity. But delivering that level of print quality on corrugated board requires precision, especially when working with complex four-color digital printing.
That’s where SICK’s SPEETEC non-contact motion sensor comes in.
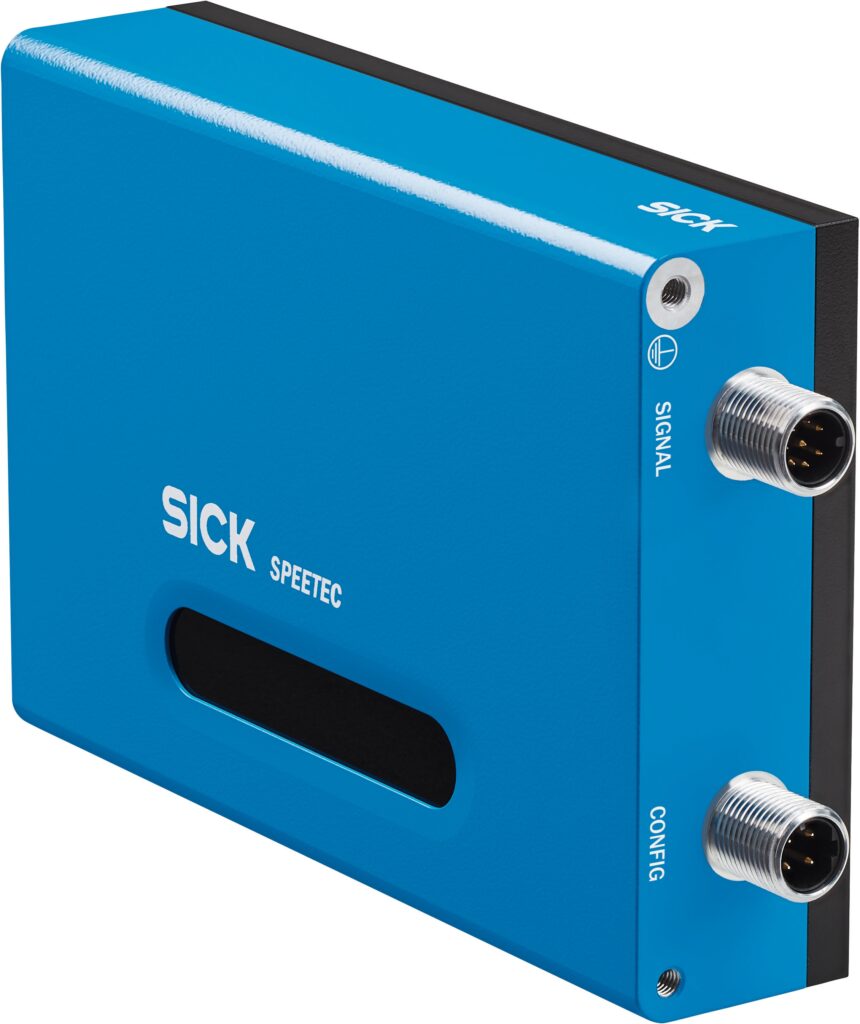
🖨️ Precision Printing with the CorruJET 170
The CorruJET 170 digital printing press, developed by Koenig & Bauer Durst, is designed specifically for the corrugated packaging industry. It handles a wide range of substrates and formats, producing small to medium batch sizes with high efficiency—up to 5,500 sheets per hour and board thicknesses up to 8 mm.
One of its standout applications? Printing ecoboxes—corrugated boxes used by retailers as a sustainable, reusable alternative to plastic bags. These boxes double as promotional tools, carrying vibrant branding and messaging directly to consumers.
“The visual quality of the print is critical,” said Oliver Baar, Senior Product Manager at Koenig & Bauer Durst. “Any misalignment in the color layers can compromise the brand image.”
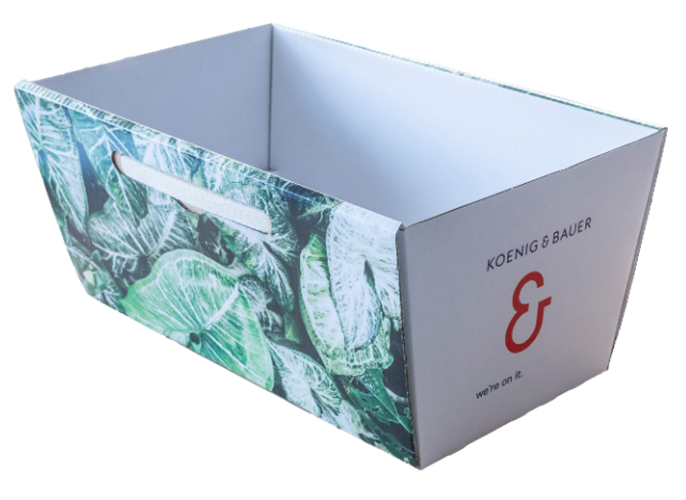
🎯 The Challenge: Accurate Color Registration
In four-color printing, each color layer must be perfectly aligned. Even slight shifts can cause blurring, shadowing, or color mismatches. To prevent this, the CorruJET 170 relies on SICK’s SPEETEC sensor to measure the movement and position of the corrugated sheets with ultra-high precision—without touching the material.
Two SPEETEC sensors are installed—one before each of the two print heads. They measure the speed of the plastic suction belt that transports the sheets, ensuring that each color layer is printed exactly where it should be.
“SPEETEC gives us the accuracy we need without interfering with the printed surface,” said Thomas Schneider, Drive Technology and Signal Processing Specialist at Koenig & Bauer Durst.
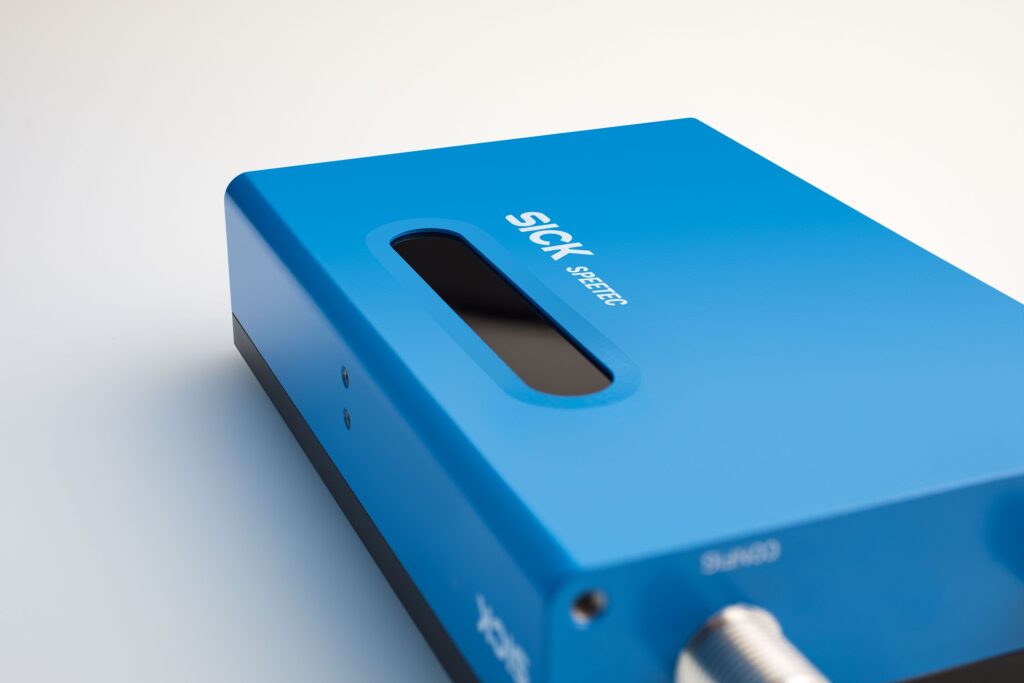
⚙️ Why SPEETEC Outperforms Other Options
Koenig & Bauer Durst evaluated three alternatives before choosing SPEETEC:
- Encoder Systems – The measurement occurs in head rollers that drive the conveyor system. These were ruled out because the encoder values alone did not provide sufficiently accurate position information due to the stretching of the plastic belt used to transport the corrugated board blanks.
- Tactile Measuring Wheels – These made contact with the printed surface and introduced errors when dropping into gaps between sheets. “This falsifies the measurement result to such an extent that precise positioning of the individual color layers on top of each cannot be reproducibly ensured,” Schneider said. “The SPEETEC with its precise position measurement, on the other hand, ensures no color shifts occur during four color printing and, as a result, the individual colors of the multi-color print are precisely registered on top of each other.”
- Laser Velocimeters – While non-contact, they use Class 3 lasers, requiring costly safety measures and complex integration. This necessitates a range of technical and organizational protective measures, and the effort and additional costs that go with these.
SPEETEC, by contrast, uses a Class 1 laser, which is safe for the eyes and doesn’t require additional safety infrastructure. It’s compact, easy to integrate, and delivers reliable, maintenance-free performance.
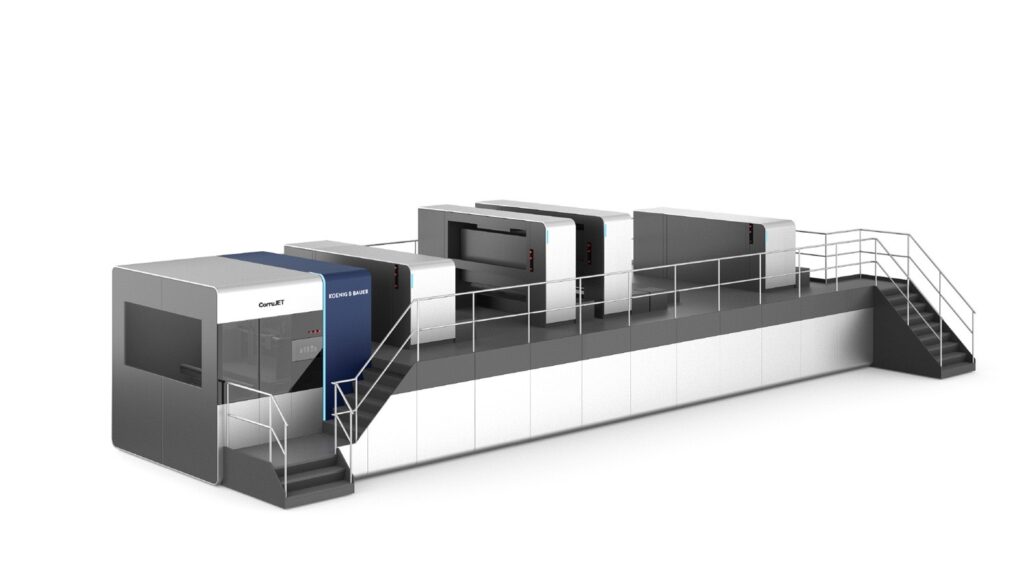
🔧 More Than a Sensor—A Development Tool
Beyond its role in the CorruJET 170, SPEETEC is also used by Koenig & Bauer Durst as a development tool for solving measurement challenges in other machine families, including analog printing systems.
“It’s proven to be a highly available and low-maintenance solution,” Schneider said. “We’re planning to use it in more of our systems moving forward.”
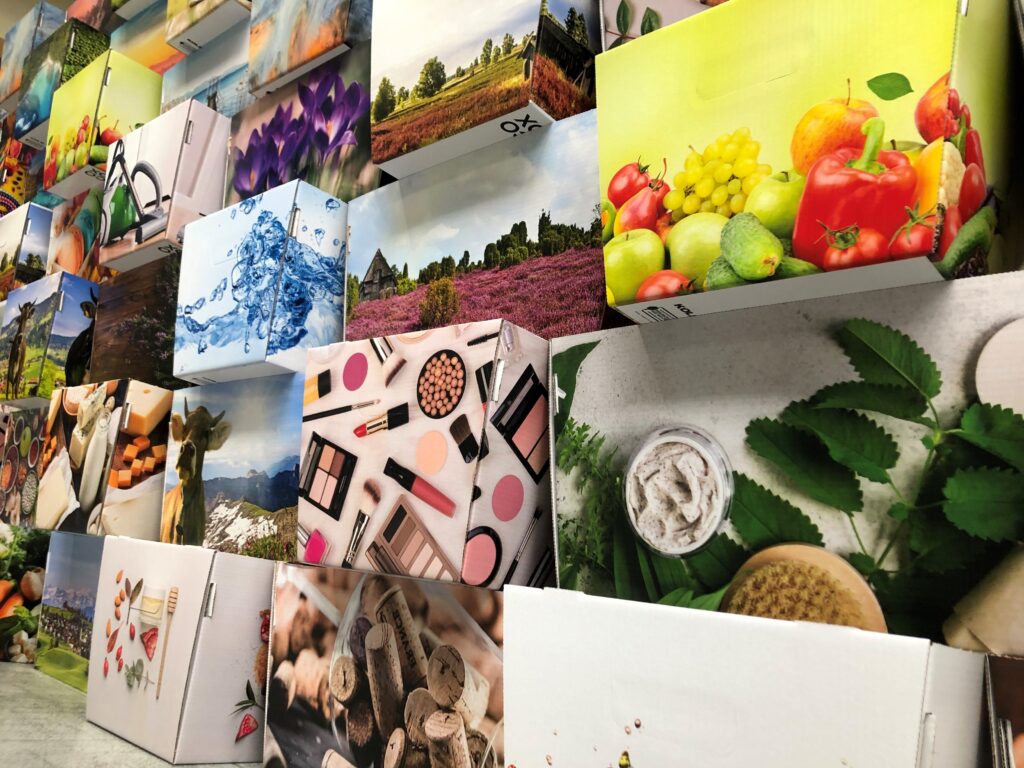
🌱 Sustainable Packaging Meets Smart Automation
As retailers and manufacturers embrace sustainable packaging, technologies like SPEETEC are helping ensure that quality and efficiency aren’t left behind. With non-contact precision and easy integration, SICK’s motion sensors are paving the way for smarter, cleaner, and more reliable printing solutions.