How cellumation and SICK are creating intelligent material flow solutions
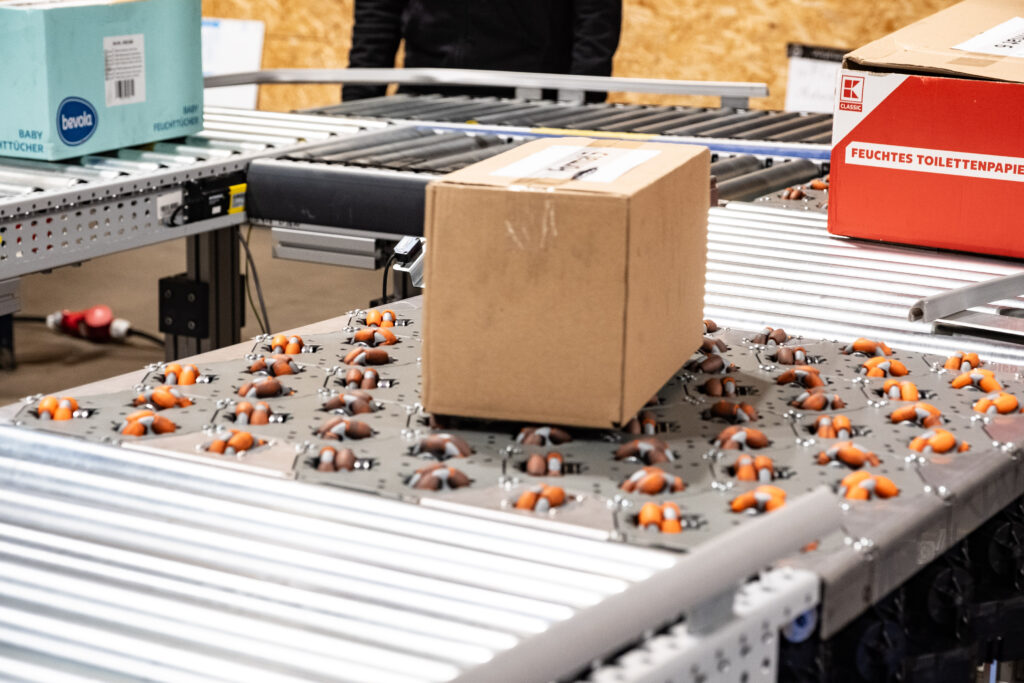
In the northern region of Germany, a revolutionary approach to robotics has been introduced that has completely transformed the landscape of material flow solutions. This innovative concept, originating from cellumation in Bremen, involves the integration of autonomous soccer robots into a single system, which is then inverted.
The brilliance of this design lies in its inversion: rather than having the robots roam freely on a surface in pursuit of a ball, powered by a trio of drives arranged in a triangle, the system is flipped over to allow for the free movement of goods on a surface. The coordinated movements of the individual robots, akin to a team effort, facilitate the highly flexible routing of various types of goods. To maintain a comprehensive overview of the operation, 3D vision cameras from SICK are employed from the sidelines.
Intelligent Material Flow
There is a market for an intelligent material flow, but it needs to satisfy two things: high-performance movement control combined with minimal space requirements.
“The floor space for logistics is shrinking and the acceptance of shared spaces falling – in particular due to the low value adding per square meter,” said Theresa Gröninger, Head Of Marketing & Business Development at cellumation, in regard to the declining push for new logistics centers at the edges of towns.
This development is countered, however, by the ongoing high volume of orders from consumers. This dilemma has led to a demand for more effective material flow solutions. The objective is simply to deliver more conveying capacity in a smaller space.
“That's where our modularly designed and, therefore, easily scalable celluveyor comes in,” Gröninger said.
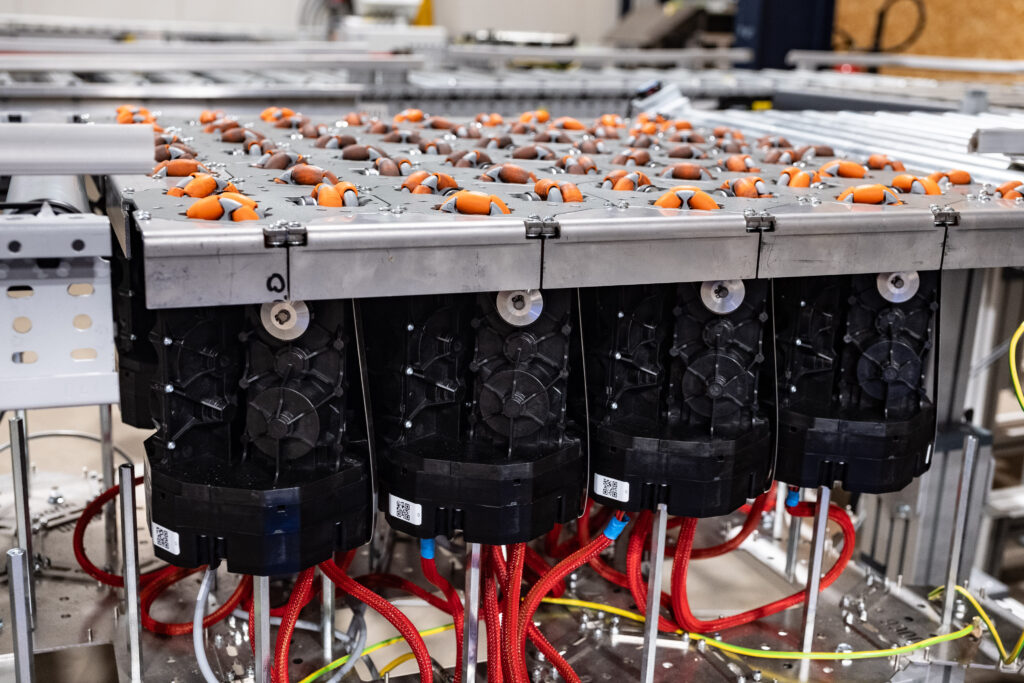
3D images for the routing on the surface
The inverted assembly of robots constitutes a transport system resembling a honeycomb structure. The number of units amalgamated for a specific application is contingent on the conveying task, the requisite capacity, and the weight of the packaging units.
To maintain a high level of standardization across the individually configurable modules, cellumation provides the individual components in merely two size and capacity variants. In terms of design, they are tailored for cell spacings of 150 and 200 mm.
The larger units are engineered to accommodate larger packages, thereby reducing the number of cells per unit area. A constant feature in both cases is the comprehensive control technology, inclusive of the connection to the Visionary-T Mini 3D time-of-flight cameras from SICK.
The unique aspect of this 3D technique is the generation of spatial vision using time-of-flight technology. Unlike conventional stereoscopy and human vision, which require two lenses, the Visionary-T Mini measures the time it takes for the camera’s infrared light to travel from the source to the object and back again after reflection, at every point on the object.
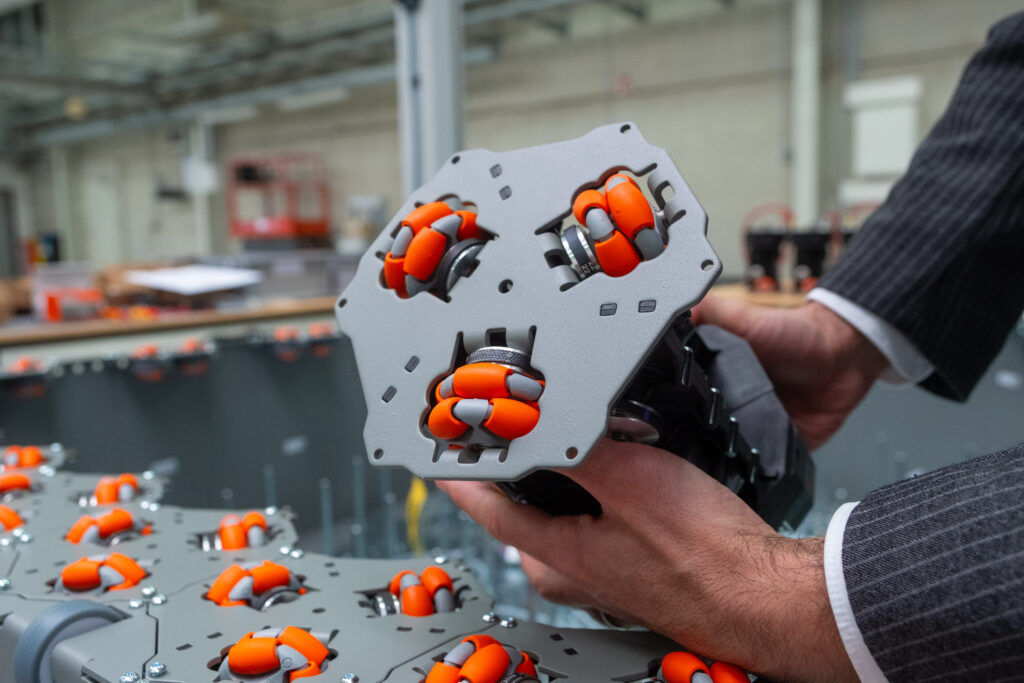
These time values, obtained from a single snapshot, enable the camera’s computational intelligence to form a 3D point cloud, which can be used to capture objects in three-dimensional space. The 3D data provide reliable information about the size and position of an object at a very specific moment in time. This level of detail sets this method apart from the operating principle of 3D laser scanners, which generate an image line by line.
From 3D LiDAR Sensors to Visionary Cameras for Industrial Use
For cellumation, this method was decisive for controlling movements on the table of the celluveyor. “3D scanners actually have a problem with moving objects,” said Claudio Uriarte, who co-founded cellumation in 2017 with Dr. Hendrik Thamer.
Both scientists were working for the Bremen Institute for Production and Logistics (BIBA) at the time. Their scientific work at BIBA – a company that belongs to the University of Bremen – involved intralogistics-related research and the search for solutions for the autonomous unloading of containers.
The company initially used 3D LiDAR sensors from SICK. Then true 3D cameras came on the market, but they were built into game consoles.
“We did a lot of work and testing with the cameras. This left us with a desire for a rugged solution for industrial use,” Uriarte said.
The two scientists stumbled across the new Visionary cameras with 3D snapshot technology in the traditional manner through a press release. That was the beginning of an intensive collaboration with SICK at a project level.
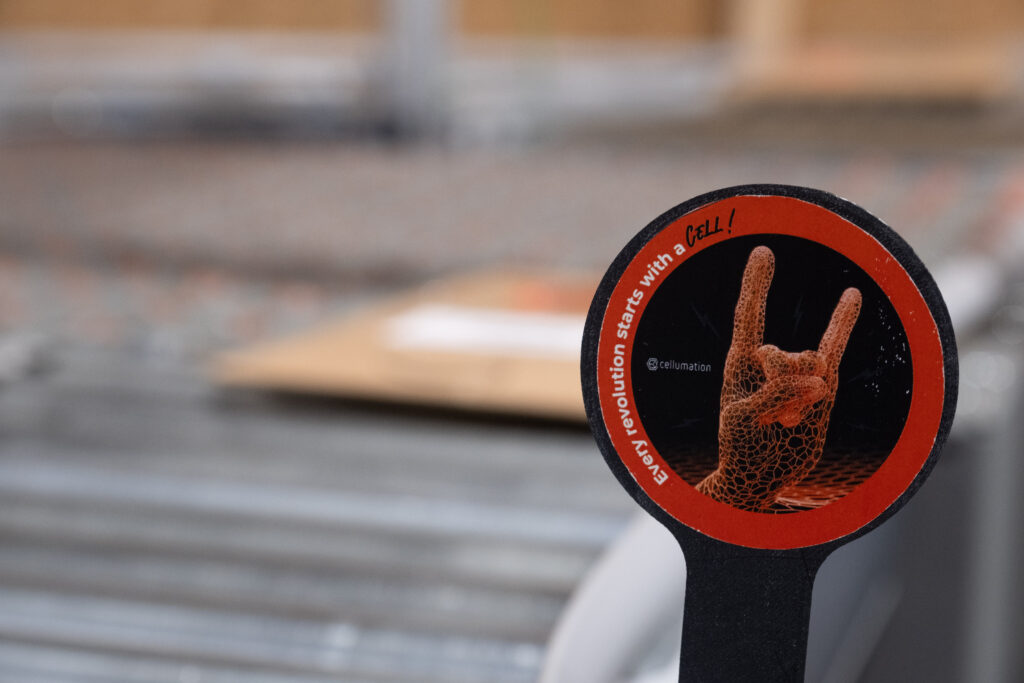
Overcoming Motion Artifacts: The Shift from Laser Scanners to 3D Cameras in Intralogistics
But what prompted the extensive search for an industrial-grade 3D camera when suitable scanners were already available? The issue was how these scanners dealt with moving objects, which are abundant in intralogistics.
Claudio Uriarte refers to a ‘tail’ that laser scanners, with their line-by-line scanning, leave behind when objects are in motion. These “motion artifacts” resemble a trailing phantom. However, with the Visionary-T Mini, these artifacts are absent, and a clear image is captured due to a single, brief exposure: the 3D snapshot.
“This allows us to capture up to 30 images per second. The data is devoid of any blur, enabling precise movement control,” Uriarte said.
In this configuration, the Visionary-T Mini serves as a rapid feedback mechanism, facilitating a swift and closed control loop. 30 images per second, each forming a three-dimensional point cloud: To prevent this measurement process from generating unmanageable data volumes, the SICK camera performs some pre-processing, which is then converted into position data by the celluveyor’s controller.
Uriarte finds it beneficial that the point cloud of 3D coordinates provided by the camera can be easily segmented.
“We can distinctly identify which data belongs to a parcel and which to the stationary table. In the post-processing, we can then eliminate everything that is irrelevant for movement control,” Uriarte said.
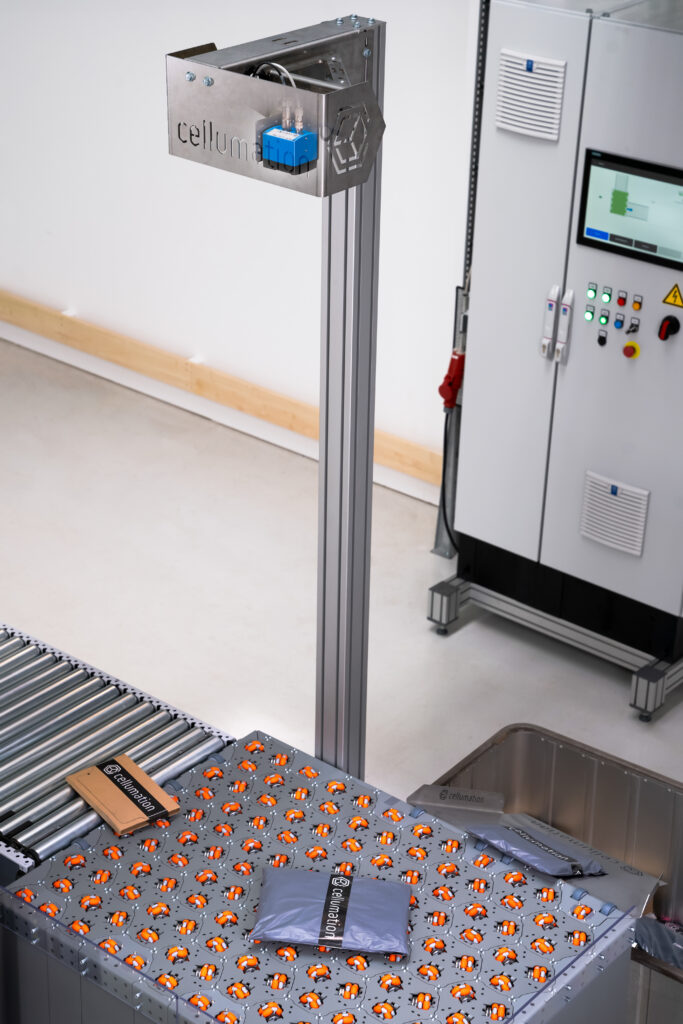
Strategic Camera Placement and Advanced 3D Technology
The company has strategically positioned the cameras directly above the distribution table. If an intralogistics application necessitates a larger module, cellumation employs a combination of cameras to ensure comprehensive monitoring of parcel movements without any blind spots.
This continuous surveillance from the 3D eye is crucial as there is no predetermined routing on the celluveyor. The unit’s controller constantly recalculates the optimal connection between the entry and exit points based on the actual positions provided.
Consequently, the celluveyor can handle multiple parcels simultaneously and even side by side. This feature contributes to the system’s reported performance. An additional benefit is that unpredictable parcel movements due to varying weights or the texture of the packaging material do not disrupt the process.
If a parcel strays from the initially calculated route, it doesn’t hinder its subsequent transport. The reason being, the controller simply recalculates the path based on the actual position provided by the Visionary-T Mini. This innovative method effectively prevents parcels from colliding or getting stuck, thereby enhancing the reliability of material flow in intralogistics, and improving overall system availability. With this arrangement of individual drive modules and 3D camera technology, cellumation has successfully built a powerhouse for intralogistics.
“Our system is ideally suited for applications that require routing decisions. We serve as an excellent addition to stationary belt or roller conveyors,” Gröninger said, discussing the market potential.
Owing to its easy integration, the Bremen-based solution can also enhance the productivity and flexibility of existing systems as part of a retrofit. Recently, the technology was honored with the “Innovation Prize Logistics” 2024 by the VDI Society for Production and Logistics. This award recognizes companies that have made significant contributions to innovation in logistics.