Leveraging a Decade of Experience to Drive Efficiency and Innovation in Battery Manufacturing
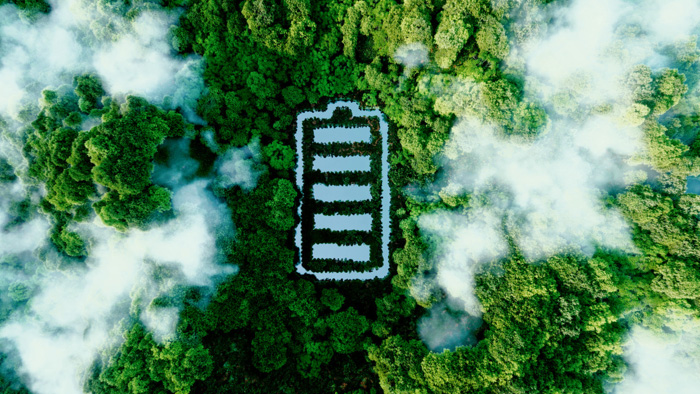
SICK has been supplying quality assurance solutions for battery manufacturing for more than ten years. The company is now using the experience it has gathered to join forces with European battery manufacturers. Because Europe wants to catch up with the strategically important battery market.
A few years ago, the West would move its production to Asia, as manufacturing costs were lower there; for its part, Asia benefited by receiving technological expertise. However, the US and Europe still maintained the upper hand from a technological perspective. This has since all changed. Asian firms are fully conversant in strategically important sectors such as battery production, and firms in Europe and the USA need to make huge efforts to stay competitive. It’s a competition between two systems.
The race is heating up in Europe, where battery production is projected to increase tenfold by 2030, reaching up to 1.5 terawatt-hours, according to Fraunhofer.
Numerous battery manufacturers, including leading Asian companies, have announced plans to build gigafactories to capture the European market. However, European firms are determined to catch up by establishing their own factories. Mastery of battery cell technology is crucial, as the complex battery, rather than the engine, is the key differentiator in electric vehicles.
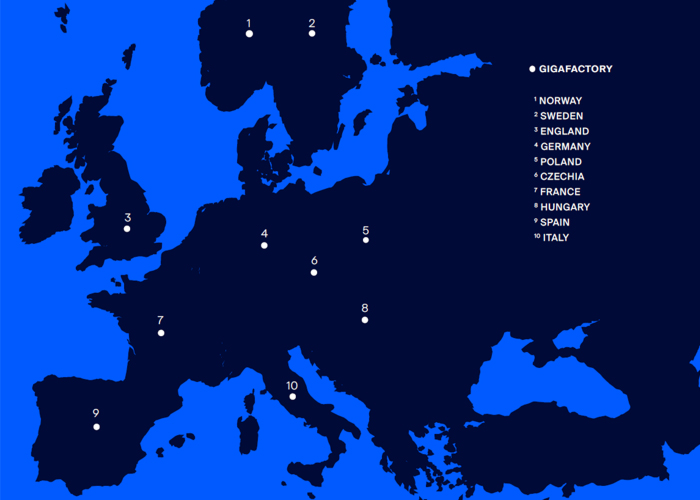
Gigafactories in Europe
To give some context, batteries must be made as close as possible to where the cars themselves are manufactured, as an automotive battery comprising hundreds of cells can soon way half a metric ton – and is also classed as hazardous cargo. It is not something that anyone wants to transport halfway around the world.
“The challenge facing Europeans is that they need to produce more efficiently than their Asian competitors,” said Philipp Mutz, Global Industry Manager for Electronics at SICK AG.
Asian manufacturers can get away with being less productive, as they enjoy cheaper access to raw materials and dominate the market. What’s more, achieving this efficiency is easier said than done. Many European manufacturers struggle with high reject rates when getting their own battery production up and running.
For over a decade, SICK has been providing automation, quality assurance, and safety engineering technology for battery production. Their journey began with an innovation aimed at smartphone batteries—the IDF double-layer sensor, which verifies the correct pickup of electrode film layers by the grabber. This sensor remains in use today, including in the production of batteries for electric vehicles, paving the way for future advancements.
Since then, SICK's technologies from various portfolio areas have been integrated into battery manufacturing. To meet the evolving demands of battery production processes, SICK continuously enhances its technologies.
For example, Surface+ offers a unique and patented solution for the final inspection of battery cells. This technology is now being adopted by European companies striving to catch up in the battery market.