Learn the steps you can take to implement AMRs successfully and automate a warehouse at scale
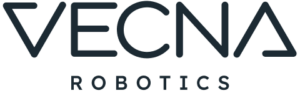
Guest Post from Vecna Robotics
In the rapidly evolving world of warehousing and logistics, businesses are seeking innovative solutions to maximize efficiency, reduce costs, and meet the increasing demands of consumers. Enter warehouse robots (Autonomous Mobile Robots, or AMRs) – a transformative solution for material handling operations. It's clear that pallet-handling robots can revolutionize warehousing, but it's important to take into account the steps and benefits of automating a warehouse at scale.
The benefits warehouse automation technology: AMRs vs AGVs
The two major players in the realm of material handling and logistics automation are Automated Mobile Robots (AMRs) and Automated Guided Vehicles (AGVs). While AGVs rely on predetermined paths, often using tracks or markers, AMRs leverage advanced sensors and AI algorithms to navigate complex environments and autonomously choose the best route. This makes AMRs more flexible and adaptive to changes in their surroundings. As industries seek greater adaptability and real-time responsiveness, the versatile navigation capabilities of AMRs offer a compelling advantage over the more fixed nature of AGVs.
Benefits of Automating with AMRs
- Efficiency and Speed: Warehouse robots can operate 24/7, reducing manual labor needs, and ensuring a consistent flow of operations. They can also move faster and more accurately than human workers, reducing the likelihood of errors.
- Scalability: Unlike fixed infrastructure solutions like conveyor belts, AMRs are easily scalable. As the business grows, more robots can be added without major changes to the existing warehouse layout. With new financing models like Robotics-as-a-Service, facilities can adjust their fleet size as needs change.
- Safety: With LiDAR (Light Detection and Ranging) sensors, onboard computing software, and mapping algorithms, AMRs can safely navigate around obstacles, reducing accidents and ensuring the safety of human workers.
- Flexibility: AMRs are characterized by their human-like capacity to interact with their surroundings. AMRs can be reprogrammed and redirected as per the changing needs of the warehouse, allowing for easy adaptation to new tasks or layouts.
Steps to Automate a Warehouse at Scale with AMRs
- Assess Current Workflow and Needs: Before introducing AMRs, it’s crucial to understand the current workflow of the warehouse. Identify bottlenecks, inefficiencies, and areas that could benefit the most from automation.
- Choose the Right AMR Solution: There are various types of AMRs available, each with its unique capabilities – from simple transport robots to complex picking robots. Select the AMR solution that aligns best with your objectives.
- Infrastructure Integration: While AMRs do not require fixed paths, they benefit from an environment optimized for their operations. This could mean clearing pathways, marking high-traffic areas, or setting up charging stations at strategic locations.
- Software Integration: AMRs work best when integrated with a Warehouse Management System (WMS). This allows for seamless coordination between the robots and the inventory system, ensuring accurate order fulfillment.
- Training Staff: Even with automation, human workers remain an essential part of the process. Train staff on how to work alongside AMRs, how to intervene if necessary, and how to maintain and troubleshoot the robots.
- Phased Implementation: Instead of a full-scale immediate implementation, consider a phased approach. Start with one section of the warehouse or a specific process. This allows for real-time learning and adjustments before scaling up.
- Regular Maintenance and Updates: Like any other machine, AMRs need regular maintenance. Additionally, keep the software updated to ensure the robots are equipped with the latest navigation algorithms and task optimization strategies.
- Feedback Loop: Continually collect data on AMR performance. This data can provide insights into areas of improvement, be it in AMR’s operation or the warehouse workflow itself.
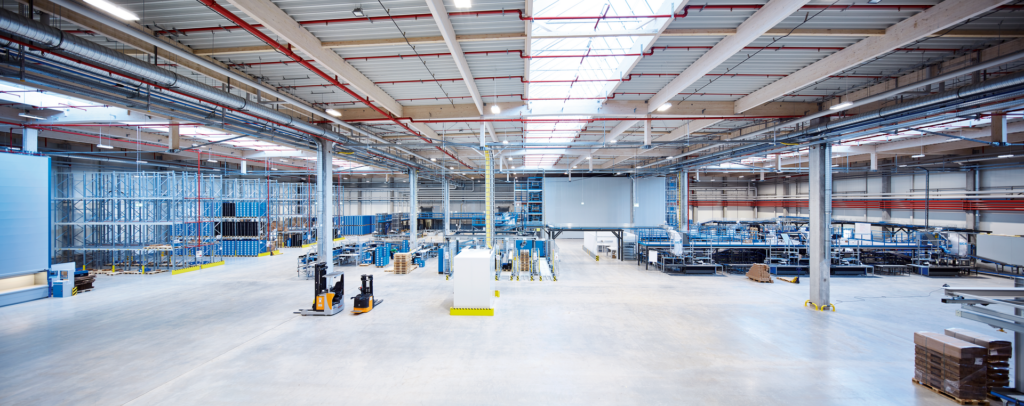
Challenges and Considerations
While AMRs promise significant advantages, they are not without challenges. Employee acceptance can be critical to the success of your investments. It's vital to address concerns and perceived job threats through transparent communication and by highlighting the collaborative role of AMRs. Be sure to choose a vendor with a robust training and assistance program to ensure a smooth transition.
The Future is Autonomous
As businesses continue to evolve in the digital age, the adoption of automated material handling equipment will grow exponentially. Warehouse automation’s ability to provide efficiency, safety, and scalability makes them invaluable assets for modern facilities.
By taking a strategic approach to their implementation and continuously seeking improvements, businesses can truly harness the power of AMRs, paving the way for a more automated and efficient future.
Learn more about autonomous technology at vecnarobotics.com, and about the safety technology that accompanies it on www.sick.com.