This Q&A is part of an ongoing collaborative robots series. Read the rest of the posts in the series.
Collaborative robots have quickly become a trending topic in the robotics industry, but how much do you really know about them?
This post covers the basics of what collaborative robots are, how they are different from service robots and other industrial robots, and the all-important question of how these robots can be safeguarded to help prevent human injury.
Q: What is a Collaborative Robot?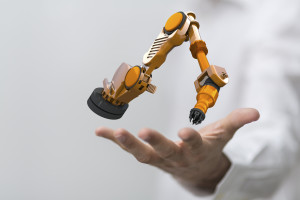
A: A collaborative robot—also referred to as a “cobot”—is defined as a “robot designed for direct interaction with a human” (ISO 8373:2.26). This interaction occurs in a defined collaborative workspace, which refers to a safeguarded area where robot and human workers can simultaneously complete production tasks.
The level of collaboration between the human worker and robot varies from robot to robot and application to application. For example, working with a collaborative robot can mean anything from simply sharing the workspace to situations where the human worker actually hand-guides the collaborative robot in order to complete a task.
In addition to interacting with humans, collaborative robots have also increased in popularity, especially among small and medium-sized businesses, due to their relatively small size and price tag. While the majority of collaborative robots are stationary, some manufacturers have designed mobile platforms to increase the mobility and versatility of these robots. Learn more about how SICK is helping make collaborative robots mobile!
Q: What are the Differences between Industrial, Collaborative, and Service Robots?
A: Unlike collaborative robots, traditional industrial robots (ISO 8373:2.9) do not interact with humans because they are large, heavy, and move at very high speeds.
Meanwhile service robots are designed to interact with humans, but they differ from collaborative robots because service robots are not intended for industrial use (ISO 8373:2.10). Instead, service robots can be used to assist humans in hospital or hotel settings, for example, rather than a manufacturing setting.
Q: Are Collaborative Robots Safe?
A: Though smaller and lighter than traditional industrial robots, collaborative robots and collaborative workspaces still need to be safeguarded to help prevent human injury. Therefore, a risk assessment needs to be performed on every robot application to determine the type(s) of safeguarding needed to reduce the safety risks to personnel.
There are 4 primary approaches to safeguarding the collaborative workspace:
1. Safety-monitored stop.
A safety-monitored stop ensures that there is no robot motion when a human worker enters the collaborative workspace. When a person enters the workspace and approaches the robot, the robot stops (keeping the drive power on), and sensors monitor the robot’s joint position(s) to make sure the robot does not move for the duration that the person is in the same space. If the stop condition is violated, a protective stop kicks in by cutting power to the robot.
When the person leaves, the robot is then able to resume autonomous operation. This not only protects the worker, but, because the power drive remains on, this solution also allows the robot to restart more quickly and autonomously when the worker leaves.
2. Hand guiding.
With hand guiding, the robot can respond to operator commands as the human worker guides the robot through a task, using an attached enabling device that senses force or displacement. The robot then moves in response to the operator commands. For example, in automotive manufacturing applications, the operator can step in and guide the robot to put seats into a car. Hand guiding is ideal for small batch production and tasks that are difficult to automate.
3. Speed and separation monitoring.
For situations where robots and humans work independently, a speed and separation monitoring solution uses safety laser scanners such as SICK’s S3000 to designate protective fields surrounding the robot. As the distance between the human worker and the robot decreases, the robot slows down.
When the separation between the robot and person drops below a set minimum distance, the robot comes to a safety-rated monitored stop. This type of safety solution allows the worker and the robot to work in the same open, fenceless workspace without stopping the robot (except when necessary to avoid human injury).
4. Power and force limiting.
Meanwhile, power and force limiting provides protection in assembly areas that require task sharing or assistance. Using a safety laser scanner* such as SICK’s S3000, a power and force limiting solution uses protective fields to limit robot speed as the worker approaches the robot.
With power and force limiting, the robot progressively slows down to a safe speed or stops at touch. This solution involves monitoring each joint and slowing down to a safe speed so the operator can interface directly with the robot.
(*Note that a safety laser scanner may not always be required, depending on the results of a risk assessment. If the robot’s operational speed is slow enough that there is no hazard from the robot, then no laser scanner is needed. Consult a safety professional.)
Learn more about SICK’s safety solutions for collaborative robots.
This blog post is meant as a guideline only and is accurate as of the time of publication. When implementing any safety measures, we recommend consulting with a safety professional.