Reliably controlling motion with encoders from SICK
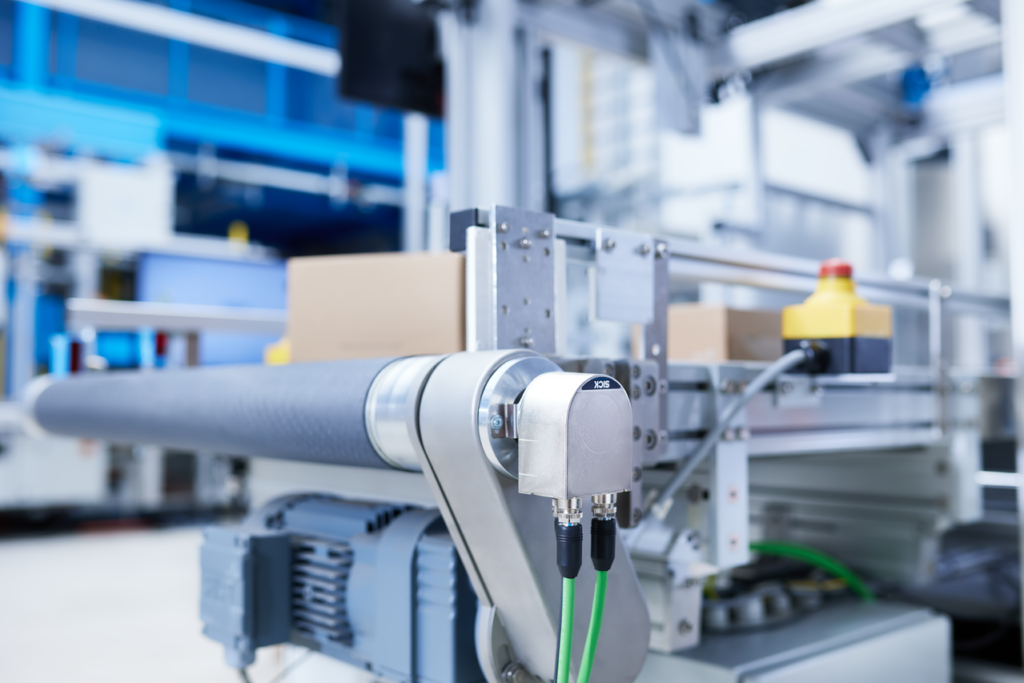
To get automation moving, something else needs to move – automatically – in machines and systems. Movement alone is not sufficient, however. Robots, packaging machines, industrial trucks, and conveyor systems, only function as desired if their movements are performed in a controlled, monitored, and reproducibly safe manner. Encoders – often invisible in electrical drive systems – take care of precisely this task. They ensure that machine movements in automated systems can be reliably controlled.
Motion control – that is what encoders are used for. They record – as linear or rotary measurement systems – positions, displacements, speeds, and directions of rotation. Using these parameters, it is possible to uniquely define and control movement sequences in most cases in industrial automation. Only then can robots accurately grip and put down objects, tools and fixtures be precisely positioned in machines, and conveyor systems and vehicles reliably perform transport tasks.
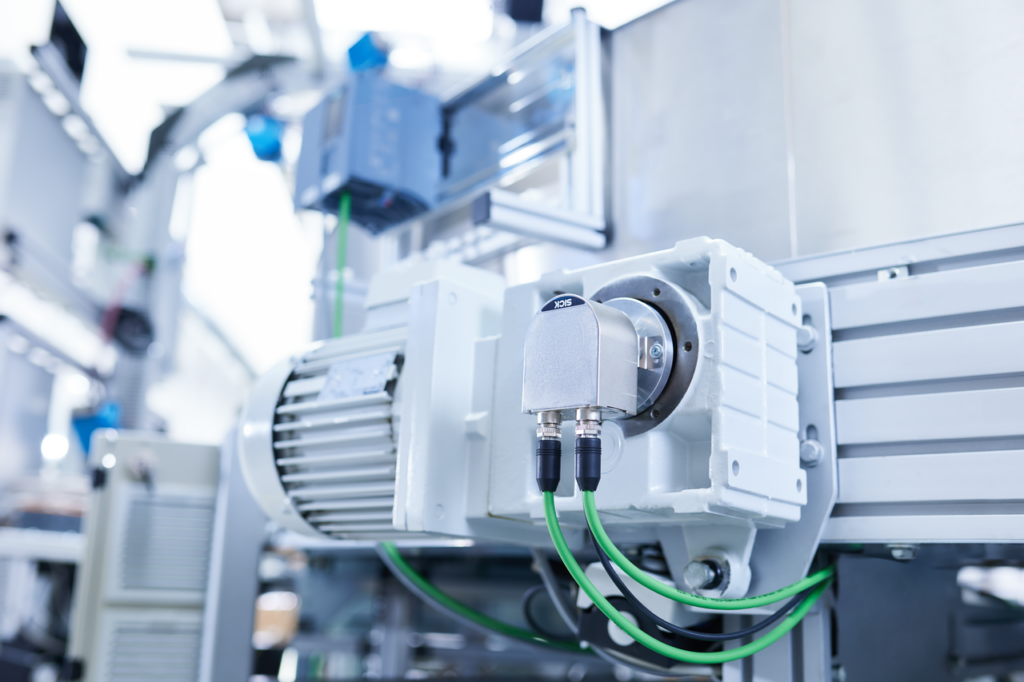
Increasing requirements for encoders
While necessary, the measurement function of encoders alone is no longer enough. Automation performance is increasing. Machines are more compact. The quality requirements on processes and products are more stringent. And there is an ongoing move toward digitalization and networking. With all this change, encoders need to offer more.
Their space-saving design and mechanical variability regarding the shaft and connection technologies are just as much in demand as their support for shorter and more precise machine cycles. This enables production rates to be increased while at the same time minimizing errors and ensuring quality.
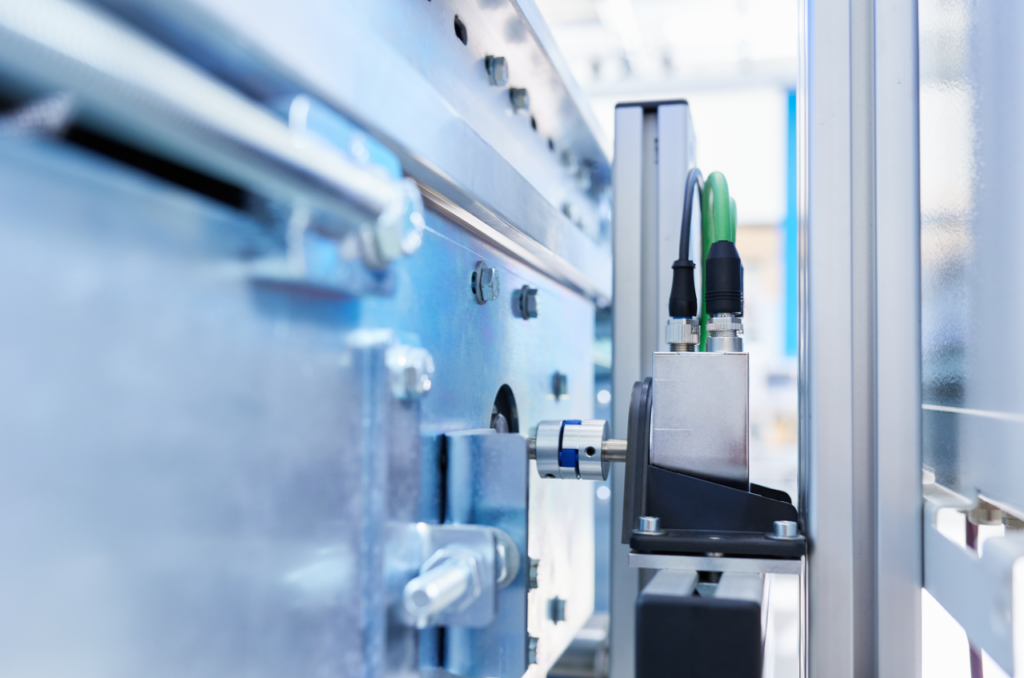
This, in turn, requires a correspondingly fast data transmission between encoders and automation systems – ideally in real time and synchronously via PROFINET IRT. The control-related integration with the help of tried-and-proven tools should be just as easy as the provision of diagnostic data for condition-based machine and system maintenance.
All these customer expectations have now made encoders a high-tech component in kinematic automation. Especially when it comes to optimizing the efficiency of machines through precise motion control while transmitting data synchronously via fieldbus in real time and in a future proof manner.
The encoder portfolio from SICK provides many linear, rotary and non-contact measurement solutions for motion control.
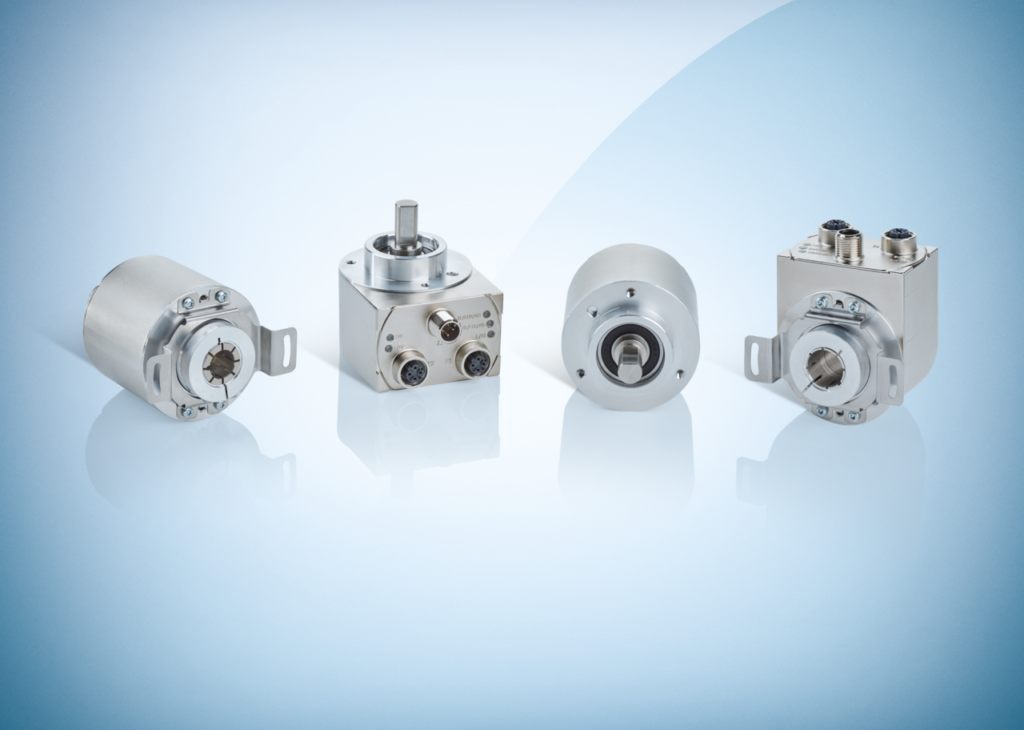
All-rounders are rare – but one does exist
High-end automation, as demanded by innovative machine builders and end-users, requires encoders that can excel in all disciplines. These kinds of all-rounders are currently rare though and, consequently, in high demand.
They are readily available, however, in the encoder portfolio of SICK thanks to the new ANS/ANM58 PROFINET absolute encoder generation, which has been designed through and through for high machine and system productivity.
The improved optical measurement system that SICK developed and manufactures in-house enables high-precision motion control, while the real-time transmission of movement and position data enables short cycle times and PROFINET IRT synchronous processes.
The compactness is best-in-class. At just 39 mm, the sensor variant with radial connection has the smallest installation depth of all encoders of this type on the market. A further plus is the many mechanical variants of the product, with a flat and narrow design, three different shaft options, and axial or radial plug variants to choose from.
These two features together offer significant advantages when mechanically integrating the device in tight and demanding installation situations. Control-related integration is simple via the Siemens TIA-Portal, while configuration of the encoder parameters can also be carried out via the SICK Engineering-Tool SOPAS.
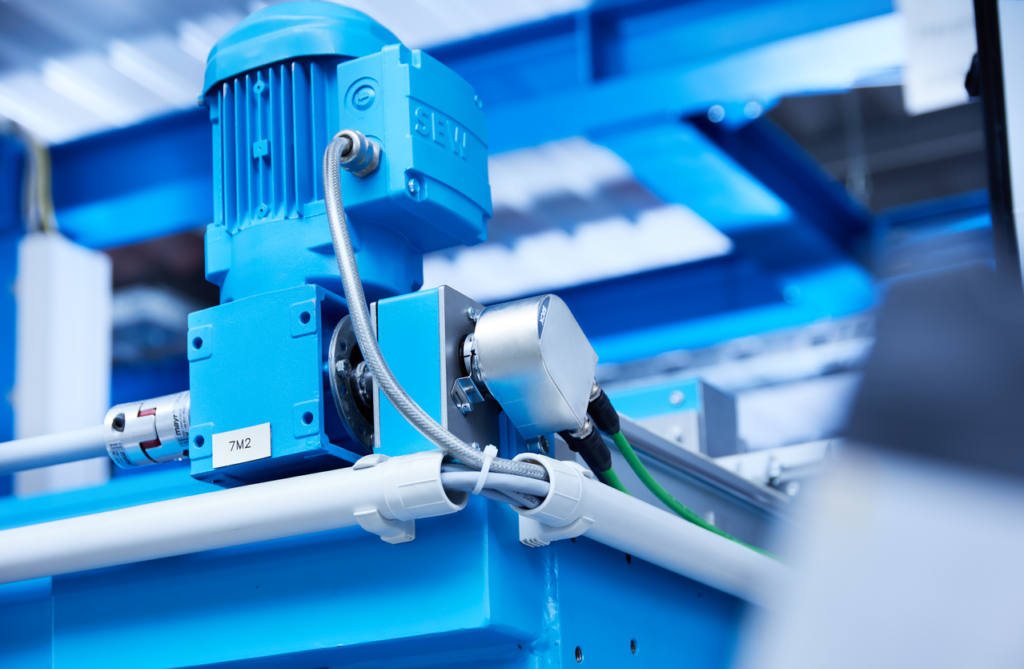
Comprehensive condition monitoring integrated
Besides highly precise measurement data for motion control, the ANS/ANM58 absolute encoders also provide relevant diagnostic data from the machine process. With data on temperatures, speeds, cycles, counters or timestamps as well, they support condition-based system maintenance.
This diagnostic data can also be used to configure application-specific limit values, using which warning thresholds for targeted maintenance and servicing measures can be set up. This makes it possible to monitor process performance, avoid unplanned machine downtimes, and increase the productivity of systems. In this way, the rotary singleturn and multiturn sensors fully cover the wide range of industrial requirements on state-of-the-art encoders.
The availability of many mechanical variants of the ANS/ANM58 PROFINET offers substantial advantages when integrating the device in demanding installation situations.
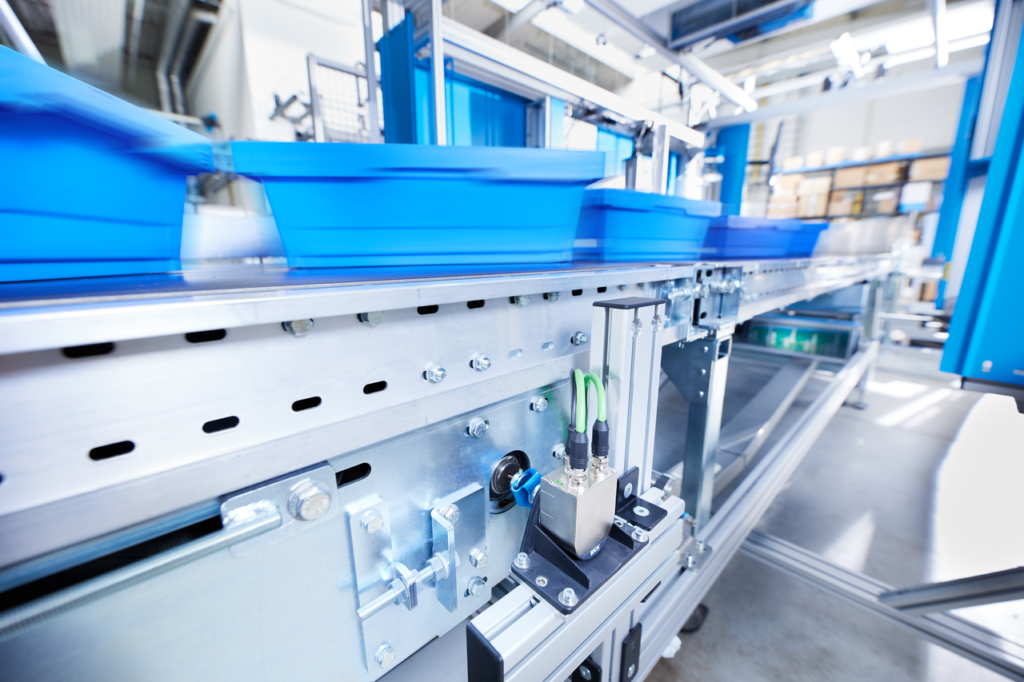
A focus on packaging technology, machine building and storage, and conveying technology
Exact position, displacement, speed or acceleration data and their real-time transmission is essential for reliable and reproducible precision movements, safe processes as well as more efficiency and productivity for drives and axes. That is why the ANS/ANM58 absolute encoder generation is used, for example, in the packaging technology of processes requiring high synchronicity.
The new encoder generation is proving itself in machine building as a means of reproducibly recording positions and measuring movements for precise machine and system control. In storage and conveying technology, it is used for the efficient automation of transport and handling processes.