Young robotics start-up and experienced sensor technology expert present novel logistics solution for safe autonomous pallet transport
Safe autonomous pallet transportation, maximum space utilization, and high process efficiency – the robotics start-up Filics has developed a double skid system for logistics applications that is setting new standards. Crucial to the success of this development is its close collaboration with SICK when using the ultra-compact nanoScan3 safety laser scanner.
“We have been working long and hard on the load carrier transportation application. While there are vertical solutions available for automated high-bay warehouses that function very well, no automation solution exists for the horizontal transportation all the way into the truck. We would like to change that,” said Julius Lutzer, COO and co-founder of Filics GmbH.
He and his start-up team intend to revolutionize ground-based pallet transportation – they are turning bulky, heteronomous industrial trucks into autonomous mobile robots (AMRs).
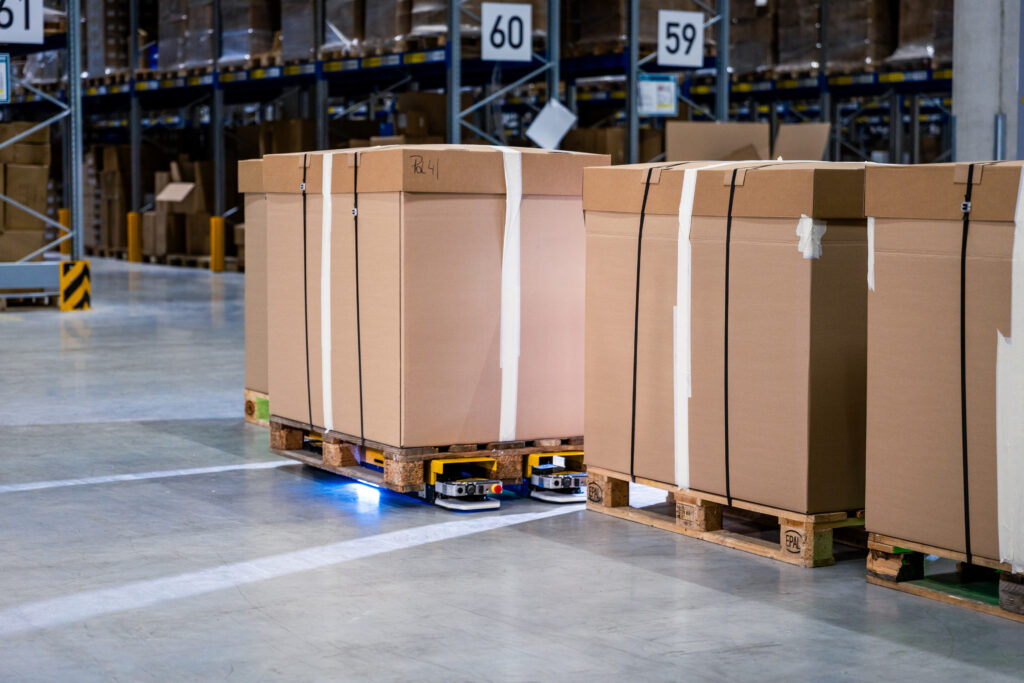
Maximum space utilization for increased productivity
In intralogistics, pallet handling in confined spaces is still largely done using manual lift trucks and manned forklifts. However, the start-up Filics views this maneuver-intensive method as a waste of valuable space.
Efficient space utilization is crucial, especially in traditional block storage systems where pallets are tightly packed. Unlike conventional methods that can only pick up and place pallets from one side, the new ‘Filics Unit' double skid system can move pallets in and out from the side. This lateral access significantly enhances the flexibility and adaptability of transportation.
The Filics Unit can be swiftly adjusted to different warehouse layouts and transportation needs, optimizing space utilization and boosting process efficiency. Additionally, the straightforward feeding of pallets ensures a continuous and efficient material flow.
To implement this innovation, Filics has eliminated the fork arms from forklift trucks and manual lift trucks. The remaining skids autonomously navigate the warehouse, drive under pallet stacks, dock, lift them, and maneuver freely.
Filics estimates that this approach reduces logistics space requirements by over one third. Additionally, it offers numerous benefits: employees can focus on value-added tasks, flexibility and productivity increase, and overall operating costs decrease.
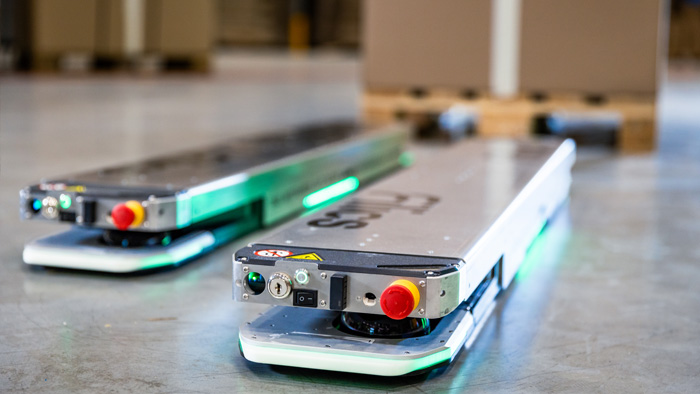
2-in-1 safety solution enables development
A crucial requirement for successful automation is maintaining a safe work environment. To achieve this, the autonomous Filics Unit needs a compact, reliable, and durable sensor solution. The integration of SICK's ultra-flat, compact nanoScan3 safety laser scanner enables the unit to pass under load carriers while ensuring the safety of both people and materials.
“In our 2-in-1 safety solution, two nanoScan3 devices have been installed under the front and rear of the skid respectively in a space-saving manner. With a height of just 80 mm, the smallest safety laser scanner from SICK is especially suitable for simple and space-saving design-in on mobile platforms,” said Klaus Beeker, Key Account Manager Mobile Platforms at SICK.
The nanoScan3 provides precise measurement data, ensuring reliable safety and accurate localization of vehicles. Key to achieving optimal speeds on these vehicles are the 128 configurable fields that protect the route up to 3 meters ahead with a 275-degree scanning angle. The more protective fields available, the more agile the vehicle's movement.
Filics engineers use SICK's free Safety Designer (SD) software to virtually configure the necessary protective fields and import them into the laser scanner. This import function allows the nanoScan3 to handle numerous fields, fine-tuning the move-in, move-through, and move-out operations.
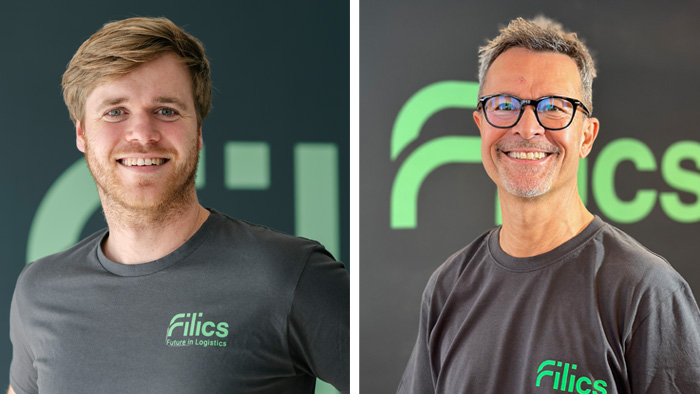
Filics Unit successfully in use at DHL
“The innovation partnership with SICK enables us to take a decisive step forward in our development efforts. Openness, creativity and an excellent understanding not only of the technologies but also of the workflows in logistics are the key to success in this collaboration,” said Helmut Schmid, CCO at Filics.
As an experienced and highly networked robotics expert for the young AMR start-up, he carefully selected SICK as a sensor partner. He is proud of the successful initial pilot applications of the Filics Unit, including at the world's biggest logistics specialist DHL. The collaboration with this logistics specialist impressively demonstrates how the advantages of the Filics Unit can come to the fore in real-life, demanding logistics environments.
For Schmid, SICK is much more than just a hardware supplier.
“We really appreciate that SICK, in contrast to many established companies, is not interested only in optimizing its core business in times of crisis like now,” Schmid said. “To create new things, you need courage and a willingness not only to recognize but also to promote opportunities.”
Filics intends to work with SICK to continuously further develop and optimize its innovations. In the next step, Filics will be particularly focusing on building up trust with suppliers and customers in a global market as the company wants to grow to further advance the automation of logistics processes.
“With SICK as an innovation partner, we have the greatest possible know-how at our side when it comes to all the challenges in safety solutions,” Schmid said.