How a packaging robot uses SICK technology to detect and package bread rolls
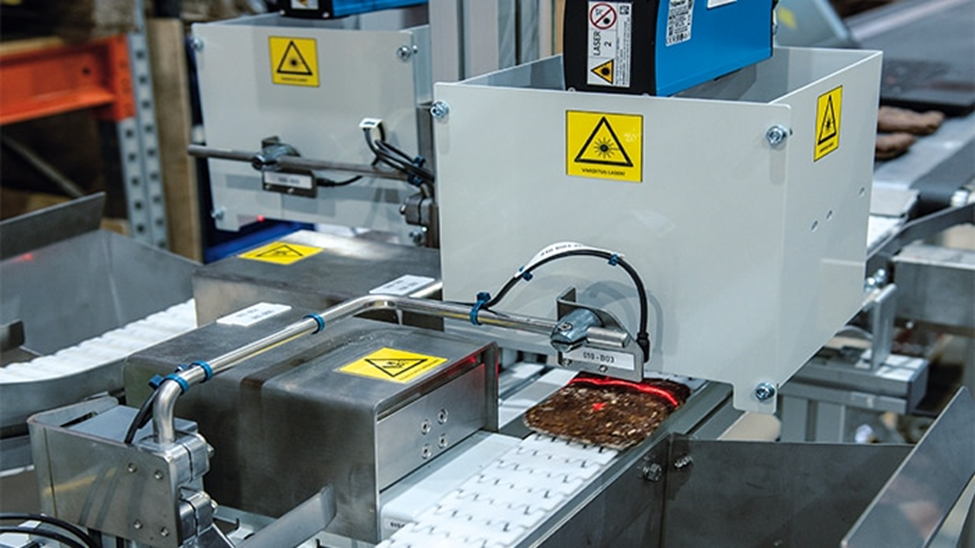
“Orfer is a family business that was founded in 1970 and is a leading supplier of automation solutions for secondary packaging and palletization in the food industry,” said Mikko Arponen, Head of Marketing at Orfer. “The first systems we developed were for the treatment of sawn timber. Having mastered the handling of piece goods, our focus [has] shifted towards the food industry.”
Orfer’s headquarters, R&D department, and production facilities are located in Orimattila, Finland with branch offices in Keuruu and Ylöjärvi as well as a subsidiary in Canada. They employ 100 specialists in automation systems and production. To date, the company has delivered almost 1,000 automation solutions in more than 20 countries.
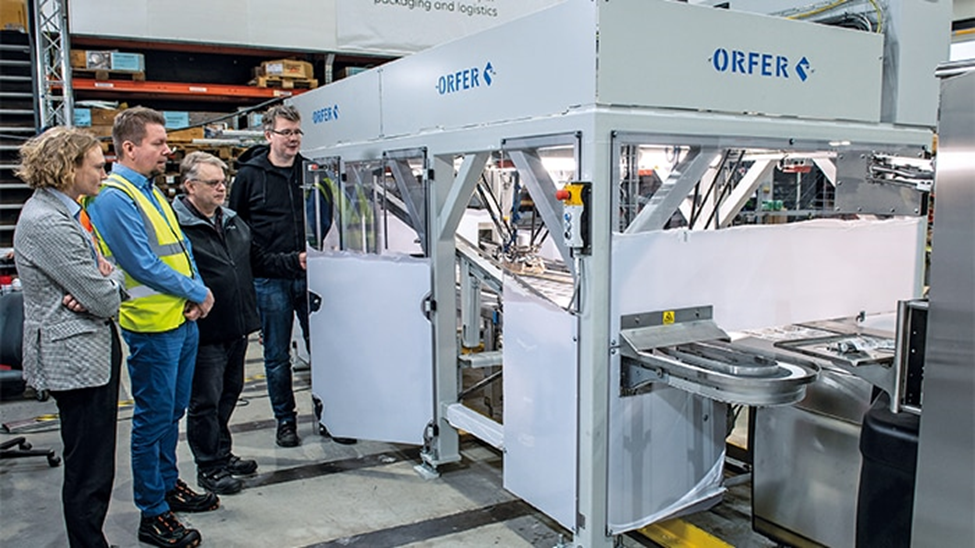
“Our systems, which are tailored to the requirements of the customer, are flexible and efficient,” Arponen said. “Automation saves packaging materials, and the optimal filling of transport units saves space and makes transport more efficient. All of this enables companies to operate in a more cost-effective and environmentally friendly manner.”
Automation in the food industry: The best thing since sliced bread
Pekan Leipä, a Finnish bread company, bakes organic rye bread. The bread is cut in half and the divided two parts are packaged into each unit before being exported to Germany and other countries around the world.
On the old packaging line, this process required a lot of manual work. More than 10,000 bread rolls per hour come out of the oven and need to be packaged.
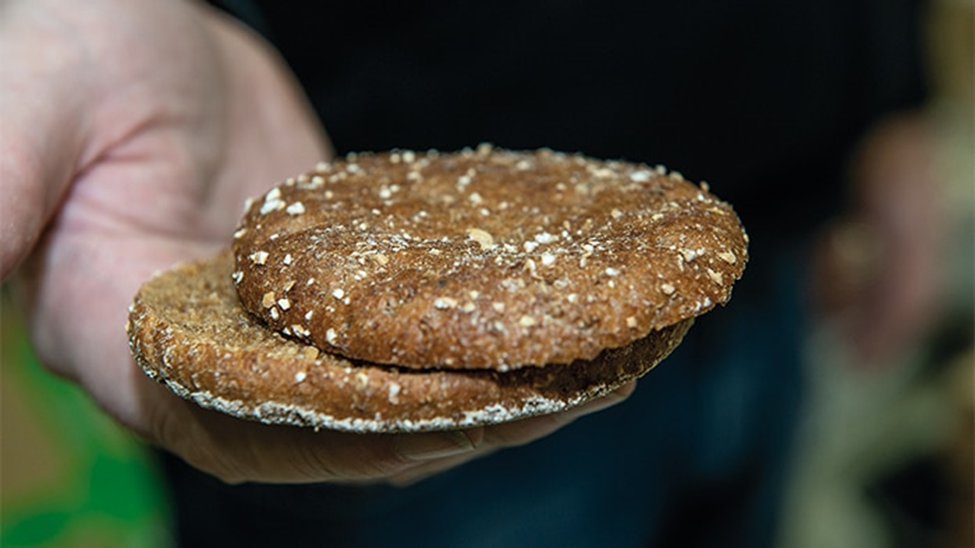
The robot from Orfer grips the divided bread roll and places the upper and lower half into a tray. The bread filled containers are then transported to the sealing machine where the packaging is covered with a protective film.
Within the solution from Orfer, a packaging robot is integrated into a German Multivac thermoforming machine. Finally, the individual packages are cut apart and transported onwards for secondary packaging.
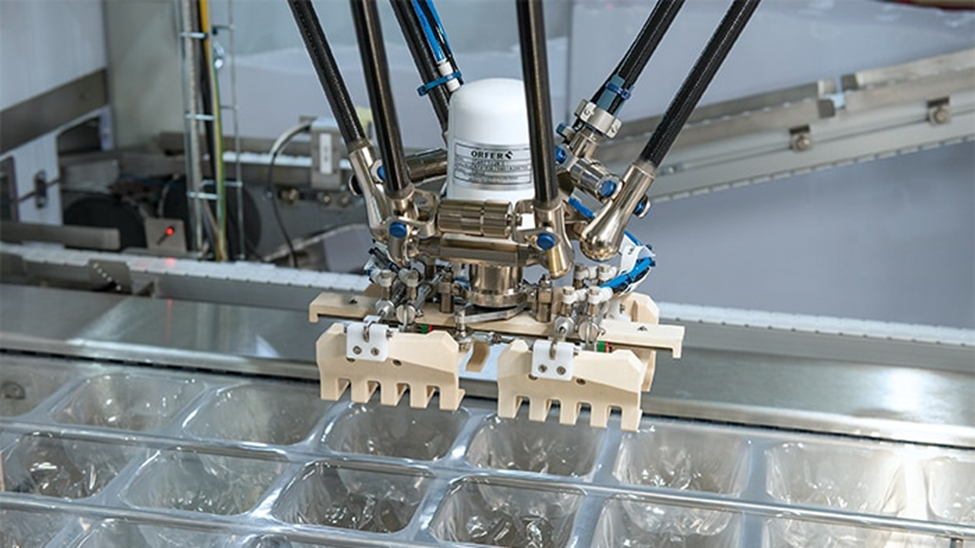
Pickup and placement of the rolls
Two conveyor belts transport several bread rolls per second into a robot cell. Three delta robots operate within this cell at a high pickup speed. The robots take the rolls from the belt and lay them in pairs into the thermoformed trays.
For the correct pickup and placement of the rolls, two halves need to be lying exactly on top of each other when they arrive at the robot cell. For this purpose, the conveyor belt is equipped with an inspection station, at the heart of which is a TriSpector1000 3D vision sensor.
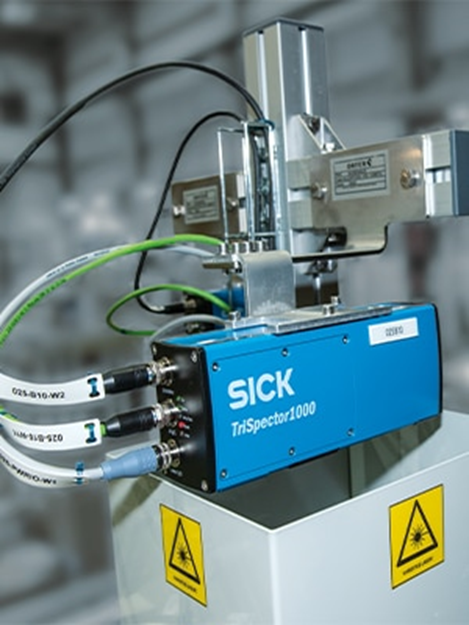
The TriSpector1000 is a configurable standalone sensor for the three-dimensional inspection of moving objects. It generates a line-by-line height profile of the object and produces a complete view based on the movement of the object. The movement information can be obtained by measuring the speed of the object or using an incremental encoder attached to the conveyor belt.
At the inspection station, the TriSpector1000 generates data on the height, length, and area of each piece of bread. If only one half of the roll is transported on the belt, its height would be too small and the roll would need fixing. If, on the other hand, the two halves of the roll overlap, i.e., they are not lying exactly on top of each other, the result would be too long of an object and would therefore be rejected. The inspection station has a pusher that pushes the rejected objects off the belt.
The Obvious Choice: SICK 3D vision
For Harri Vartiainen, who develops automation solutions for Orfer, the TriSpector1000 – along with numerous other SICK sensors that are used in the system – is an obvious choice:
“This 3D vision camera was a good and cost-effective solution for implementing this system. The colors of the products were not an issue in this application, the 3D camera has its own illumination, and it was easy to install. A 2D camera might perhaps have been a more economical alternative, however, the TriSpector1000 is very reasonably priced compared to competitor products. And the application possibilities are very, very diverse,” Vartiainen said.
Want to learn more about SICK 3D vision systems in food automation?