Averting factory fires, diminishing downtime: thermal imaging safeguards international production lines
Manufacturing electric vehicles requires close monitoring of fire hazards and the individual components that can cause them. By collaborating with infrared camera manufacturer FLIR, SICK was able to combine advanced thermography and scanning technologies to solve a pain point for one automaker.
In the race to hit ambitious global net zero targets, a further two billion electric vehicles need to be on the road by 2050, according to the International Energy Agency. And lithium-ion batteries will help power them.
But what happens if a battery turns out to be defective? Even before they are installed in a working engine, traction batteries are typically transported with a small level of charge. This is because a fully discharged battery poses problems for both the manufacturer and consumer. These problems range from lower capacity and faster depletion to electrical shorts, which can cause a fire to break out.
Regardless of where in the supply chain this occurs, unexpected ignition can cause catastrophic damage to vehicles and transport infrastructure – not to mention endanger lives.
The electric vehicles industry, therefore, has a great need for systems that detect at-risk batteries and help businesses prevent battery fires before they can cause serious damage.
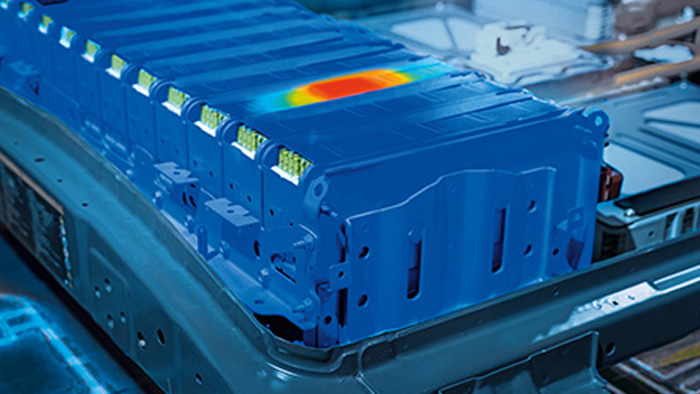
Preventing battery fires with SICK hotspot detection
A German automotive manufacturer of electric vehicles was looking for ways to detect potential issues in EV batteries on a new assembly line. They needed someone to design, test and implement an interface for identifying thermal runaway in battery production in just three months. This process would typically take over a year to see through to completion.
Having successfully developed a system that detects hot spots and potential fires on ferries and in tunnels vital to transport infrastructure, such as Switzerland’s 10.5-mile-long Gotthard Road Tunnel, SICK was a good candidate for the job. To make sure it could fulfill all the technical requirements, SICK in turn approached FLIR to supply the most suitable thermal imaging technology for the task.
The system required a bespoke interface that could accurately test each battery for thermal runaway and then export and transmit the data to a server to be cross-referenced and analyzed where anomalies had been identified.
After carefully considering the scale of the hot spots to be detected by this state-of-the-art system, SICK chose to build its new Area Hotspot Detection System (AHD) around a FLIR thermal imaging camera.
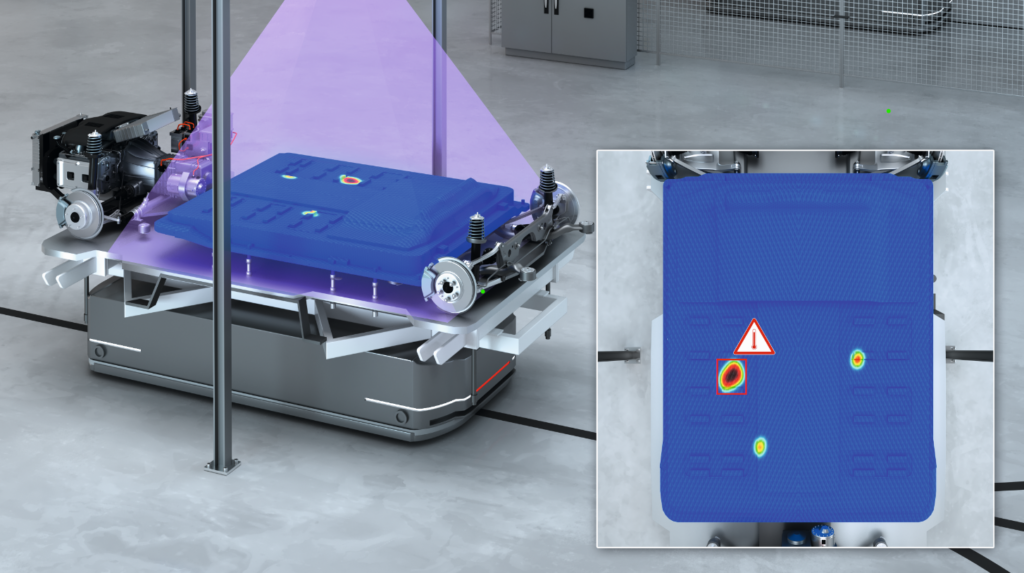
How much could one faulty battery cost the manufacturer?
“The danger here is not simply an isolated battery but the whole facility,” said Lukas Wallimann, Product Manager at SICK AG. “Just one faulty unit could cause irreparable damage to very expensive automobiles, writing them off before they’ve even left the assembly line.”
On top of that, there is the valuable machinery that would sit idle in a factory if a fire interrupts production. Every hour that a factory is off-line translates into thousands of euros in lost revenue.
To reassure the manufacturers and make the production and implementation of electrical vehicle batteries as safe as possible, the Area Hotspot Detection System goes beyond other inspection methods to accurately check every unit on the production line.
Conventional inspections such as laser thermography can only isolate and measure the temperature of battery components one at a time. The camera used in this setup, on the other hand, ensures that the Area Hotspot Detection System has a clear view of every element of each battery through infrared imaging.
This allows the Area Hotspot Detection System to view any areas with elevated heat readings as batteries pass beneath the thermal imaging camera in real time. The system alerts staff to potential problems and ensures that units measuring above the accepted temperature threshold are swiftly taken off the line and neutralized before they can cause damage—either physical or reputational.
Easy integration: superior inspection whatever the interface
The system needed to be able to communicate over PROFINET (the technical standard for data communication over Industrial Ethernet) and remotely store and share data for analysis.
Here, too, the Area Hotspot Detection System rose to the challenge. It keeps human operators involved, giving them access to information in real time that lets them make data-driven decisions based on the situation, unlike a fully automated process that could cause otherwise viable stock to be discarded.
The system can also be integrated into a higher-level system through the TCP/IP interface or into an existing system, as the PROFINET and digital input and output interfaces make it ideal for retrofitting older production lines to bring them up to speed.
Through the collaborative approach between SICK and FLIR, the automotive manufacturer received a versatile sensor system that can be integrated with a variety of systems in virtually any environment. On top of that, the tight deadline was met.