How the industry moved from magnetic line guidance to 3D LiDAR, and what SICK’s doing now
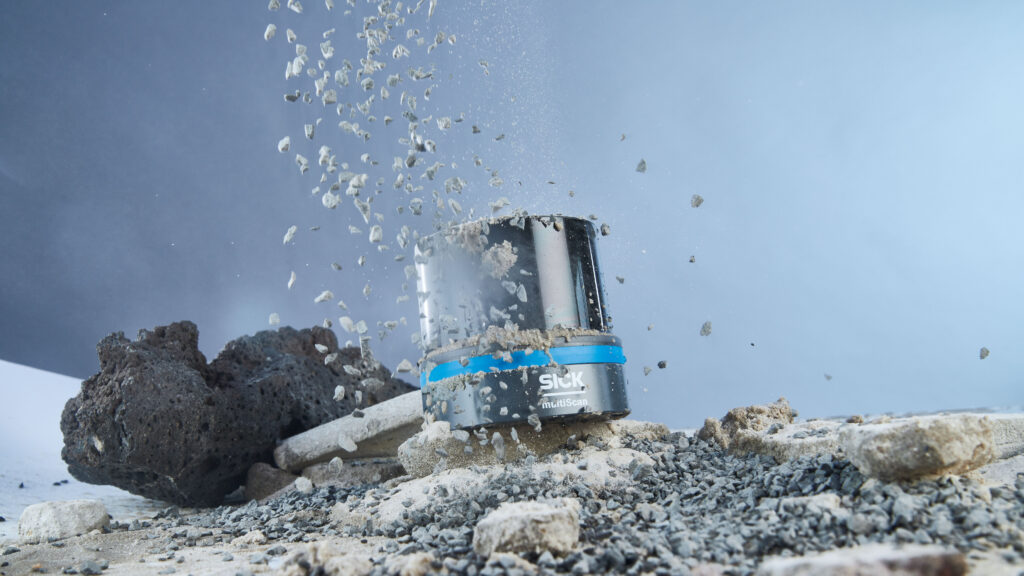
SICK’s multiScan offers a 360° field of view and the ability to “see” above and below the sensor. What makes this so great? Humans have been doing this since the dawn of time. But it hasn’t always been that way for industrial sensors. Let’s take a backwards jump for a little history lesson: LiDAR sensor functionality edition.
The beginnings of navigation and collision avoidance
Before LiDAR made a huge splash in the industrial automation scene, most AMRs and AGVs traveled via line guidance. Whether that meant a magnetic strip on the floor or a painted line, it allowed them to get from point A to point B. While this method works and is still in play today, it does limit the AGV’s movement to one specific route.
If an obstacle presents itself, the AGV must wait for the obstacle to move, as opposed to finding an alternate route around the obstacle to keep operations running. As Aaron Rothmeyer, Market Product Manager – Dynamic Ranging says, “If you're following a line on the floor, that works great until you can't see the line anymore.”
Next up: LiDAR with a constellation of reflectors. How majestic! Just like a sea captain uses the positioning of stars to figure out the location of his ship, mounted reflectors help the LiDAR on an AGV figure out where it is, based on its position relative to the reflectors. Because this is a very precise method of localization, it's still frequently used today, but it does have its drawbacks. It's a very time intensive process to plan and execute the installation.
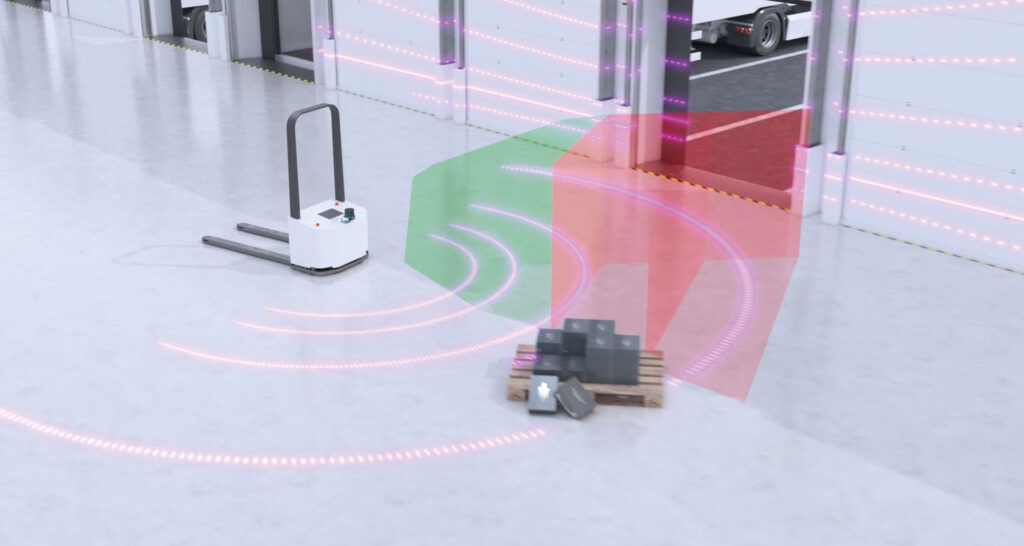
SLAM (dunk) with multiScan
Goodbye reflectors, hello natural contours. Simultaneous Location And Mapping (SLAM) deviates from the traditional LiDAR technology of line guidance and reflectors, and moves into the newest era of localization by utilizing 2D or 3D LiDAR.
So, how does 3D LiDAR operate in comparison to line guidance or a constellation of reflectors? Instead of sticking to one predefined route or using reflectors to figure out where it is, the 3D LiDAR can “sense” its actual surroundings. It’s looking for the natural contours in its space to know where it is, as opposed to manmade markers.
Being able to understand its surroundings allows more flexibility on many fronts. If the environment changes, the platform can alter its route based on the given environment, instead of needing a new magnetic line on the floor to follow or a rearranged constellation of reflectors.
This is extremely important in typical warehouse environments where a variety of obstacles (including other vehicles) can create a very dynamic environment. This saves precious time for human workers and maintains productivity, as operations do not have to halt. Because it delivers such a large amount of high-quality data, SICK’s new multiScan is a perfect pairing for SLAM algorithms.
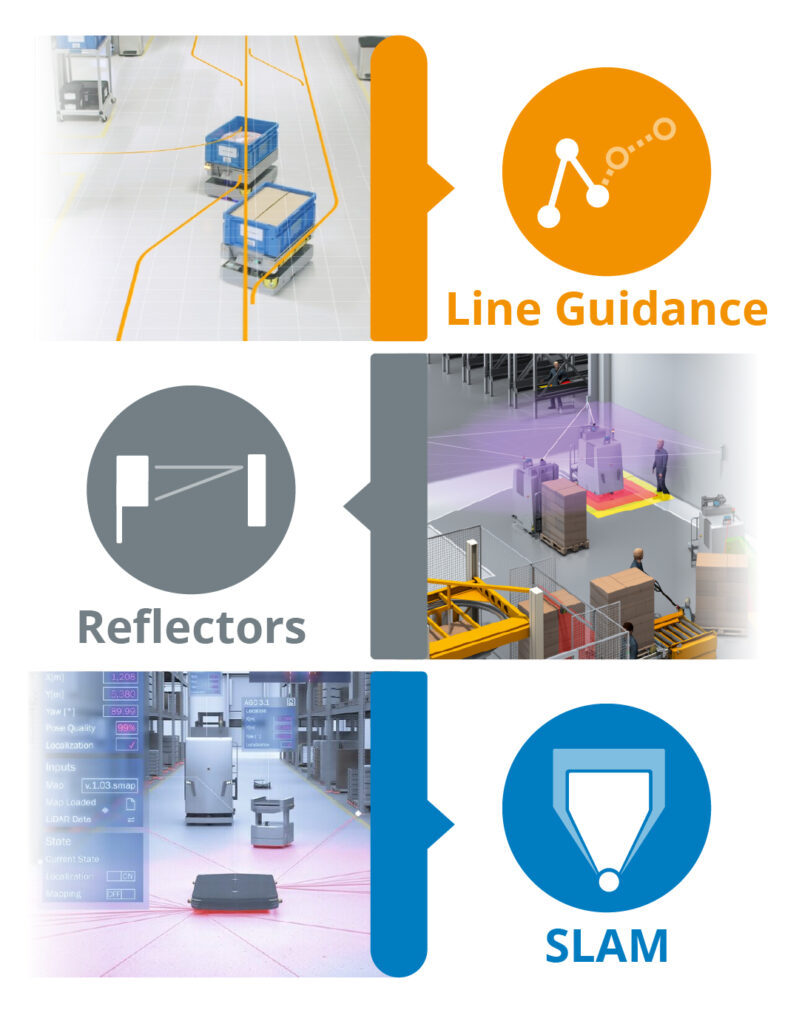
More data = better decisions
What prompted SICK to create the multiScan? Data.
“The consistent feedback [from customers] is that more data allows them [mobile platforms] to make better decisions about where they are, what’s in front of them, and what’s behind them…if we can give them 360 degrees with a wide opening angle, manufacturers can better create AGVs,” Rothmeyer said.
And that’s exactly what SICK did.
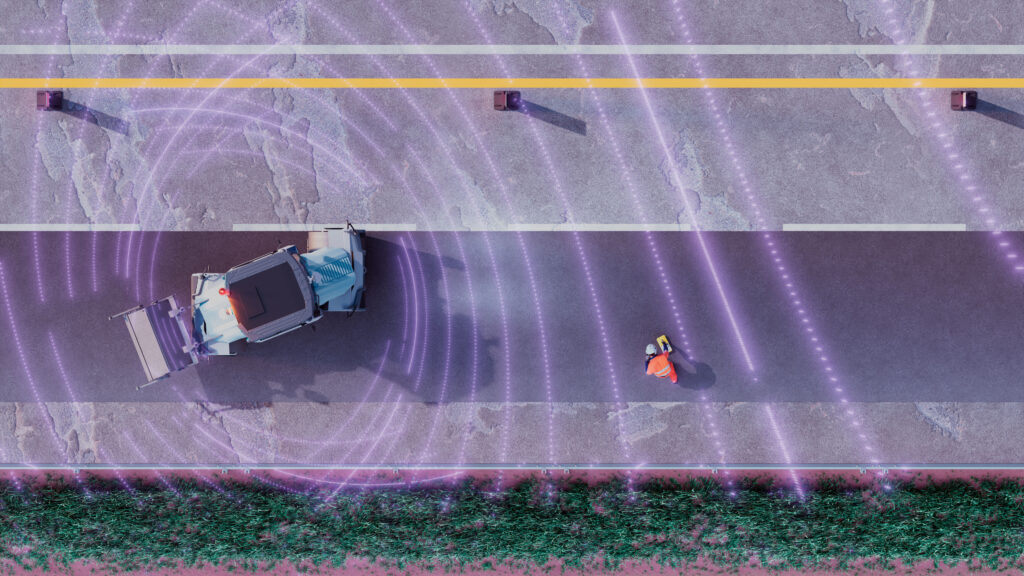
3D v 2D: What’s better?
There really isn’t a “better” option, definitively, when it comes to LiDAR. It depends on your application. Although 3D LiDAR is newer in the navigation space, 2D navigation is still a viable solution. It works great to see what’s right in front of you, but if something is above or below the sensor, you’re out of luck (and range). So, if you’d like your device to see more of its surroundings, 3D might be the way to go.
Where 2D LiDAR can see what’s right in front of it, the additional layers of 3D LiDAR can also see what’s above and below it. How is this helpful? Well, AGVs aren’t always on level ground. If they’re approaching a loading dock, the LiDAR can see that there’s a drop off. It will then move and/or stop accordingly to avoid an accidental fall.
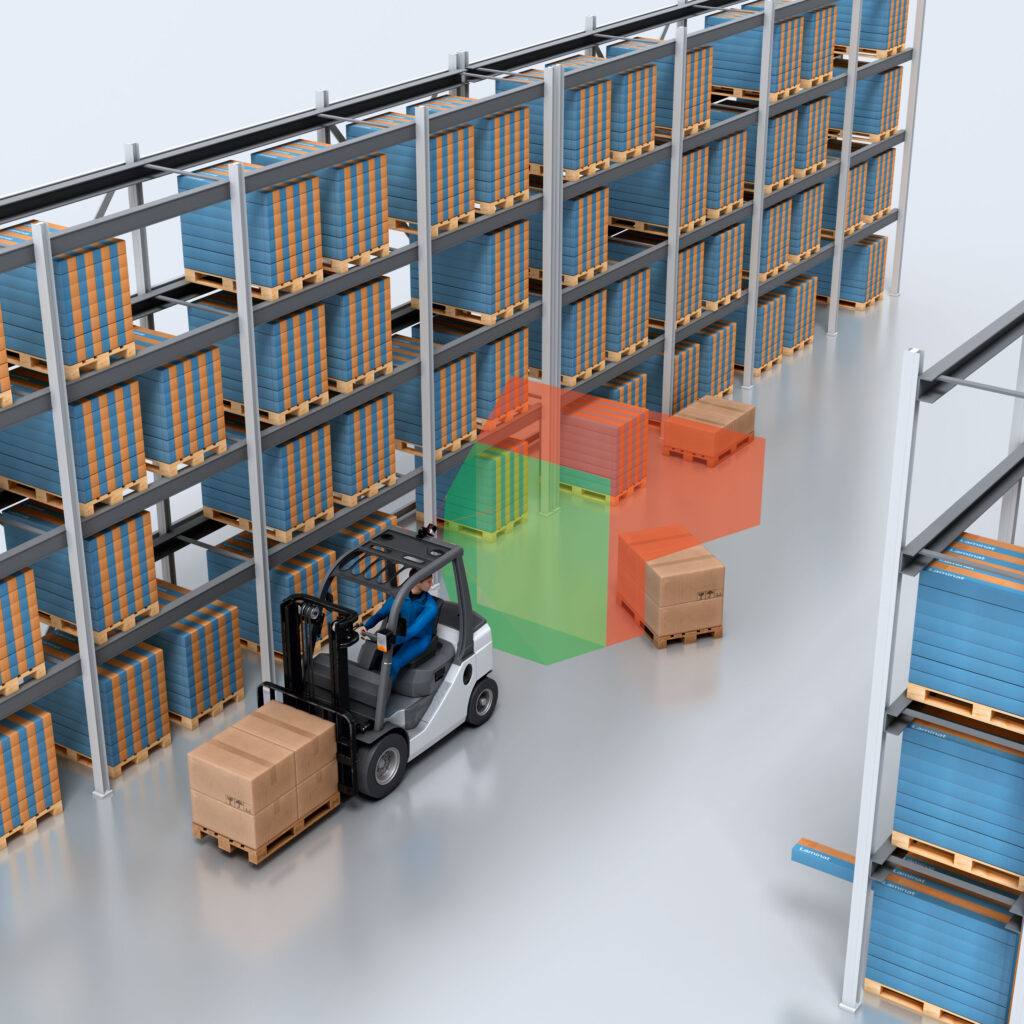
Less is more
The more layers a LiDAR device has, the better, right? Not necessarily.
Although additional layers provide more data, you may not need it all depending on your application. What’s more, it could be detrimental to your operations if you don’t have the bandwidth to handle all the data.
The multiScan offers 16 scan layers. While you can find 3D LiDAR on the market with up to 128 layers, your operations may only need, say, eight of those layers to do its job effectively. Instead of using bandwidth to process unnecessary layers, a 16-layer 3D LiDAR processes the data you need in a more efficient manner, as it doesn’t have to sort through an additional 100+ layers that aren’t needed in the first place.
To further reduce the load on the vehicle’s network and control system, the multiScan adds another important function: 3D Object Detection. All of the available layers can be used to look for objects present in user-defined zones (volumes). These volumes can easily be created in the onboard GUI.
Up to 48 of them can be monitored by the multiScan itself and objects present in the zones can be signaled to the control system through digital outputs or Ethernet messages. Using this function, the AGV can sense and avoid obstacles without further 3D point cloud evaluation.
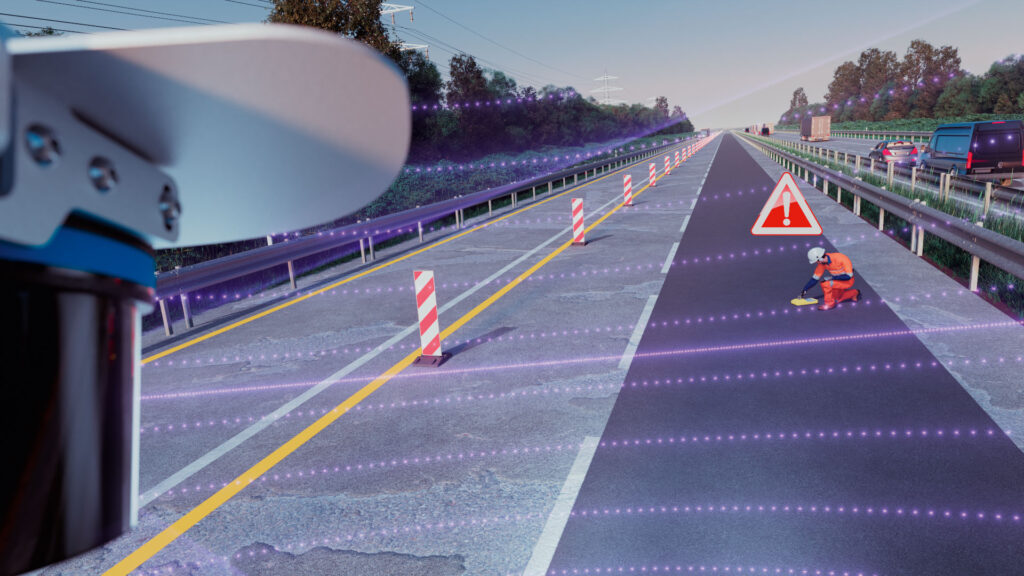
Stand up to the environment
As our world becomes more automated, mobile platforms have an increasing list of tasks and operations. This also means they’re thrown (figuratively) into a variety of environments, like the outdoors and/or cold temperatures. What the industry likes to call “ambient conditions.”
But a lot of LiDAR products aren’t equipped for such conditions! Especially chilly temps. They just stop working. Like a Floridian visiting the Midwest in a paper-thin jacket from the convenience store. It just doesn’t cut it.
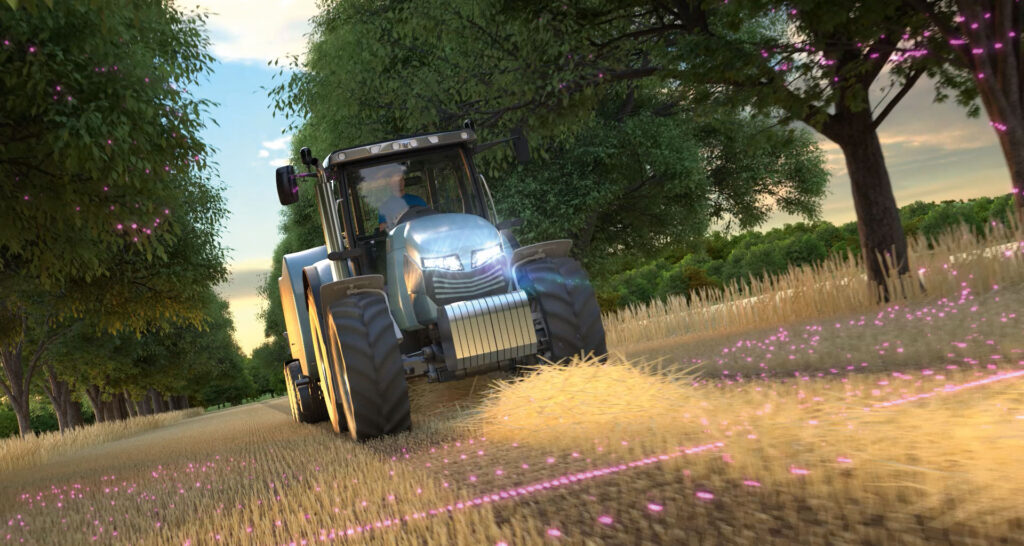
The multi-echo and IP69K advantage(s)
Fortunately, the multiScan is equipped with more than a paper-thin jacket and can easily withstand wind and weather conditions. This is thanks to its multi-echo and filter functions and IP69K enclosure rating; essentially, the Patagonia equivalent. It can actually operate within a temperature range of –30 °C to +50 °C, which makes it a great contender for working in walk-in freezers for cold storage.
More specifically, the multi-echo technology makes the multiScan a masterclass of environment perception. How? Where most LiDAR systems emit a singular beam and measure the time it takes for the laser pulse to hit an object and return (the echo), the multi-echo technology is able to enhance this process by generating multiple echoes for each laser pulse. By analyzing multiple echoes, the multiScan is better able to differentiate between genuine reflections (from objects of interest) and unwanted signals caused by raindrops, snow, fog, or dust particles.
In a similar fashion, the multi-echo technology in the multiScan also enhances accurate obstacle detection and consequently, collision avoidance, as it helps the platform better understand its surroundings. Even if the multiScan endures a few bumps and scratches or ambient hiccups, the integrated IMU helps monitor shock and damage to alert users of any maintenance needs (it also helps the multiScan to sense its position). If it’s in a dirtier environment where debris gets in the way of the camera, it alerts the user that it needs to be cleaned.
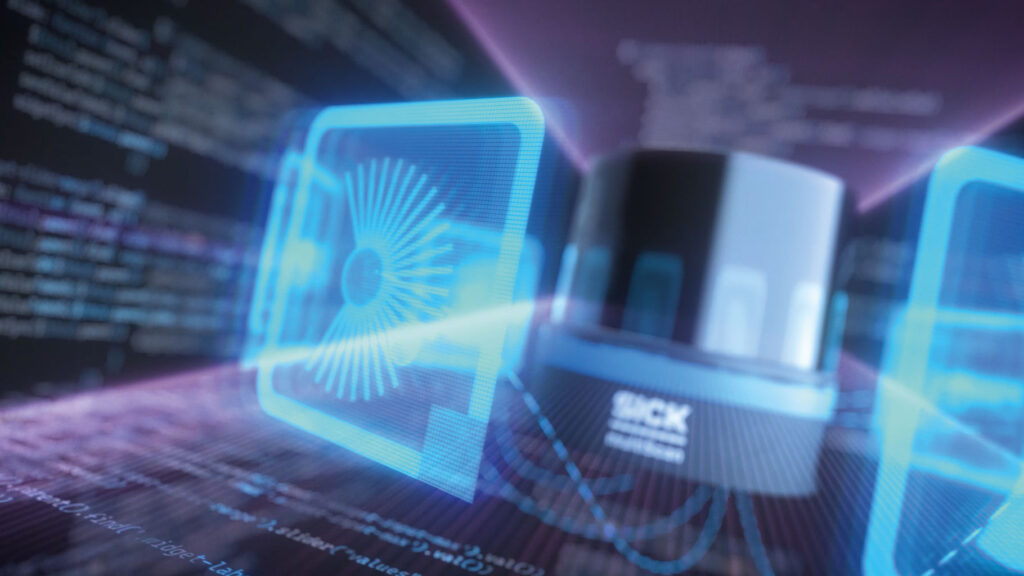
Looking Toward the Future
As we bid farewell (sort of) to the era of magnetic strips and reflectors, we welcome the dawn of 3D LiDAR—a revolution in localization and perception. SICK’s multiScan, with its panoramic view and sensing of natural contours, epitomizes this leap forward. No longer bound by predefined routes or manmade markers, AGVs and mobile platforms can adapt dynamically to their surroundings. The warehouse floor becomes a canvas of possibilities, where obstacles are mere challenges to overcome, not roadblocks.
But it’s not just about technology; it’s about data. More data empowers better decisions. SICK’s multiScan, with its 360-degree perspective, equips AGV manufacturers to create smarter, more efficient autonomous vehicles. The marriage of high-quality data and SLAM algorithms ensures productivity without compromise.
So, whether you’re navigating a bustling warehouse or exploring uncharted terrain, remember that LiDAR—whether 2D or 3D—guides us toward a future where precision meets adaptability. As the contours of our world shift, so do our possibilities. Let’s embrace the journey, one laser pulse at a time.