Robots process baggage, 3D camera makes loading quick and precise
In the Amsterdam Schiphol Airport, robots process passengers’ baggage and a 3D camera from SICK is used to make loading quicker and more precise.
The ABLE system made by AAT Automation uses robots to reliably load baggage from the conveyor system into a ULD container. To do their job, the robots need precise data about each bag’s form and position as well as the available space in the ULD container. A 3D camera from SICK delivers this data; featuring 3D snapshot technology, the Visionary-T Mini helps the system load baggage faster and more precisely.
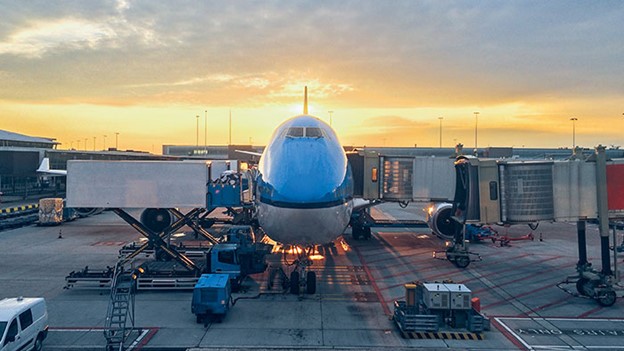
AAT’s ABLE system handles airport baggage
Day in and day out, countless pieces of baggage are loaded at airports around the world. Every hour, an average of 50 bags weighing a total of one ton are moved by a single service worker.
But there’s a better way to handle baggage at an airport: The Automated Baggage Loading Equipment system (ABLE) from AAT Automation has been demonstrating this for years. The system uses an industrial robot to take each piece of baggage from the conveyor system and place it in the waiting baggage container, removing the burden of physically demanding labor from human workers. Other systems for loading containers in operation at airports are limited, as they merely provide airport staff with lifting assistance. In contrast, the ABLE system’s robots work fully automatically. The system frees airport personnel from having to perform difficult physical labor and guards against health risks.
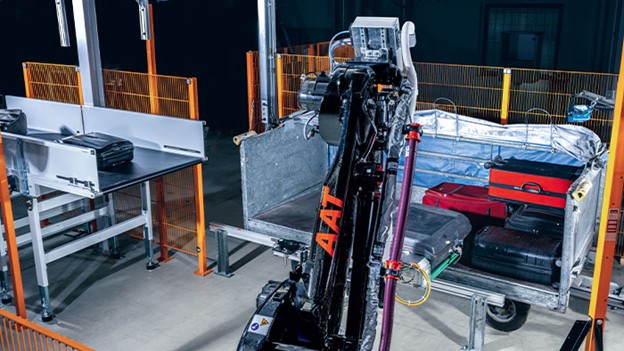
Increased precision in locating, gripping, and placement
What does it mean to deliver peak performance when loading baggage? The ABLE system must locate each piece of baggage, calculate its dimensions, and pick it up from the conveyor system. Then the system must determine the position of the ULD container and how to load it. In the final step, the robot finds a custom fit for the baggage in the container. To enable the system to work with such precision, AAT Automation started equipping it with SICK sensors several years ago.
Airport requirements are increasing, however. Processes must become more and more efficient, while the variety of goods transported increases. Further enhancements therefore became necessary to ensure the system would also work quickly and reliably in the future. Thanks to the fast and precise 3D cameras from SICK, the new generation of AAT’s ABLE system will also be able to load more baggage reliably and smoothly. The cameras will also boost precision in capturing the shape of the baggage.

Real time 3D data increases efficiency
The Visionary-T Mini 3D time-of-flight camera stands out for its performance. The 3D camera delivers up to 30 high-precision depth images per second that are ready for processing in the blink of an eye. The camera also captures the entire image area in just one “snapshot.” This eliminates the swiveling operation that was required of laser scanners, which shortens processing time.
AAT Automation has equipped the ABLE system with six Visionary-T Mini cameras. Thanks to their wide dynamic range and high 3D data quality, the cameras ensure the system quickly and accurately detects each piece of baggage, even in challenging conditions, like in a space with reflective surfaces. The compact design also allows for a wide range of installation options, thus offering a significant degree of design freedom.
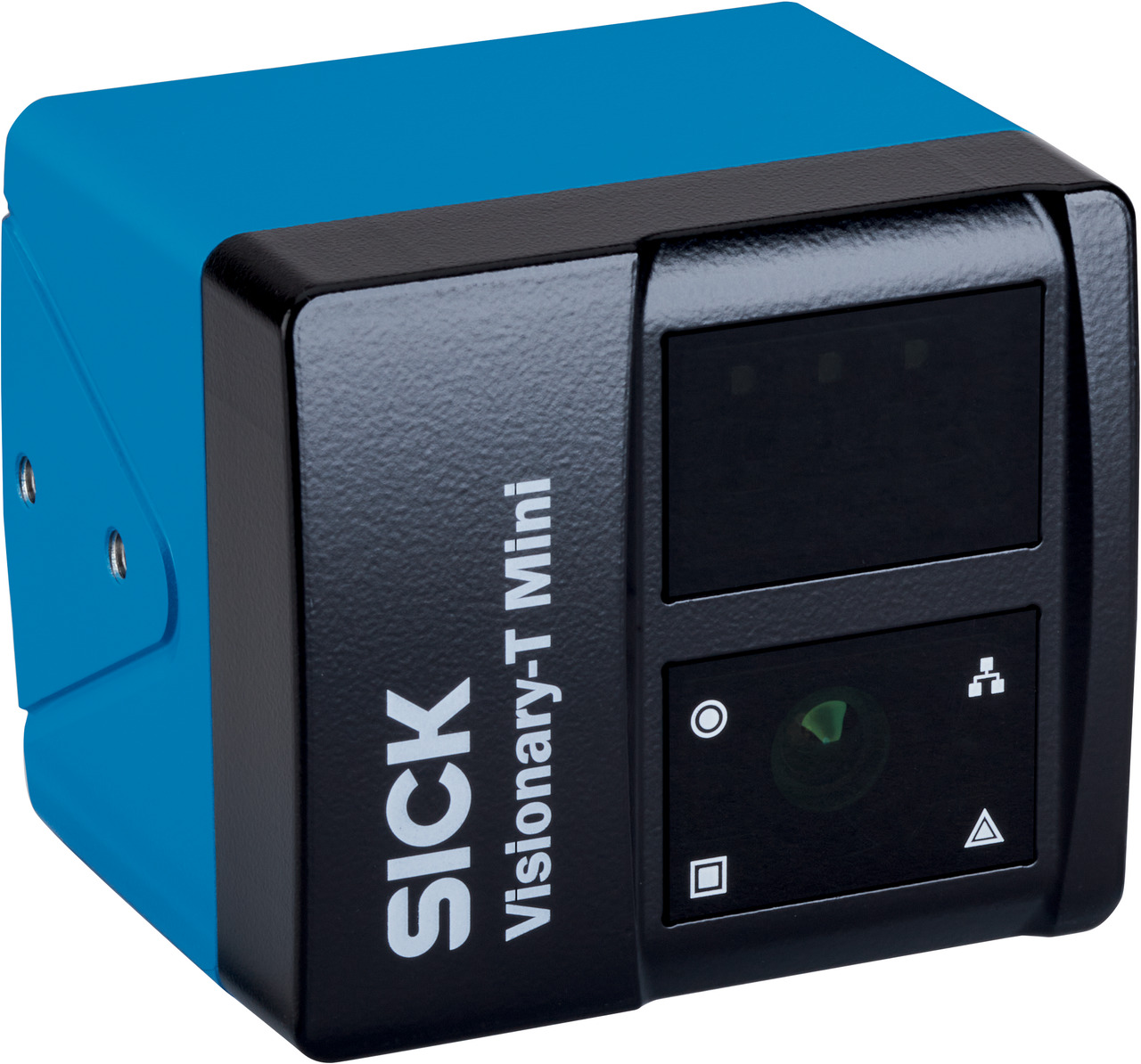
Successful partnership
For more than 25 years, AAT Automation has been delivering automation solutions in a broad range of areas, including conveyor technology, robotic systems, and mobile transport systems.
Adding the 3D cameras to the ABLE system is another example of value created by the technology partnership between SICK and AAT Automation. The collaboration offers decisive advantages for immediately addressing new business requirements with state-of-the-art technology. For future expansion, AAT Automation encourages other airports to use 3D cameras from SICK as well.