Innovative sensor solutions for battery production: Insights into cell production
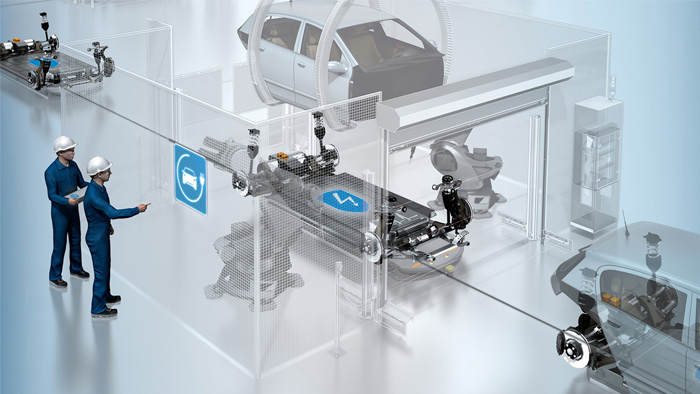
In the complex production process of batteries for electric vehicles and energy storage systems, sensors play a crucial role at numerous stations. They provide signals to control processes, safeguard assembly stations, and ensure integrated quality assurance. At SICK, manufacturers and operators can source all necessary sensors from a single provider, offering clear benefits in terms of process efficiency, safety, quality, and productivity in battery production.
Future market for battery production
In the coming years, all relevant markets are expected to see a strong increase in the production and sale of electric vehicles. Forecasts show that around 80% of new vehicles will be equipped with an electric drive by 2030. This translates into an annual requirement of batteries for approximately 60 million vehicles, which will require many more gigafactories, in addition to those that already exist.
The sale of vehicles with combustion engines is set to come to an end in the EU in 2035. In China, the largest car market, all vehicles will then be powered by “new energy.” This means that the number of batteries required by the industry will continue to rise beyond 2030. Moreover, battery systems for stationary energy storage systems will form the basis for managing the move away from fossil resources as part of the energy transition. This market will also grow strongly.
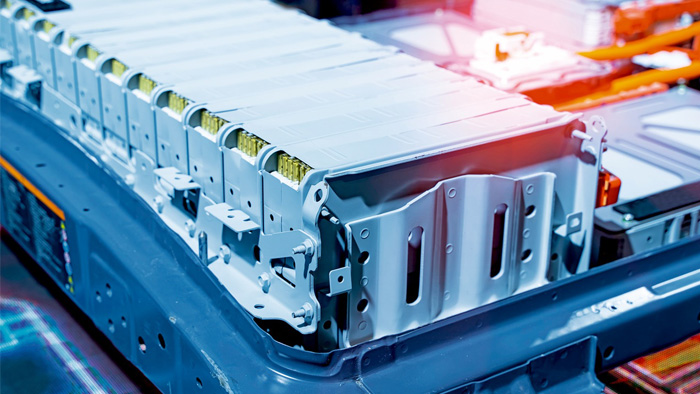
A complex process
Battery production is extremely complex. The process from the electrode to the cell and on through the module to the complete battery pack requires many individual steps and high-quality standards must be ensured at every stage. Given the quantities required, a high degree of automation is essential. The output of the gigafactories must be correspondingly high – especially as the economic pressure is high. Customers in the automotive industry expect target prices per kWh to fall steadily.
High quality without downtime
For these reasons, gigafactory operators are not only concerned with maintaining uninterrupted production runs, but they also rely on it. Avoiding rejects is crucial, meaning defects must be immediately detected and removed. This necessitates integrated quality control at each step of the process.
Finally, the machine safety standards and norms that apply at the location of the battery factory must be considered. Safety technology should not impair productivity. On the contrary, intelligent safety technology tailored precisely to the process is what creates the conditions for safe productivity.
One of the key objectives of machine manufacturers and turnkey suppliers is to offer their customers systems with stable production processes. In terms of design implementation, this means: Control processes, reduce complexity. This will – on the sensor level – be achieved using high-quality sensor technology from a single source.
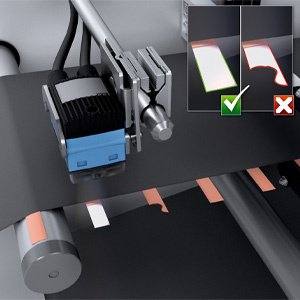
Nine application examples for sensor solutions in battery cell production
Different sensor technologies are available for many tasks in battery production, including cell production. The main components of the cell (electrode and separator foils) are processed here at high speed as roll goods.
- The deTec4 safety light curtains with Flexi Compact safety controller are ideal for access control on the high-speed winding units. Access points for logistics employees or AGV systems allow new rolls of film to be fed in and must be secured.
- Many enclosed machines are made accessible through protective doors – flexLock safety locking devices, also in combination with Flexi Compact Safety Controllers, monitor these protective doors.
- Measuring the thickness of the electrode coating at several stations – for example after calendering – requires the highest measuring frequencies (up to 80 kHz) with a measurement accuracy down to a few micrometers. OD5000 displacement measurement sensors are used here.
- The InspectorP61x 2D vision sensor can demonstrate its advantages in the process-integrated quality control of electrode arresters: Precise detection and integrated illumination in a minimal installation space enable precise distance measurements. The addition of deep learning tools directly on the camera solves extensive image pre-processing tasks for quality control.
- The OD2000 displacement measurement sensor measures the height of the rolls as they unwind and gives the signal for a roll change (residual film control) – at measuring ranges of up to 1.20 m and with a repeatability of up to 0.1 µm.
- Integrated tear and hole detection of the high-speed films is essential. This task is performed by the MLG-2 measuring automation light grid to ensure the further processing of high-quality film webs and to prevent interruptions to the process.
- Array sensors from the AS30 family are suitable for edge guiding of the electrode and separator films and, if the edges of several films are to be detected simultaneously, the MLG-2 WebChecker.
- To detect markings at the end of the film or faulty coatings, the following are used to detect the splice tape: the CSS color sensor with a large measuring distance (up to 500 mm) and the KTS Prime contrast sensor with Twin Eye technology for optimum contrast detection even with fluttering material.
- If roll-to-roll processes require precise position or speed measurement, the SPEETEC 1D laser surface motion sensor is used. The contactless measuring principle protects sensitive surfaces of the electrode material.
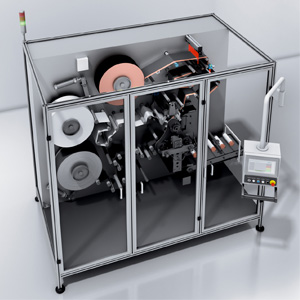
Enhancing productivity, quality, and machine safety
The sensor solutions for cell production cover the areas of productivity/system control (e.g. web edge detection, residual film control), quality (defect detection, electrode distance measurement), and machine safety (access control, protection of hazardous areas).
Sensors do not only achieve added value at sensor or machine level. Their integration into the overall control system (e.g. via Ethernet, IO-Link etc.) and into higher-level MES and ERP systems enables transparency and data availability along the entire value chain.
In addition, track and trace solutions from SICK generate data and information that enable seamless detection, identification, and tracing of the product and material in the networked process chain.
In line with the traceability created in this way, sensor and machine data become a prerequisite for data-based optimization of quality and efficiency. Sensor systems from SICK are thus an important prerequisite for highly productive and intelligent battery production in the future.